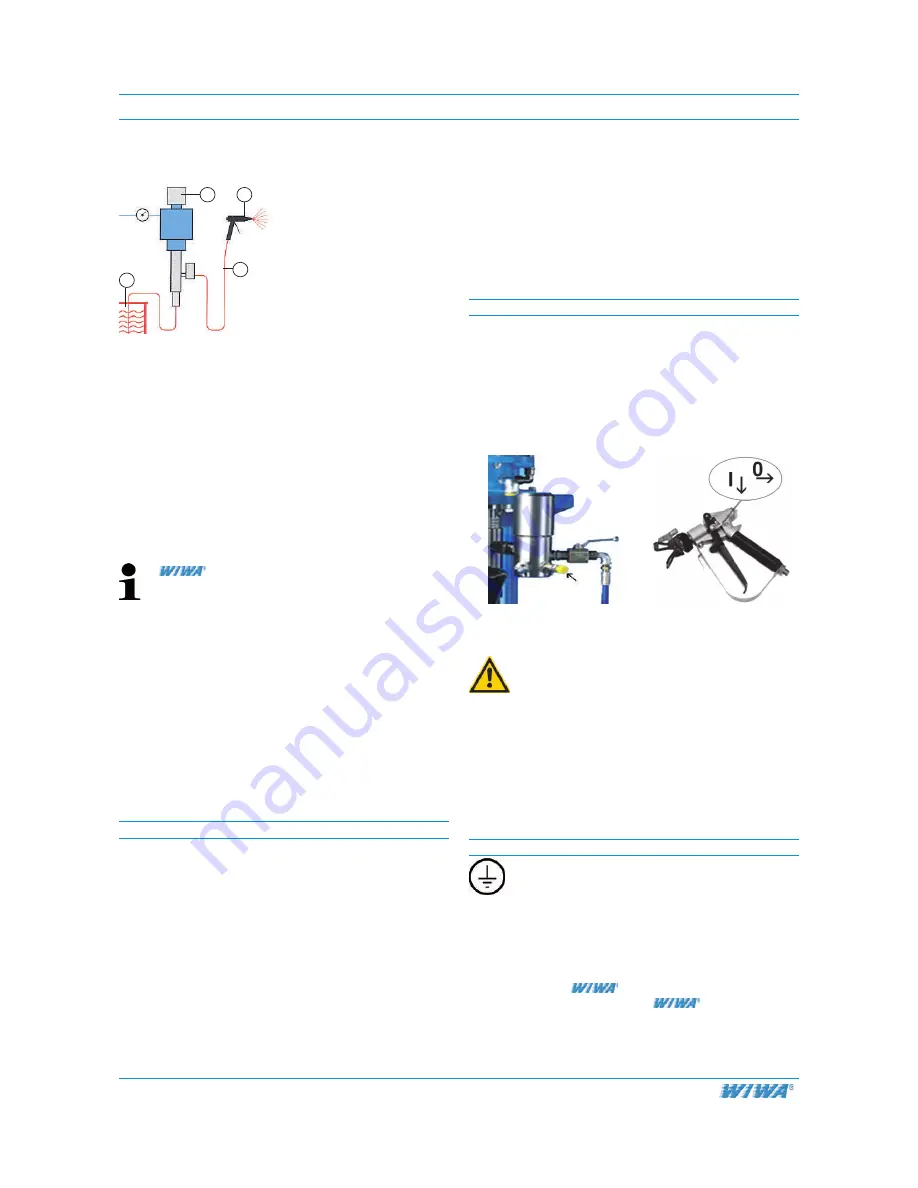
12
Translation of the original operation manual Airless
Phoenix_BAoDB_en_1210
•
jw
4
Installation and Assembly
1 Airless unit
2 Airless spray gun
3 Paint container
4 Spray hose
Picure 4.1
1
2
3
4
Job
The unit is to be installed at the job site and prepared for
operation.
Prerequisite
➤
The material to be worked with is prepared.
➤
All materials to be sprayed should be marked with
information on viscosity, processing temperatures,
mixing proportions etc. If this is not the case, please
acquire this data from the relevant manufacturer.
➤
The material to be sprayed must be slowly but tho-
roughly stirred before beginning to work.
offers a broad selection of accesso-
ries for the optimised preparation of spraying
materials, i.e.:
➤
agitators in various sizes
➤
material pre-heating containers in various
sizes
➤
fluid hester
If working with plural component materials,
the pot life must be observed.
➤
To insure that the necessary volume of air is supplied,
the compressor capacity must comply with the air con-
sumption requirements of the pump.
The diameter of the air supply hoses must correspond
to the connection on the pump.
1. Set up the pump
➤
The pump must be set up securely on a level and solid
surface
➤
Pay attention to the information covering the required
floor space found in machin card.
➤
Operating elements must be easily accessible
➤
Safety features must be
easily accessible
Wall-mounted versions:
➤
To fix the wall-mount, use M 12 screws - class 8.8
➤
Be sure to use anchoring devices in accordance with
the nature of the wall being used
➤
Ensure that at least 10 cm (4 in.) free space is left
between the suction elbow and the floor after mounting
(refer to the picture in Chapter 3)
2. Mount accessories
For transport purposes the following components were
dismounted and packed in a separate carton:
1.
Spray hose (Picture 4.2)
2.
Airless spray gun (Picture 4.3)
3.
Air regulator or maintenance unit (depending upon
version)
➤
Attach these items according to Picture 4.2 + 4.3.
Note:
The air maintenance unit is connected to the air
inlet of the air motor.
Picture 4.2 Spray hose con
-
nection on the high-pressure
filter
Picture 4.3 Spray hose con
-
nection to the spray gun
m
Warning!
Material leaks at connections can lead to se-
rious injury of property damage.
Check all turnable parts, nuts, screws and
hose connections and tighten them securely.
➤
Check the permissible maximum air pressure for the
spray hose, spray gun and accessories. It must be
greater than or equal to the maximum operational
pressure shown on the pump's nameplate or on the
machine card.
3 Ground the unit
Warning!
Due to the high flow speed created by Airless
equipment, static charging can occur. A static
charge can lead to fires or explosion
A static charge can lead to fires or explosion.
➤
The pump and object to be coated must be
grounded properly
➤
Only use conductive hoses
Note:
spray hoses are conductive
and compatible with
pumps