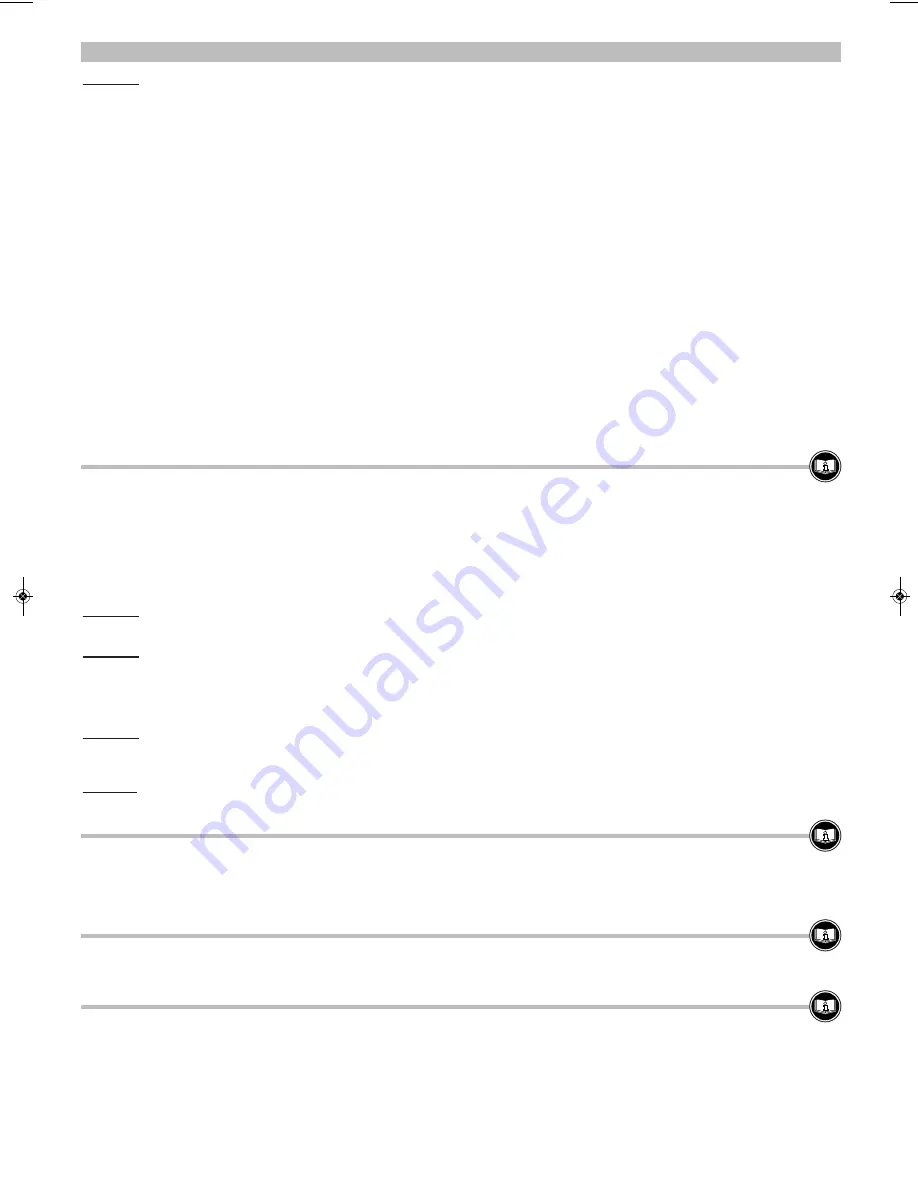
WARNING: Make always sure that your hands are kept at a sufficient distance from the rotating saw blade (danger of injury).
With the angle guides installed in this way, work pieces with a height ranging between 15 mm and 60 mm can be sawn. If the height of the work
piece is less than 15 mm, the guidance of the angle guide will have to be modified accordingly (Fig. 16.4 - 16.7). The angle guide makes it possible
to saw work pieces at angles ranging between 0° and 65°. In order to do, loosen the knurled screw, set the required angle and re-tighten
the knurled screw firmly (Fig. 16.8). You can now use the saw as shown in Figures 16.1 - 16.3.
