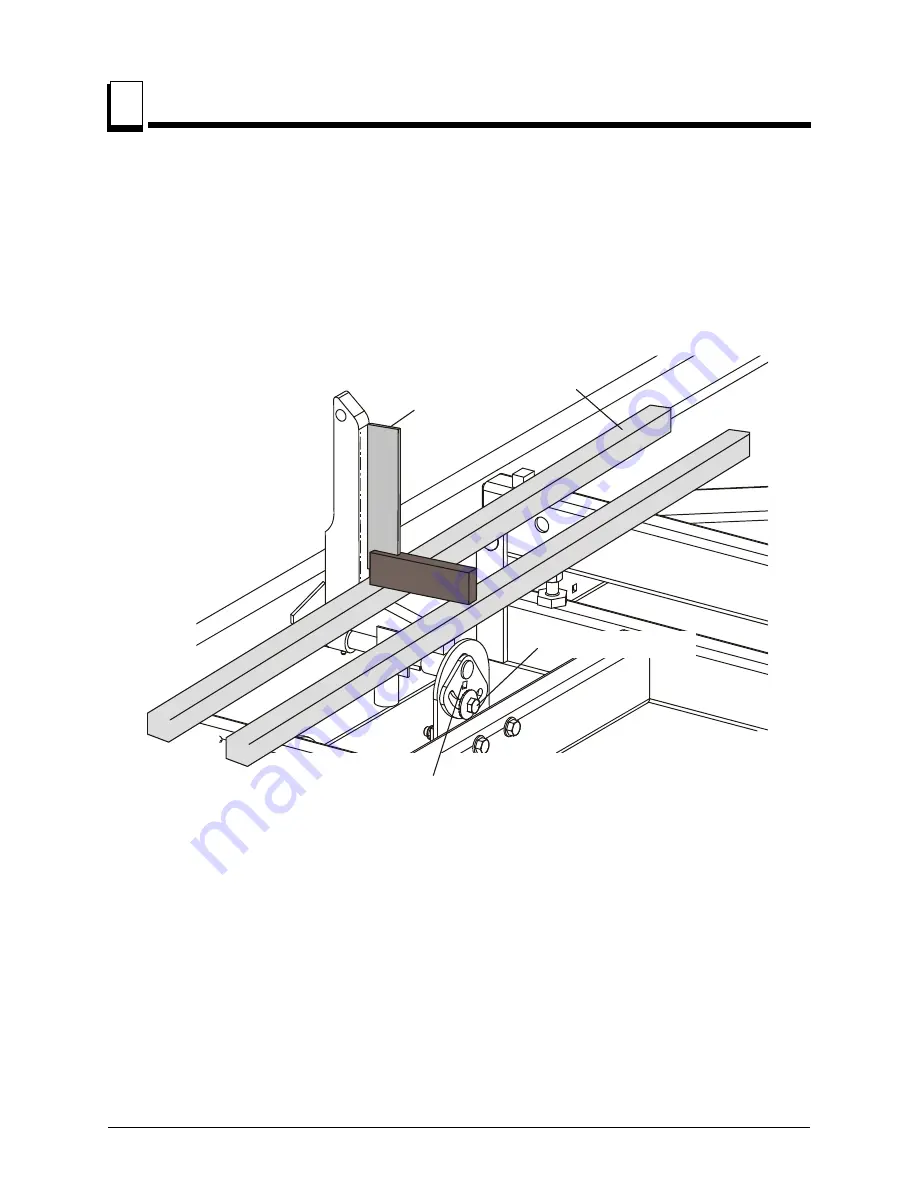
Sawmill Alignment
Hydraulic Side Support Alignment
7
7-40
HD-R10doc072619
Sawmill Alignment
4.
Pull back at the top of the support to eliminate slack as if a log were being clamped
against it.
5.
Place a square against the face of the side support. The side support should be square or
slightly tilted forward 1/32" (0.8 mm). Adjust the vertical tilt of the side support if neces-
sary.
See Figure 7-44.
Loosen the side support mounting bolt. Use a 3/8" ratchet to rotate the
pin until the side support is square to the bed.
6.
Repeat the vertical check for the remaining side supports and adjust as necessary.
Hydraulic Side Support Alignment
Place the square against the face of the side support. The side support should be square
or slightly tilted forward 1/32" (0.8 mm). Adjust the vertical tilt of the side support if neces-
sary.
FIG. 7-44
SM0272-1
Place square
against side
support
Loosen mounting bolt
Alignment
Tubes (2)
Use 3/8” ratchet to adjust
side support mounting pin