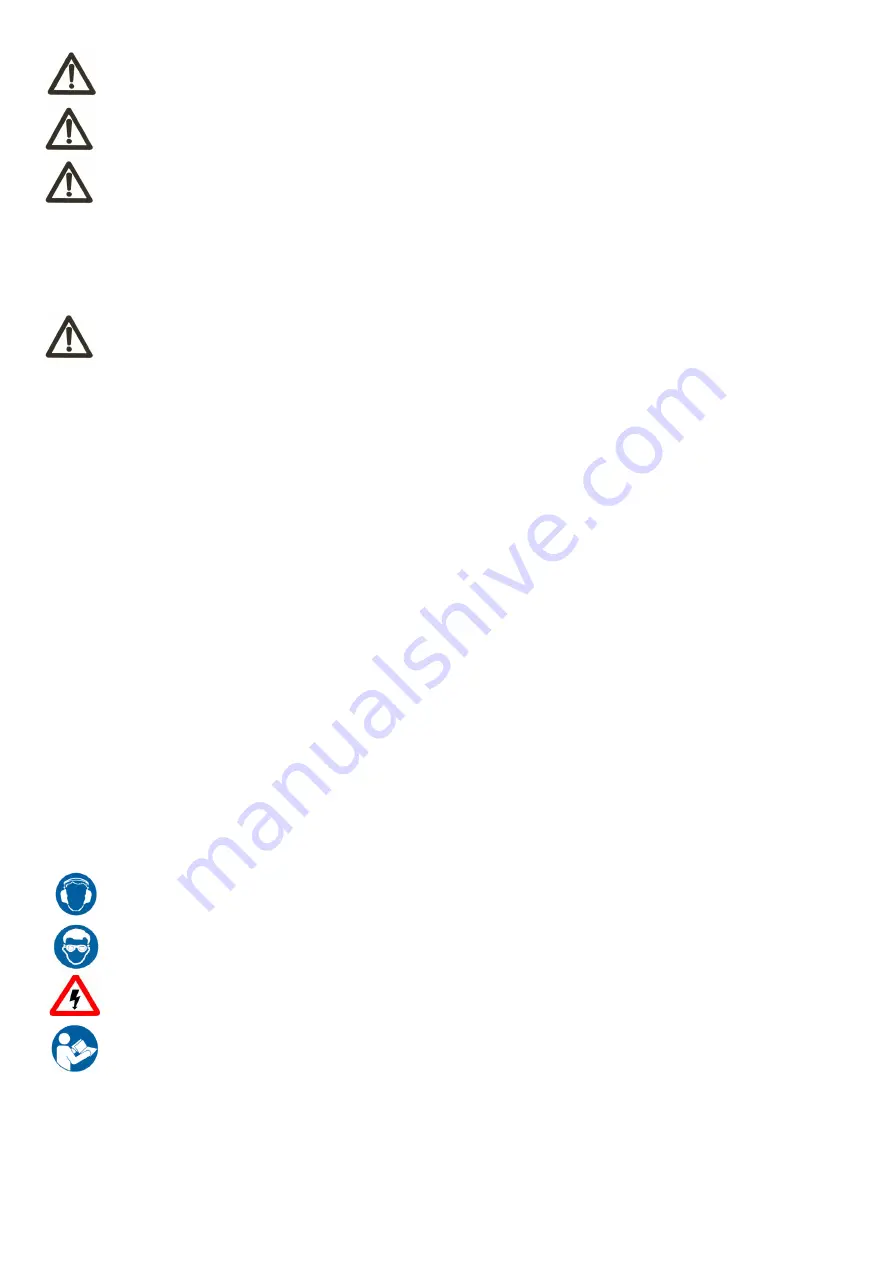
-5-
2.2 RESIDUAL RISKS
- contact with tool
- contact with moving parts (belts, pulleys, etc..)
- recoil of the piece or part of it
- accidents due to wood splinters or fragments
- tool insert ejection
- electrocution from contact with live parts
- danger due to incorrect tool installation
- inverse tool rotation due to incorrect electrical connection
- danger due to dust inhalation in case of working without vacuum cleaner.
2.3 SAFETY AND INFORMATION SIGNALS
This signals may be applied on the machine; in some cases they indicate possible danger conditions, in others they
serve as indication.
Always take the utmost care.
SAFETY SIGNALS:
Wear hearing protection systems.
Risk of eye injury. Wear eye protection.
Danger of electric shock. Do not access the area when the machine is powered.
Carefully read and understand the manual before using the machine.
INFORMATION SIGNALS:
Indicate the technical characteristics, direction of rotation and inclination, block and release, etc.
Carefully following the directions to simply the use and adjustment of the machine.
The signals are graphically described and do not require further explanation.
WARNING
Accident caused by unqualified electrical element which connect machine and unconventional
installation, manufacturer assumes no responsibility.
WARNING
Accident cause by change machine function or change spare part arbitrarily, manufacturer
assumes no responsibility.
Despite observance of all the safety regulations, and use according to the rules described in this
manual, residual risks may still be present, among which the most recurring are:
WARNING
Accident caused by operation under missing part or damage condition,manufacturer assumes no
responsibility
WARNING