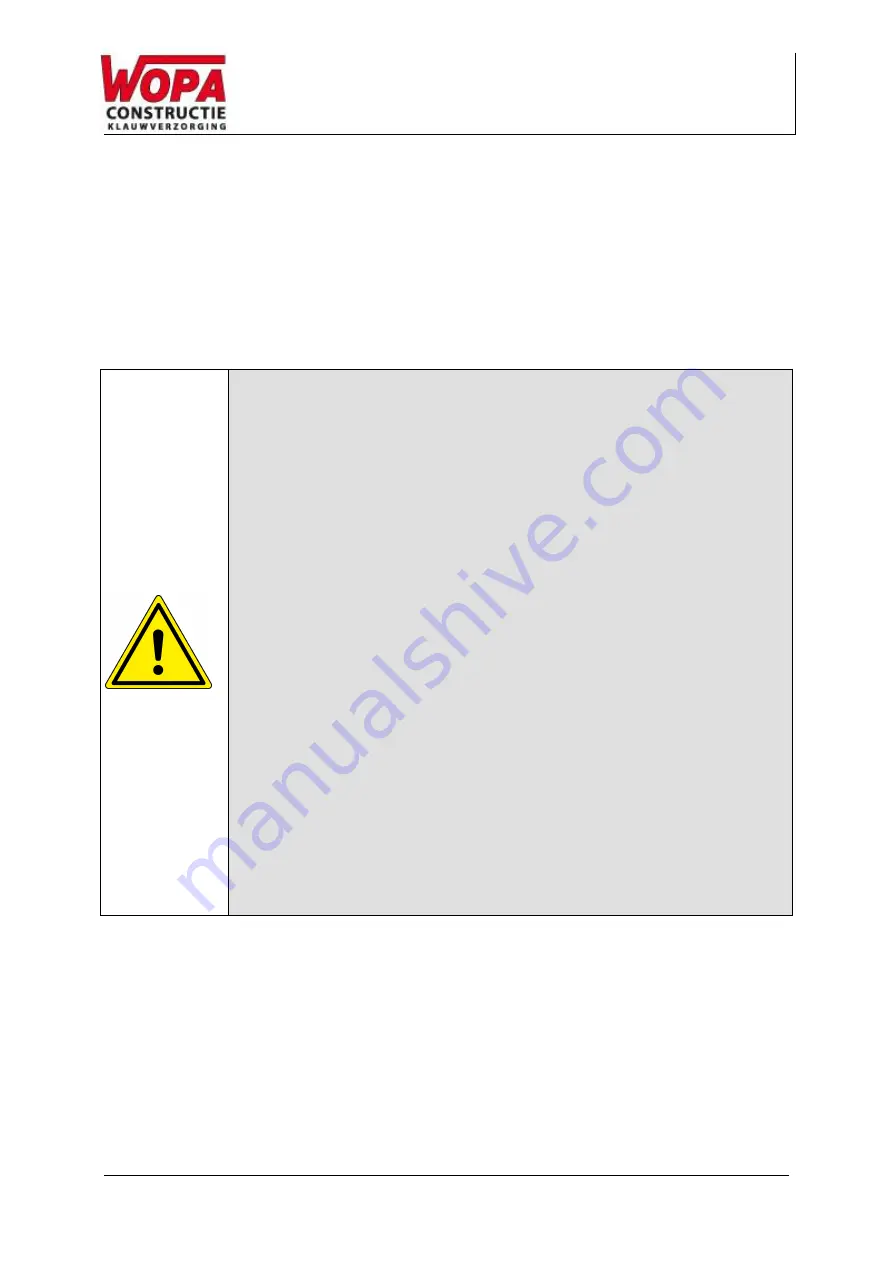
User manual
SA0061 Cattle Crush
Version: 09-07-18
Page 3 of 47
Introduction
Wopa Constructiebedrijf BV are specialists in the development and manufacture of cattle crushes used
by professionals and stockholders for the hoof care and treatment of cows and bulls.
Our cattle crushes are developed and manufactured to the highest standards of safety, ease of use,
animal welfare and hygiene.
This manual contains important information and instructions for the installation, operation and
maintenance of the equipment.
The cattle crush is not suitable for use in explosive environments.
All persons responsible for its operation must as a minimum carefully study and
understand the sections in these operating instructions relating to its use and
safety.
All persons responsible for the assembly, installation, maintenance and repair
of the equipment must read and understand these operating instructions in full.
The user is responsible for the interpretation and use of this manual in all
circumstances. Please contact the owner of the machine or your manager with
any questions or uncertainties.
This manual must be kept close to the installation and accessible to users.
All important maintenance activities, modifications to the installation and any
notes must be retained in a logbook, see Appendix 8.1.
Modifications to the installation/machine are not permitted without the prior
written approval of the supplier.
Contact the supplier for special maintenance activities not included in this
manual.
The safety requirements set out in Section 3 must be complied with at all times.
The proper function and safety of the system can only be guaranteed where
the recommended maintenance has been carried out correctly and in good
time.
Summary of Contents for SA0061
Page 1: ...User manual SA0061 Cattle Crush Version 09 07 18 User manual SA0061 Cattle Crush ...
Page 27: ...User manual SA0061 Cattle Crush Version 09 07 18 Page 27 of 47 5 4 Hydraulic control levers ...
Page 36: ...User manual SA0061 Cattle Crush Version 09 07 18 Page 36 of 47 6 2 VIEW FROM BELOW 1 ...