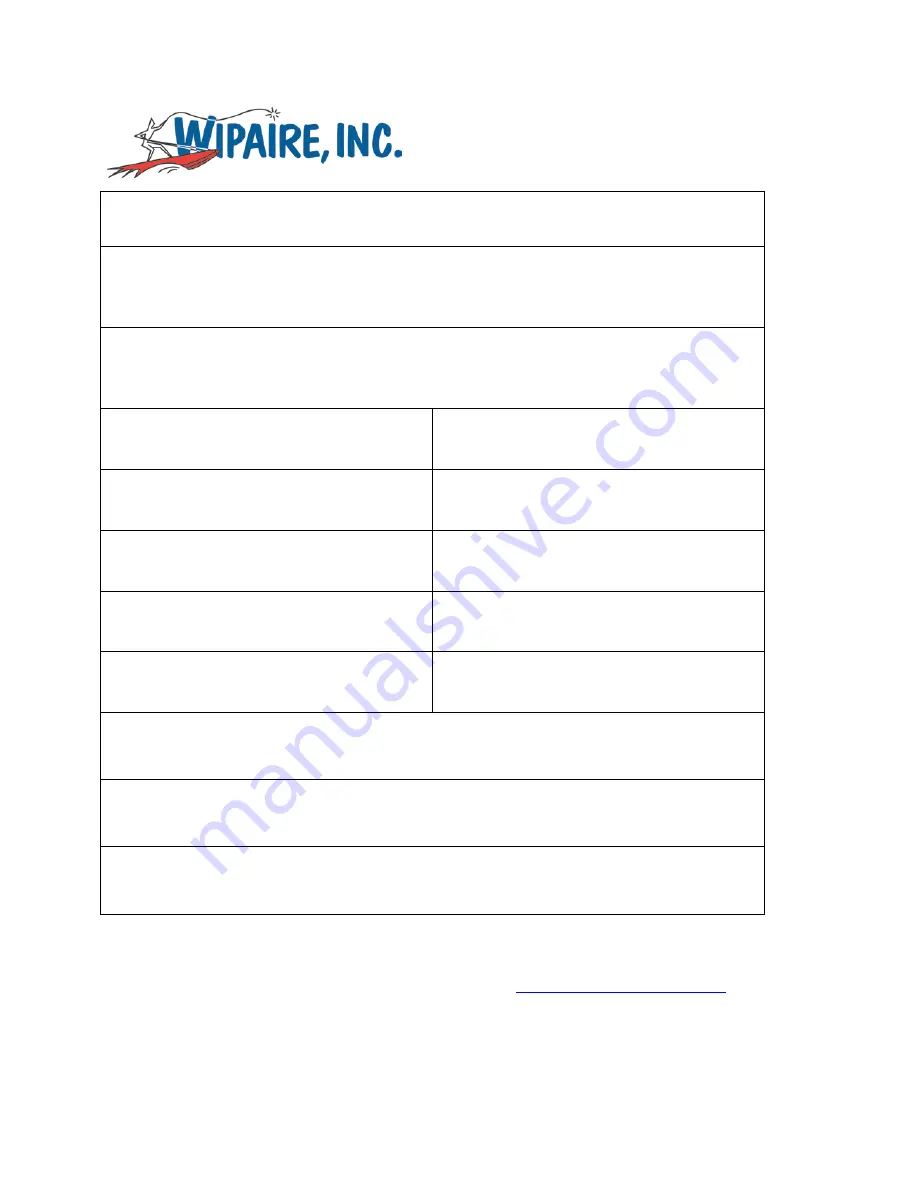
WIPLINE MODEL 8000 SERVICE MANUAL
Page 6 of 62
1002554 • Rev H
NEW CUSTOMER INFORMATION
Customer Name
Billing Address
Shipping Address
Phone Number
Fax Number
Purchasing Contact
Phone Number
Fax Number
Accounts Payable Contact
Phone Number
Fax Number
Type(s) of Aircraft Owned or Maintained
Model(s) of Floats and Skis Owned or Maintained
FedEx and/or UPS account number (if applicable)
Please return to Wipaire Customer Service:
Fax 651-306-0666
Phone 651-306-0459