Sawing with the parallel guide
Put the parallel guide with the eccentric levers left open into the table’s guidance. Press down both eccentric levers and make sure that the parallel
guide is aligned parallel to the circular saw blade (Fig. 17.1). The guidance for the angle guide must now be installed on the parallel guide, in order
to prevent the work piece from striking back during the sawing. Install both knurled screws with their square nuts loosely on the parallel guide
(Fig. 17.2) and slide the guidance into both square nuts at the parallel guide as shown in the picture. The end of the guidance must not be inserted
farther than the end of the saw blade (Fig. 17.3). Tighten both knurled screws and loosen both eccentric levers, in order to set the desired cutting
width. Then press down both eccentric levers. Now switch on the hand-held circular saw at its safety switch and push the work piece in the direction
indicated by the arrow towards the saw blade as shown in Fig. 17.4, until the work piece is completely cut through. Then switch off the hand-held
circular saw at the safety switch. Use the push stick (which is included in the scope of delivery) for narrower work pieces (Fig. 17.5). If necessary,
the parallel guide can also be installed on the right-hand side of the circular saw blade. In order to do so, shift the guidance by one row of holes
(Fig. 17.6). All other installation steps can be taken from Figures 17.1 - 17.3.
Vertical mitre cuts
The hand-held circular saw must be re-aligned for vertical mitre cuts. In order to do so, re-move first of all the gap insert (Fig. 18.1).
Then lift the machine plate at the recessed grip (Fig. 18.2) and remove it (Fig. 18.3). Retract the circular saw‘s protective pendulum hood
and put the gap insert back until it hits the stop (Fig. 18.4). Place the machine plate thus installed onto the table as shown (Fig. 18.5).
Loosen the four clamping claws and the four side stops. Set the desired mitre angle at the hand-held circular saw and shift the base plate
in the direction indicated by the arrow par-allel along the two remaining side stops (Fig. 18.6). Make sure that the saw blade can freely run
in the gap insert. Then fix the four side stops and the four clamping claws (Fig. 18.7). After having placed the machine plate together
with the hand-held circular saw onto the table’s four retaining bolts, let the machine plate slide into its holders from above and let it click into place.
The table is now ready for vertical mitre cuts (Fig. 18.8).
SAWING WITH THE GUIDE BAR
When the hand-held circular saw was initially installed (Fig. 14.1 - 14.8), it was precisely geared to working with the guide bar. Now place the
machine plate with the hand-held circu-lar saw thus installed onto the table and exchange the gap insert for stationary sawing against the gap insert
for cutting with the guide bar (Fig. 19.1). Put the work piece onto the worktop. Always use the angle guide for the guide bar, if possible (see section
on angle cuts). Then install the guide bar with its two holders and the two clamps (Fig. 19.2). Always tighten the two clamps so firmly that the work
piece cannot get out of place during the sawing. Place the machine plate with the hand-held circular saw installed on it onto the guidance of the
guide bar. Now set the cutting depth of the hand-held circular saw in such a way that the saw blade does not extend more than 4 mm underneath
the work piece.
WARNING: When cutting narrow work pieces, support the guide bar with work pieces of the same height over the entire table width,
so that the guide bar cannot tumble down with the machine plate.
WARNING: The appliance inlet of the hand-held circular saw must be plugged into a mains socket outlet, since the safety switch and the switch clamp
must not be used when sawing with the guide bar.
Switch on the hand-held circular saw and move it always parallel along the guide bar (Fig. 19.3). Once the cut has been completed,
switch off the hand-held circular saw.
Angle cuts: Put the plastic holder of the angle guide into a borehole on the worktop. Always use the borehole closest to the cutting edge
of the guide bar. Shift the loosely assembled guide rails into the groove on the worktop and right up to the angle guide. Now clamp the groove
of the guide rail into the profile of the angle guide. Align the work piece together with the angle guide to the guide bar and tighten the knurled
screw of the guide rail firmly (Fig. 19.4).
Serial cuts: Install the additional guide slide for serial cuts. Insert the guide slide into the groove of the angle guide and turn the metal stop up to
the worktop. Then place the work piece in the desired length against the angle guide and push the guide slide to the end of the work piece.
