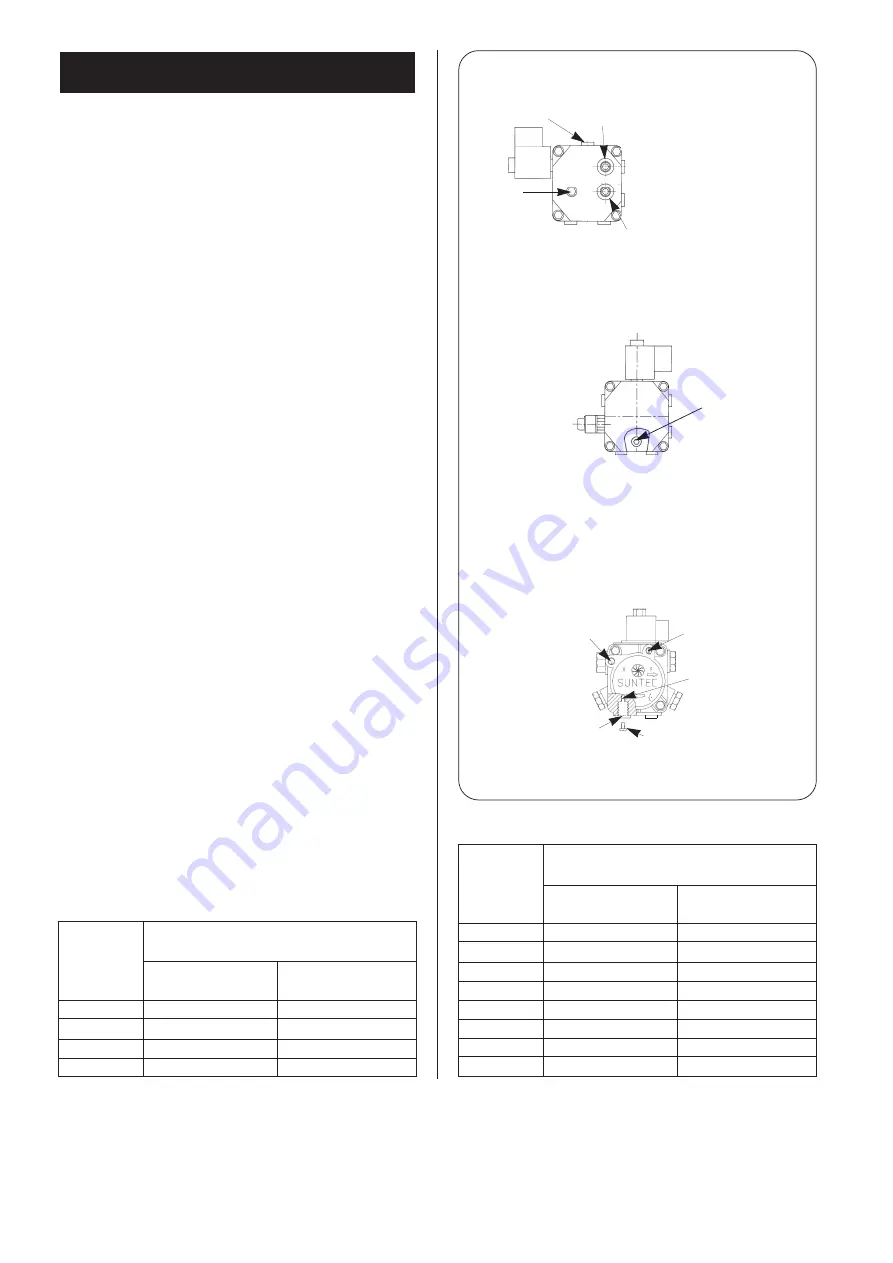
See Figs. 6 and 7.
8.1
The oil storage tank must be installed in accordance with
BS 799 Part 5. The tank should be arranged with a slope of 1 in
24 away from the outlet valve with a sludge cock at its lower
end .
8.2
Do not use galvanised steel tanks or pipework for the oil
supply system.
