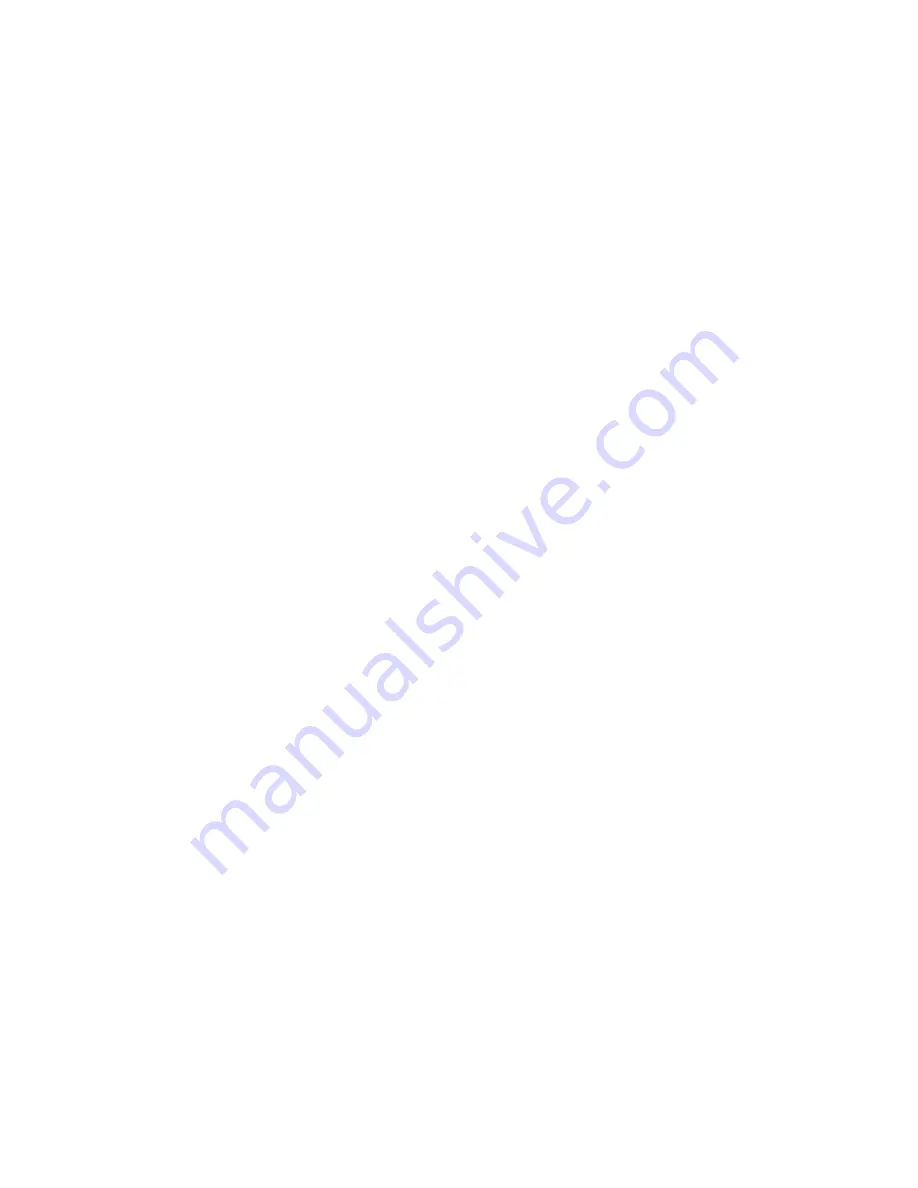
SHUTTING DOWN THE WELDER. (10 MINUTES COOL DOWN)
First, remove the nozzle tip while the welder is still in motion by positioning the nozzle tip in an
"UP"
position
, pointing into the air.
Switch the Drive Motor to "STOP" and put the drive gear lever to
"FREE WHEEL".
DO NOT TURN THE TOOL SWITCH OFF UNLESS YOU HAVE ALLOWED THE GUN TO "COOL"
DOWN. Failure to cool the gun prior to turning the power off may cause damage to the unit's
heating element and/or internal components. Make sure that the heat of the resting nozzle tip is
not pointed in the direction of the weights. Leaving the heat gun in the down position will cause
damage to the compression roller.
SEAM VERIFICATION FOR MODIFIED BITUMENS.
At the beginning of a day's seam welding, the operator of the unit must always perform destructive seam
analysis to make sure that he has selected the optimum mix of the temperature, speed and pressure for
his welder, and the particular membrane.
This seam analysis should be performed at the beginning of a day's production, and at any significant
change in operating environment, such as:
• A ten degree (F) change in ambient temperature.
• A significant change in cloud coverage.
• A moderate change in wind conditions (10MPH).
• A moderate change in humidity (10%).
• A noticeable change in the speed of the drive (indicating a significant change in voltage).
• Movement from a major shaded area to a major sunny area, or vice versa.
The operator should select a mix of speed, weight and temperature that is conservative, that is, he should
never run the welder at the "high edge" of welding. There should be a minimum of a 20% margin of safety
against peak speed and temperature mix.
The operator should be cautious of poor welds where there is a change in plane of the substrate surface.
For example, where there is a seam along the edge of a raised insulation board or where a fastener plate
is located too close to the edge of the seam, there may be insufficient compression of the seam.
Start and stop points in a seam are especially vulnerable to cold weld, so these should be marked and
checked carefully.
-6-
COOL DOWN 10 MINUTES