You can now tighten the knurled screw firmly (Fig. 19.5).
SAWING WITH THE JIGSAW
Fit the gap insert for jigsaws into the machine plate (Fig. 20.1). Align the jigsaw on the machine plate in such a way that the saw blade runs in the
centre of the saw opening. Now install the jigsaw as shown in Fig. 20.2 & 20.3. Insert the jigsaw thus installed together with the machine plate into
the table and let its four holders click into the retaining bolts. Attach the switch clamp to the jigsaw switch and con-nect the appliance inlet with the
safety switch. The table is now ready for being used with the jigsaw (Fig. 20.4).
USE AS WORKBENCH
The Master cut 2000 is equipped with 4 plastic clamping claws and 2 quick clamps made of aluminium. They can be used to clamp work pieces
flexibly and safely or to fasten them tightly (Fig. 21).
SETTING THE MACHINE PLATE
The machine plate has been set in the worktop in the factory at such a height that a workpiece can be safely moved over the entire worktop and
machine plate. The height of the machine plate can be adjusted, if the need arises. In order to so, release the five lock nuts, align the machine plate
flush with the height of the work top with the help of the five adjusting bolts and re-tighten the lock nuts (Fig. 22). Make sure before staring any new
job that the five lock nuts are always firmly tightened.
t
31
BDAL 6900_116386900_NEU 11.01.13 09:49 Seite 31
Summary of Contents for MASTER cut 2000
Page 2: ...2 1 1 1 1 4 1 6 1 5 1 7 1 8 1 10 1 11 1 12 1 13 1 14 1 2 1 3 1 9...
Page 4: ...4 3 3 1 3 3 3 2 3 4 1 1 A B B B B B C C A...
Page 5: ...4 1 9 2 22 2 17 2 23 2 21 5 5 2 5 3 5 1 1 11 1 10 2 27 2 16 2 20 2 23 2 26 2 19 5...
Page 7: ...7 8 8 2 8 3 8 1 9 2 10 2 5 2 9 2 3 2 33 2 32 1 12 10 10 3 10 1 2 48 2 x 10 2 1 13 2 49 2 x...
Page 8: ...8 11 11 2 11 6 11 1 11 5 11 4 11 3 1 3 1 2 unlock...
Page 9: ...12 13 9 14 14 1 2 2 2 12 2 5 2 6 2 7 D D D D D D 14 2 D 6 x...
Page 10: ...14 10 14 3 2 11 2 4 2 8 E 4 x E E E E 14 4 14 5 14 6 14 7 max max 20 mm...
Page 12: ...15 15 4 12 15 3 16 16 3 16 2 16 1 16 4 16 5 16 6 16 7 min 15 mm max 15 mm 2 33 EIN ON AUS OFF...
Page 13: ...16 13 16 8 0 max 65 17 17 2 17 4 17 6 17 3 17 5 2 25 2 24 2 x 2 x 17 1 1 14 max...
Page 14: ...14 18 18 2 18 4 18 5 18 8 18 3 18 6 18 7 18 1 4 x 4 x 1 2...
Page 15: ...15 19 19 3 19 1 19 2 H 1 4 H H 19 4 max 4 mm 0 max 70 45...
Page 16: ...16 20 20 2 20 1 1 5 J 4 x 2 1 2 13 19 19 5 1 2 20 4 20 3 J J...
Page 17: ...17 21 2 50 2 47 1 22 2 3...
Page 94: ...94 DIN EN 60745 1 1995 CE ON 200 mm 70 mm 13 v...
Page 95: ...95 wolfcraft 6119973 6901000 6901000 6901000 1800 W 230 V 27 mm 6119973 v...
Page 124: ...124 DIN EN 60745 1 1995 200 mm 70 mm e...
Page 125: ...125 13 wolfcraft Nr 6119973 A 6901000 6901000 6901000 1800 W 230 V 27 mm 6119973 e...
Page 136: ...136 r DIN EN 60745 1 1995 CE 200 70 13...
Page 137: ...137 r wolfcraft 6119973 6901000 6901000 6901000 1800 230 27 6119973...
Page 141: ...141...