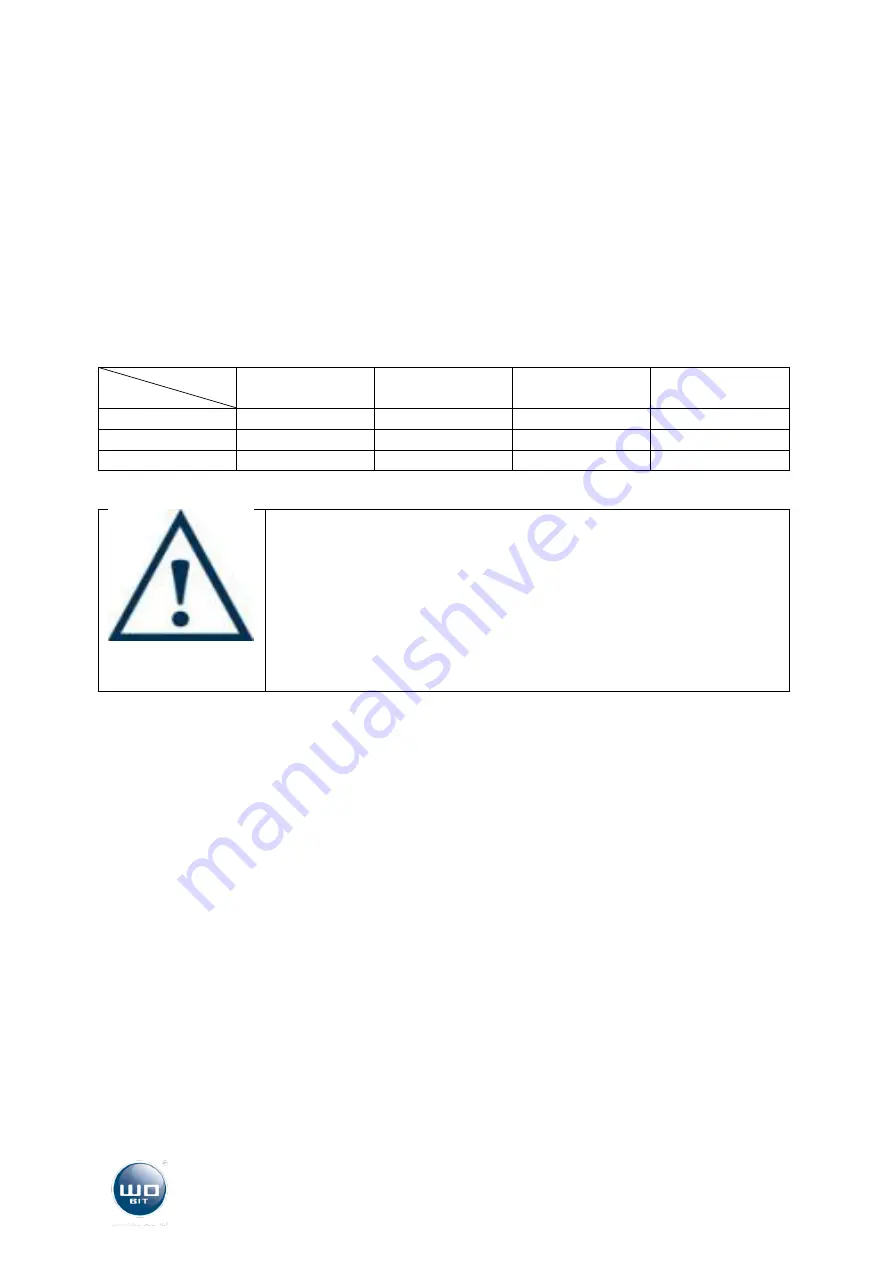
www.wobit.com.pl
Manual -SIC184 – 27.10.2014 – v.1.1
page 11
For driver power supply it is recommended to use a non-stabilized power supply with output voltage
in range +12..+36V. The power supply must receive return energy of the motor, which is provided by
output capacitors with capacity bigger than 4700µF.
A minimal current efficiency of power supply should be match according to formula below:
Izas= 12/Uzas*Ister
Where:
Izas
-a minimal current efficiency of power supply,
Uzas
– voltage supply,
Ister
- set driver
current.
Exemplary values of minimal current efficiency used power supply :
Motor current [A]
Power supply[V]
1
2
3
4
12
1A
2A
3A
4A
24
0,5A
1A
2A
3A
36
0,4A
0,8A
1,5A
2,5A
Warning!
Opposite polarity or exceeding of max voltage supply can cause damage of
the driver.
To small output capacitors or none capacitors can damage the driver or
cause incorrect operation, while operation of the driver with high voltage
and a big motor, which operates dynamic (sudden decreasing velocity of
the motor).
It is recommended to use electrolytic capacitors 1000µF at max driver
currents and max rotational velocity (>2 rps).
2.5 Stepper motor
Motor should be connect to the driver by 4-pin cable. To reduce noise it is recommended to use
twisted cable (A with /A, B with /B), preferably shielded. In case of unipolar motors (with 6 or 8
derivation cables) you should connect them according to examples below.