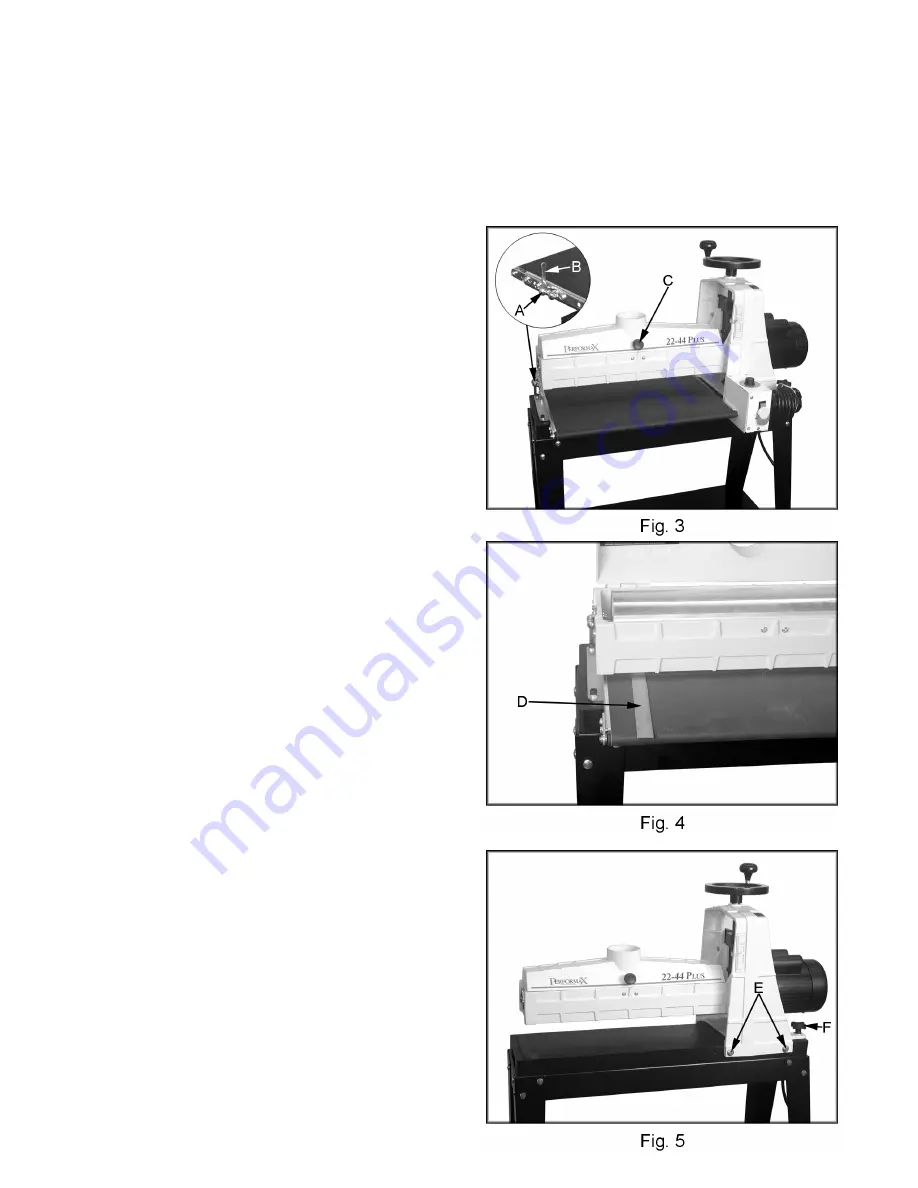
10
Conveyor Belt Tracking
Belt tracking adjustment may be necessary
during the break-in period to compensate for belt
stretching.
Abrasive belt tension must be properly adjusted
before adjusting the tracking. Adjust the belt
tracking while the conveyor belt is running at its
fastest speed.
Tighten the hex nut (Fig. 3, Item A) on the side
the belt is drifting towards, and loosen the hex
nut on the opposite side. Use the attached
wrenches (Fig. 3, Item B) to adjust the hex nuts.
Note:
Adjustment should be made in 1/4 turns of
the hex nut. Allow time for the belt to react to the
adjustment. Do not over adjust.
Dust Cover
To open the dust cover, push in on the knob
(Fig. 3, Item C) and lift.
Checking Drum Alignment
The sanding drum comes preset from the
factory. If a problem with the drum alignment
occurs follow the instructions listed below.
1. Push in and lift the knob (Fig. 3, Item C) to
open the cover and remove the abrasive
strip. If you are unsure how to do this, see
the “Wrapping Abrasive Strips” section in
this manual.
2. Using a metal straight edge, or ruler, as a
thickness gauge (Fig. 4, Item D), insert the
gauge between the drum and the conveyor
bed on the outer end of the drum.
3. Open the dust cover and lower the sanding
drum while slowly rotating the drum by hand
until the drum lightly contacts the thickness
gauge.
4. Remove the thickness gauge and place it
under the drum at the opposite end. If the
drum does not contact the thickness gauge
to the same degree as the other end of the
drum, alignment is necessary.
Aligning the Drum
1. Loosen the four hex cap bolts (Fig. 5, Item
E) (two in front and two in back).
2. Lay the thickness gauge under the drum
lengthwise.
3. Adjust the knob, (Fig. 5, Item F) until the
drum contacts the gauge equally along its
entire surface. Turn the adjusting knob
clockwise to raise the outboard end of the
drum, and counterclockwise to lower the
outboard end of the drum.
4. When the drum is parallel to the conveyor,
tighten the four hex cap bolts.
Summary of Contents for PERFORMAX 22-44 Plus
Page 19: ...19 Drum Head Assembly...
Page 22: ...22 Conveyor and Motor Assembly...
Page 24: ...24 Wiring Diagram...