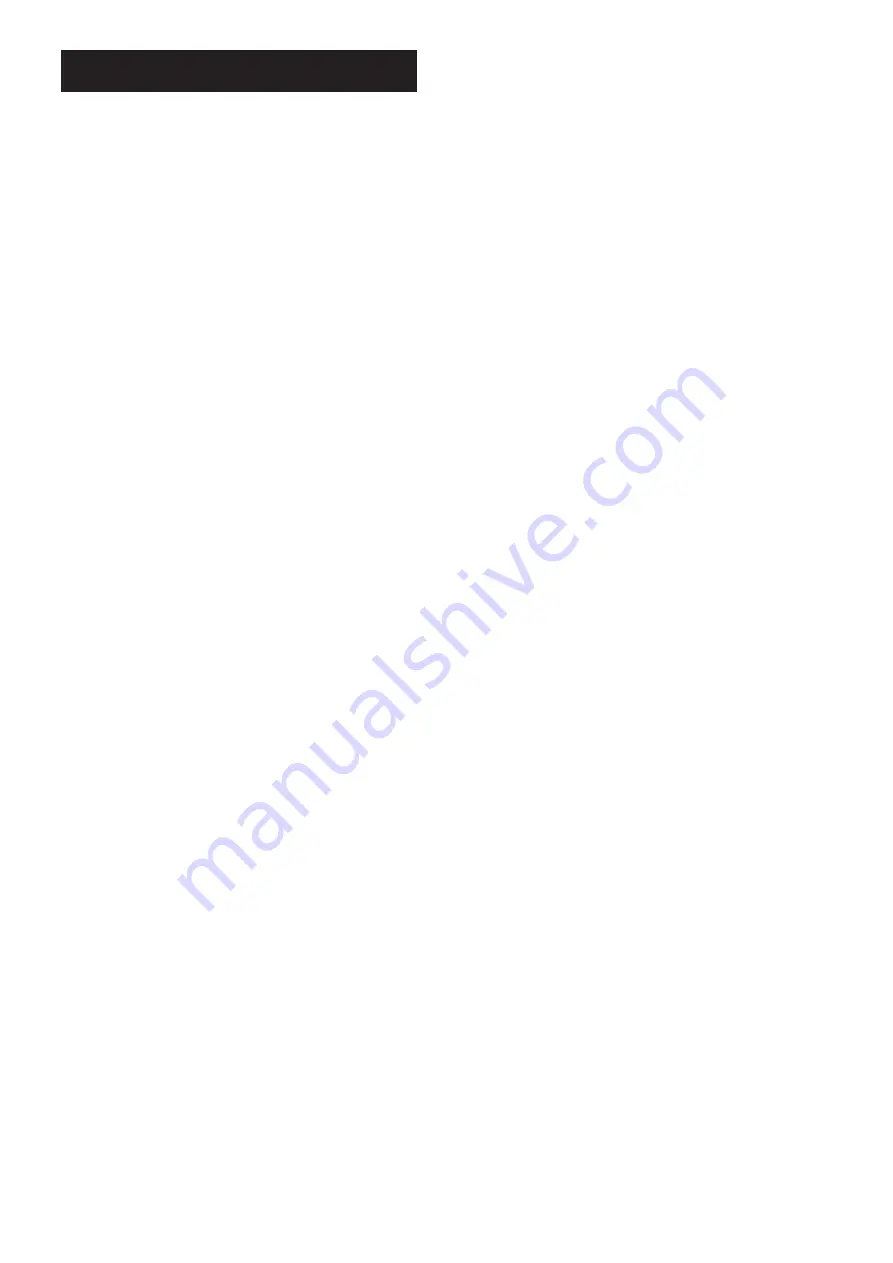
13
A qualified engineer must commission the appliance before
handing over to the user.
Ensure that no foreign matter is left in the system as this could
cause damage to the appliance.
12.1
Check that the electrical supply to the appliance is
switched off.
12.2
When commissioning the appliance after initial installation
follow the procedure from 12.3, otherwise remove the burner
first as described in section 14.3.
12.3 Prepare the heating system
1.
After initial installation and checking for leaks, as previously
described, drain down the system sufficiently to add a flushing
agent. Flush the system in accordance with BS 7593:1992.
2.
Refill the system
12.4 Check the Burner
1.
Check that the nozzle and electrode settings are correct for
the relevant burner. (See Figs. 13, 14 and 15).
2.
Check that the nozzle lies central with the combustion head hole.
3.
Check for any visible defects.
12.5 Replace the burner
1.
Connect the flexible oil supply hose to the isolating valve and
tighten sufficiently to form a good seal. Where a double pipe
system is being used fit the bypass plug, as described in Fig. 6,
and connect the oil return flexible hose to the return pipe fitting.
2.
