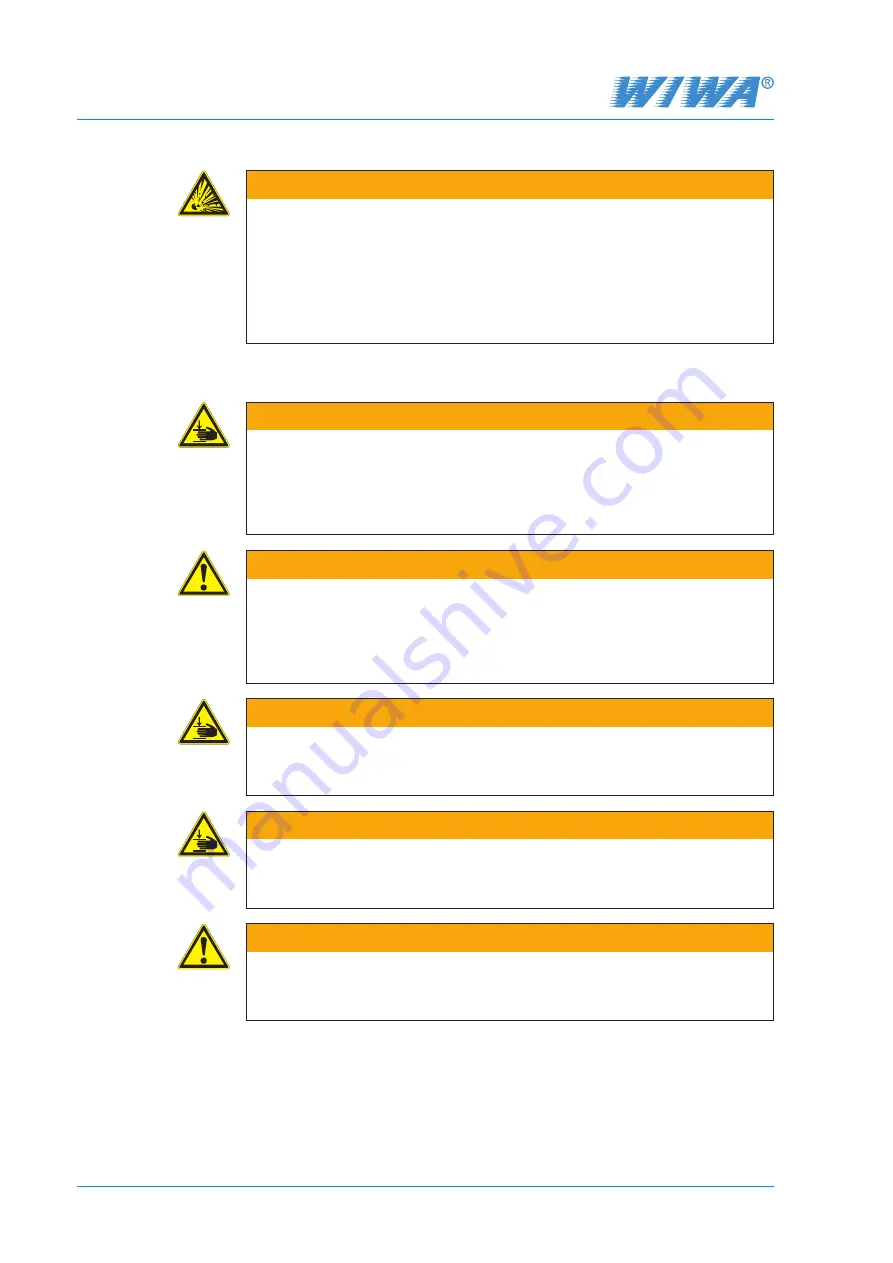
10
Translation of the original operation manual
HERKULES PFP
HERKULES PFP_BAoDB_en_1402_B · rs
Safety
WARNING
Heating up cleaning agents can cause an explosion. This may result in seri-
ous injury to persons and damage to property.
➤
Pay attention to the flashpoint and the ignition temperature of the clean
-
ing agent.
➤
Switch off the material flow heater if you need to perform the following
work: Cleaning, pressure testing, decommissioning, maintenance and
repair.
2.2.5 Risks due to the rams
WARNING
While the rams are lifting, the moving components can crush your fingers,
hands or other parts of the body.
➤
Do not reach between the follow plate and the material drum, the tra-
verse and cylinder cover of the pneumatic cylinder or the clamping piece
and the cylinder cover of the pneumatic cylinder.
WARNING
While the rams are lifting, loose clothing can get between the follow plate or
the follow cover and the material drum or catch on other moving components
or be pulled upwards.
➤
Wear tight-fitting working clothes that are not very tear-resistant, that
have tight-fitting sleeves and no protruding parts.
WARNING
While the rams are lifting, the moving components can cause crushing or
impact injuries.
➤
While the rams are lifting, nobody must be in the lifting area.
WARNING
Accidental starting of the rams can result in crushing and impact injuries.
➤
Each time work is interrupted, set the ram control levers to the “Stop”
position.
WARNING
Objects placed on the rams may fall down during a stroke movement and
cause injuries.
➤
Never place any objects on the rams!