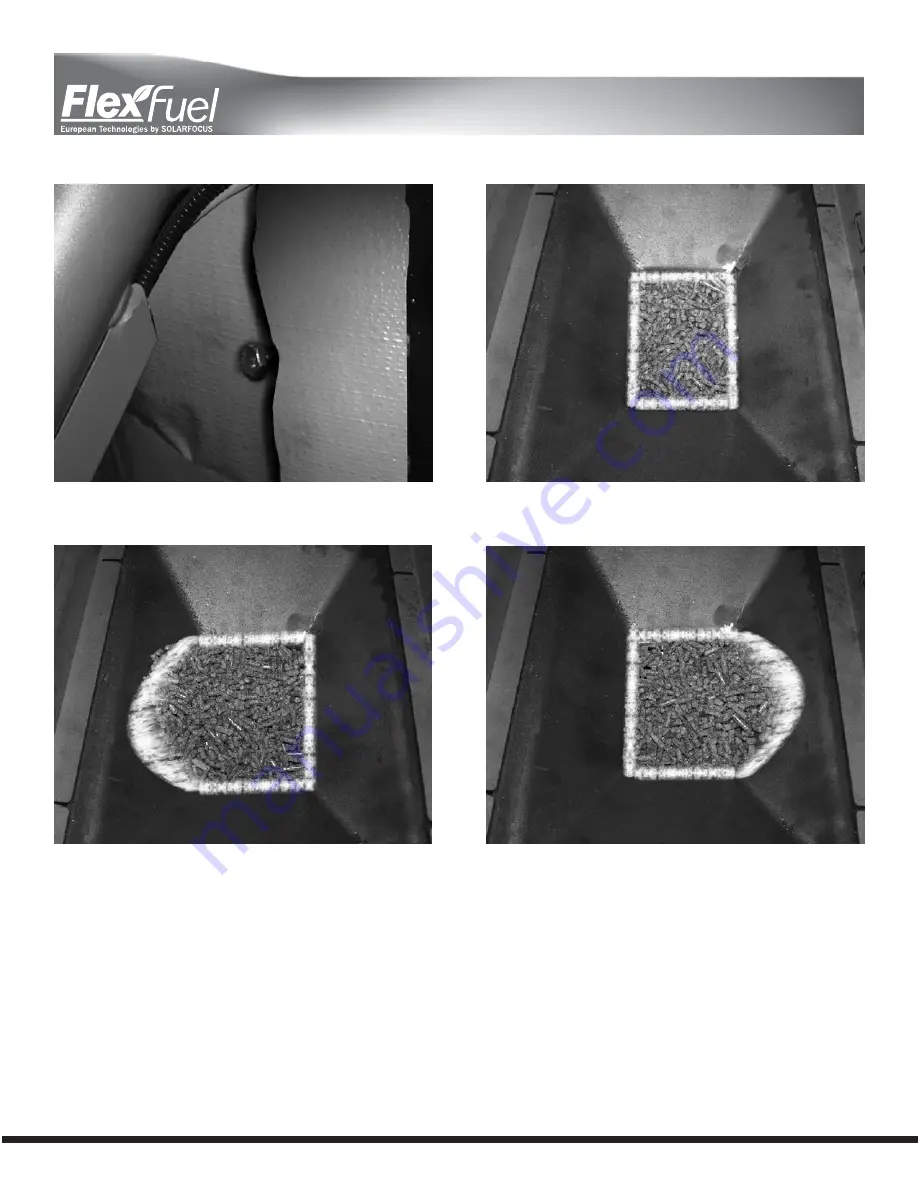
54
Flex Fuel Owner’s Manual
March 2011
13: Pellets Auto Control
Adjustment Bolt (Fig. 1)
Correct Burn: no further
adjustments needed (Fig. 2)
Incorrect Burn: bolt is
too far in. (Fig. 4)
Incorrect Burn: bolt is
too far out. (Fig. 3)
Allow the furnace to burn for another 45 minutes and check the pile again. If it is still not burning in the
center adjust again. Repeat this process until the pile is evenly centered on the insert. Once this is
achieved lock the counter nut and replace the panel.
Check the slide adjustment once a month to ensure a proper burn.
Note: Adjusting the slide is a time consuming process.
Allow yourself at least 2.5 hours to correctly adjust the slide.