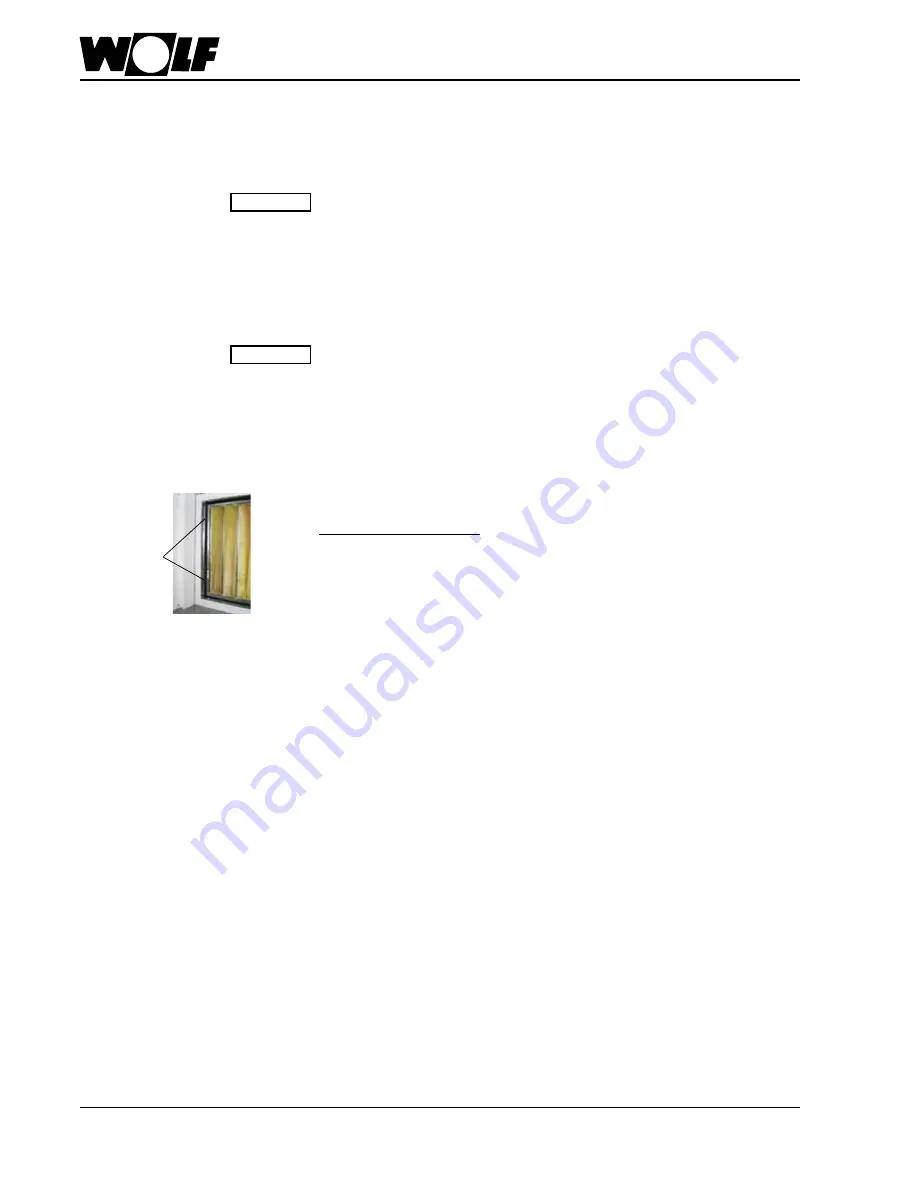
20
3040530_201503
Maintenance / Frost protection
Heat exchanger
Warm/hot water heater, cold water cooler:
- Only site the KG air handling units in a room that is free from the risk of frost.
- Operation with commercially available antifreeze and frost stat.
- With the heating system switched OFF, drain all parts filled with water and
blow out remaining water using compressed air.
Steam coil:
- With the heating system switched OFF, drain all parts filled with water and
blow out remaining water using compressed air.
Electric heater:
- No frost protection measures required.
Scrubber
Insulate the water supply line on site; use a ribbon heater if required.
Drain pan and pipework; blow compressed air through pipework.
Drain pump (see separately supplied instructions from pump manufacturer).
Siphon
Protect siphon on site against freezing.
Frost protection measures
Clean scrubbers and mist eliminators at regular intervals. The cleaning cycles
depend on the operating mode, air condition and water quality.
For maintenance, drain the pan and rinse with clean water or a high pressure
cleaner.
Spray the pipework and nozzle holder only with reduced water pressure.
If the water pressure is too high, there is a risk of destroying components.
Commercially available descaling agents can be used.
Foaming cleaning agents are not suitable.
The scrubber pump is maintenance-free.
However, when cleaning the scrubber, we recommend flushing the pump and
pipework with clean water.
If the scrubber is idle for a prolonged period, run the pump once a week for
approximately 5 minutes to prevent the bearings seizing up (never run dry).
Please note
Please note
Scrubber
Filters
Fixing clips
To clean or replace the filter cartridges, open the inspection door and remove
the cartridges from the side of the unit casing.
The grade G4 synthetic fibre filter mats used for the filter cartridges are
renewable. You can beat them, blow air through them, vacuum them or
wash them in lukewarm water with commercially available mild detergent.
Never wring out the mats.
Bag filters are not renewable; they have to be replaced due to contamination
when they exceed the permissible pressure drop.
To replace filter cartridges that are held in the unit frame with clips, open the
inspection door, release the clips and remove the cartridges from the side of
the unit casing towards the dusty side.
Replace filter bags once the recommended final pressure drop has been reached.
Summary of Contents for KG Standard
Page 22: ...22 3040530_201503 Notes ...
Page 23: ...3040530_201503 23 Notes ...