8.3
Do not use soldered joints on the oil supply pipework as this
could cause a hazard in the case of a fire.
8.4
The burners on all appliances are supplied so as to be
connected to a single pipe gravity feed system. Details of how to
convert the burners to a double-pipe sub-gravity feed system are
shown in Fig. 6.
8.5
If a single pipe system is employed then the tank must be
positioned such that the oil level does not exceed 4 metres
above the level of the burner oil pump and in addition the oil
level must be at least 0.3 metres above the level of the oil pump.
Should it prove impossible to site the tank below the 4 metres
maximum oil level a head breaking device must be installed
between the tank and the burner.
8.6
If a double pipe system is used then the maximum suction
height allowable is 3.5 metres.
8.7
The oil supply pipe diameter can be determined using Tables
7 and 8 depending on whether a single or double pipe system is
being installed. Selection of the correct pipe diameter will
depend on the position of the oil storage tank relative to the
burner and the length of the pipe run.
8.8
The oil supply pipe should be laid as level as possible to
avoid air pockets and unnecessary friction losses.
8.9
The following components should be fitted in the fuel line
between the storage tank and burner.
1.
A manual isolating valve installed as close to the tank as
possible.
2.
A fire valve in accordance with BS799: Part 2 as shown in Fig.
7.
The fire valve should be fitted externally with a fire
detection element located within the appliance case. Use of a
capillary type valve will allow a neat and simple installation.
A suitable valve is the KBB manufactured by Teddington
Controls Limited. A spring clip has been provided behind the
electrical panel shown in Fig. 2 to allow a fire valve element
to be mounted. Alternatively a fusible link or electrical
system may be used. Under no circumstances should a
combination isolating/fire valve be used as the sole fire
protection device.
3.
A paper element filter complying with the requirements of
BS799, Parts 2, 3 and 4 should be fitted in the fuel line between
the isolating valve and the burner and as near to the latter as
possible.
8. Oil Supply
7
Fig. 6. Oil Pump.
(b) Danfoss BFP 11 Oil Pump.
(a) Danfoss BFP 41.
(c) Suntec AS47C Oil Pump.
Cartridge filter
1
2
3
4
4a
5
6
1
2
3
4
5
6
1 INLET
2 RETURN
3 BLEED AND PRESSURE
GAUGE PORT
4 VACUUM GAUGE PORT
5 PRESSURE ADJUSTMENT
6 NOZZLE OUTLET
To convert to a double pipe system, remove plug 4a and insert the
grub screw provided into the threaded hole. Connect flow and
return pipes to (1) and (2).
To convert to a double pipe system: Remove the pump front
cover, remove the changeover screw (A) nearest to ports 1 and 2,
and the horseshoe washer underneath. Replace the changeover
screw back into the threaded hole. Connect the flow and return
pipes to 1 and 2.
Note:
When removing the pump front cover ensure that a suitable
receptacle is placed below the pump to catch the oil residue.
To convert to a double pipe system, remove the return port plug (2)
and insert the grub screw (A) provided into the threaded hole (B).
Connect flow and return pipes to (1) and (2).
1
2
3
3
6
4
5
B
A
TABLE 7 Single Pipe Gravity Feed System
MAXIMUM ALLOWABLE PIPE RUN
HEAD (metres)
(metres)
8 mm inside dia. pipe 10 mm inside dia. pipe
(10 mm O.D. copper)
(12 mm O.D. copper)
0.5
10
20
1.0
20
40
1.5
40
80
2.0
60
100
TABLE 8 Double Pipe Sub-Gravity Feed System
MAXIMUM ALLOWABLE PIPE RUN
HEAD (metres)
(metres)
8 mm inside dia. pipe 10 mm inside dia. pipe
(10 mm O.D. copper)
(12 mm O.D. copper)
0
35
100
0.5
30
100
1.0
25
100
1.5
20
85
2.0
15
70
2.5
11
50
3.0
8
30
3.5
6
20
A
Summary of Contents for 70/90
Page 19: ...19 NOTES ...