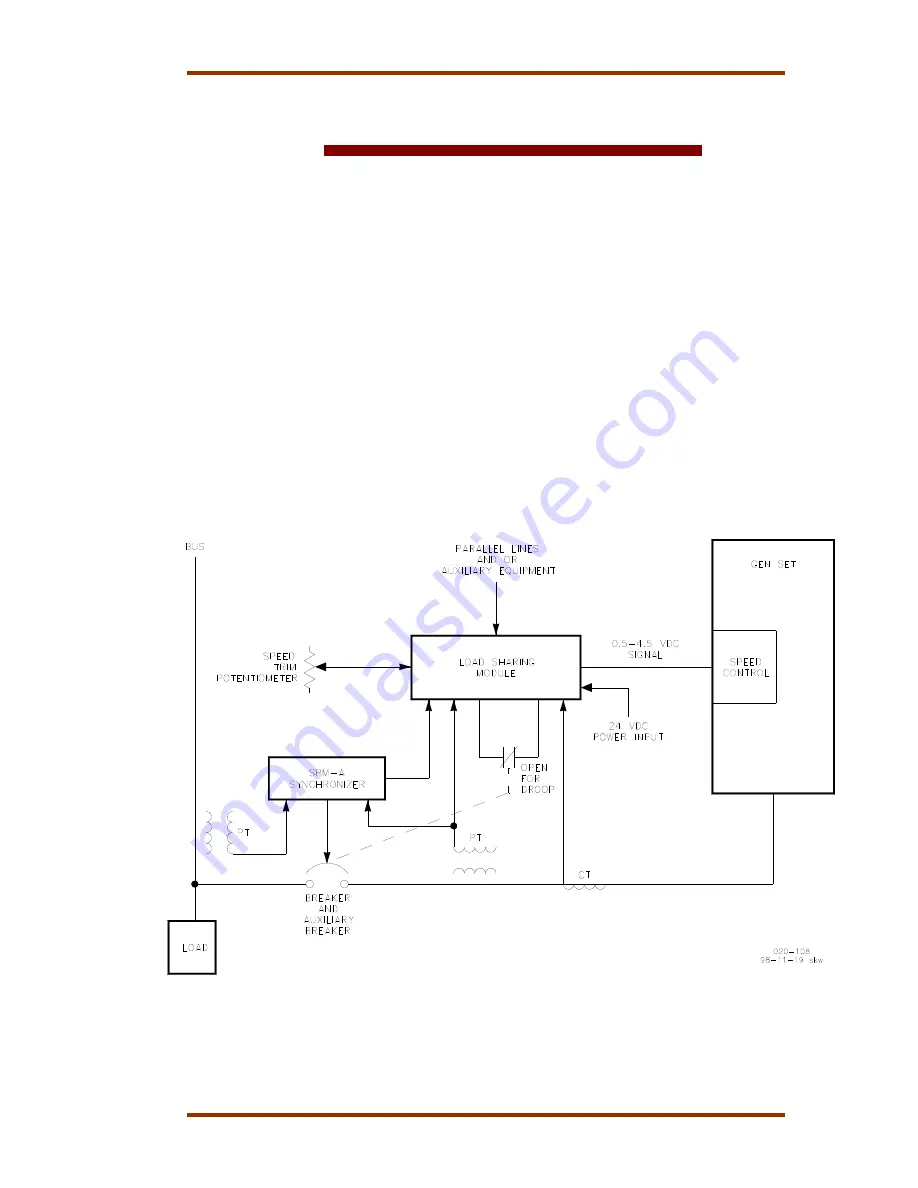
Manual 02035
Load Sharing Module
Woodward
1
Chapter 1.
General Information
Introduction
The Woodward Load Sharing Module is made for use with engines equipped with
speed controls that accept a 0–5 Vdc speed setting. The Load Sharing Module
allows use of Woodward power generation accessories and allows load sharing
between engines equipped with speed controls that are not manufactured by
Woodward and engines controlled with Woodward electronic controls, or controls
using other Woodward load sharing modules.
Description
The Load Sharing Module provides isochronous and droop load-sharing
capability for engines in generator set applications. Additional equipment in the
control system can include the Woodward SPM-A Synchronizer, Import/Export
Control, Automatic Generator Loading Control, and Automatic Power Transfer
and Loading Control.
Figure 1-1 shows a typical system using a Load Sharing Module.
Figure 1-1. Typical System Using a Load Sharing Module
Summary of Contents for 9907-252
Page 6: ...Load Sharing Module Manual 02035 2 Woodward Figure 1 2 Outline Drawing of Load Sharing Module...
Page 7: ...Manual 02035 Load Sharing Module Woodward 3 Figure 1 3 Block Diagram of Load Sharing Module...
Page 8: ...Load Sharing Module Manual 02035 4 Woodward...
Page 34: ...Load Sharing Module Manual 02035 30 Woodward...
Page 35: ......