With the sponge O-ring gasket around the burner blast tube
insert the burner into the housing tube. Push the burner firmly
forward to compress the gasket and tighten the two locking
screws using a 5mm Allen key.
Note:
It is important that a good seal is made between the
burner and the boiler to prevent re-circulation of the flue gases
from the combustion chamber to the room.
3.
Re-connect the electrical lead plug into the control box.
12.6 Check the installation
1.
Check that the appliance is correctly wired as described in
Section 10.
2.
Check that all baffles are correctly located and the heat shield
is correctly mounted (70/90 and 90/110 models only) as
shown in Fig. 16.
3.
Check that the baffle retainer is correctly mounted (70/90
and 90/110 models only) as shown in Fig. 16.
6.
Check that the control thermostat and auto reset high limit
thermostat phials are correctly located in the boiler thermostat
pocket positioned in the top front of the boiler.
7.
Check that the manual reset limit thermostat is located in the
steel pocket above the electrical box mounting bracket on the
front face of the boiler.
8.
Check that all of the air-ways to the burner are clear of any
obstruction.
12.7
Fit a pressure gauge and manifold to the burner pump at
the point indicated in Fig. 6 or the pressure gauge port shown in
Fig. 14 on the 70/90.
12.8
Turn on the electricity to the appliance.
12.9 Bleed the burner.
Single Pipe System
Release the fuel bleed port on the manifold and place a suitable
receptacle beneath. Turn on the boiler thermostat and allow the
burner to run through to lockout. Wait two minutes and reset
the burner control box. Repeat the procedure at least three
times or until a steady stream of oil, without air, is exhausted
from the bleed port. Re-lock the bleed port.
Two Pipe System
A two pipe system will automatically vent the air back to the oil
tank. Turn on the boiler thermostat and allow the burner to run
through to lockout. Wait two minutes and reset the burner
control box. Repeat the procedure until the burner fires and
runs in a steady state. This may take several attempts
depending on the oil pipe length and height.
12.10
Adjust the air shutter and pump pressure to the settings
recommended in Tables 2 to 4. After a pre-ignition period of
approximately 15 seconds the burner should ignite. Flame
sensing is carried out by means of a photocell mounted in the
burner body. Should the boiler fail to establish a normal firing
pattern (or should flame failure occur during running), the
absence of a flame is sensed and the control box is monitored to
a safe lockout condition and the boiler is shut down. The
lockout indicator light/reset button in the burner control box
will illuminate indicating that the burner has gone to lockout. In
this instance wait two minutes and press the lockout reset
button to initiate another start sequence. Repeat the procedure
until a flame is established.
Note:
Persistent lockout when running indicates a fault and a
Service Engineer should be consulted.
12.11
Run the boiler for approximately 3 minutes and switch
off checking that there is no after-spurting from the nozzle. This
can be detected by oil saturation on the blast tube. If after-
spurting occurs remove the burner from the boiler, unscrew the
nozzle, and while holding the burner in a vertical position, fill
the nozzle holder with oil and refit the nozzle. Replace the
burner and continue to run the boiler for three minute periods
until after-spurting stops.
Note:
In order that after-spurting is reduced to a minimum
during the commissioning period it is recommended that a
pressure gauge only is fitted on the external pressure gauge
port on the Electro Oil B11 (See Fig. 14). Use of a “T” piece
pressure gauge manifold will increase the oil line volume and
hence increase the degree of after-spurting.
12.12
Run the boiler for a further 15 minute period and then
finally fine tune the air shutter setting to give the CO
2
level
specified in Tables 2 to 4 less 0.5%CO . During this period some
smoke will be emitted due to the burning of the organic binder
in the base insulation board. Smoke readings will therefore be
inaccurate at this point.
Note:
A flue gas sampling point is located on the boiler top
plate.
12.13
Check that the smoke reading is in the range 0-1. If this
cannot be achieved then check that the burner head is set
correctly and the nozzle is in good condition.
12.14
Check that the flue temperature does not exceed the
value specified in Tables 2 to 4. If this is the case then check that
the baffles are correctly located. If the baffles are correctly
located then reduce the pump pressure since nozzle variations
of up to + or – 15% may occur.
12.15
Remove the oil pressure gauge and manifold and check
all oil system joints for any signs of leakage.
12.16
Refit the cabinet front panel.
12.17
Allow the burner to run for a further five minutes and
then recheck the CO
2
level and adjust the air setting if
required. With the cabinet front panel fitted as 12.16, repeat
the previous test procedure and Check that the smoke
number is in the range 0-1. Repeat the fine tuning procedure
if found necessary.
12.18
Refit the cabinet top and front panels in the reverse
order to that described in Section 5.
12.19
When the heating circuit has reached full operating
temperature check the whole system for any leaks.
12. Commissioning the Appliance
Summary of Contents for 70/90
Page 19: ...19 NOTES ...