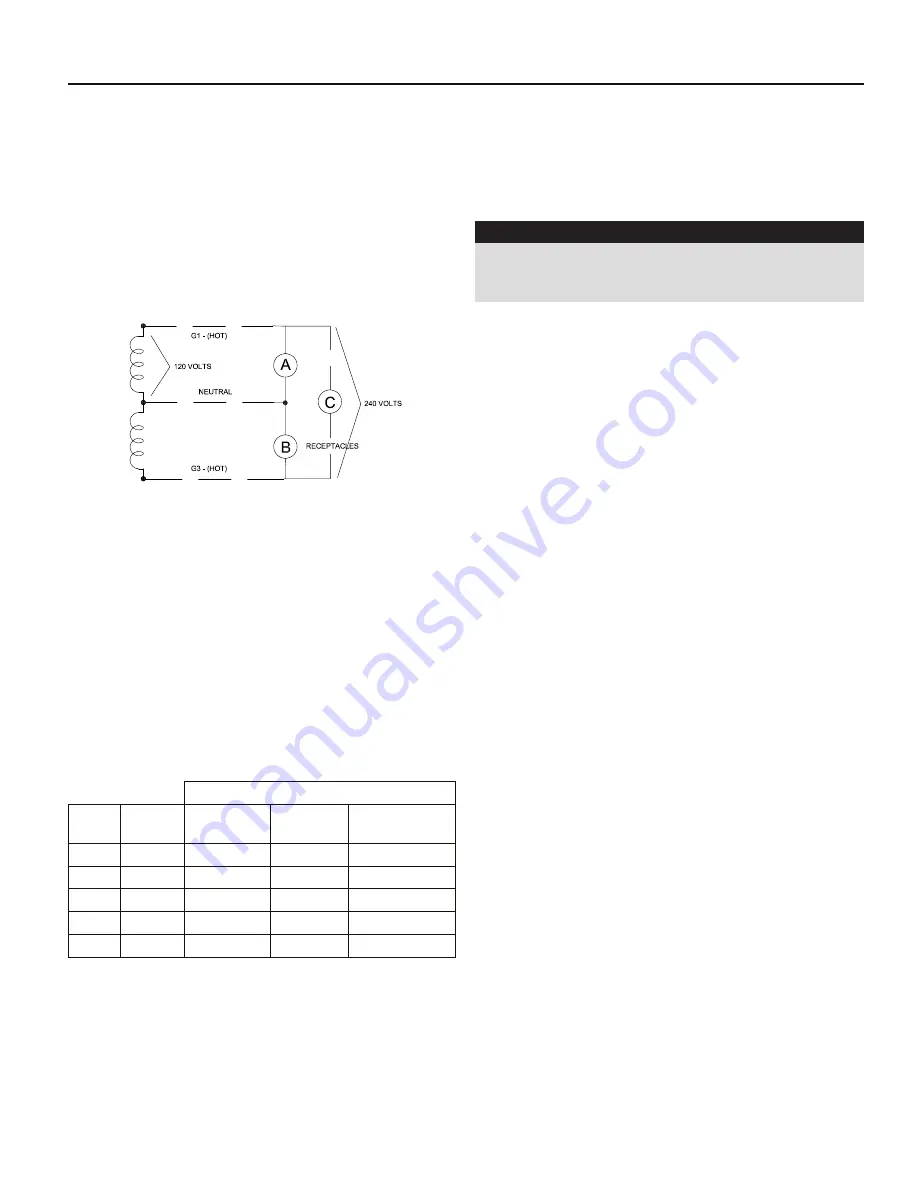
5
OPM-125/D
is not able to supply enough power to bring the electric
motor up to operating speed. The generator responds with
high initial starting current, but the engine speed drops
sharply. The overload may stall the engine. If allowed to
operate at very low speeds, the electric motor starting
winding will burn out in a short time. The generator
winding may also be damaged.
CAUTION: EQUIPMENT DAMAGE
Running the generator set under these conditions may
result in damage to the generator stator as well as the
motor winding.
The heavy surge of current required for starting motors
is required for only an instant. The generator will not be
damaged if it can bring the motor up to speed in a few
seconds of time. If difficulty is experienced in starting
motors, turn all other electrical loads off and if possible
reduce the load on the electric motor.
Motor starting capacity - 2HP code ‘G’ capacitor start
engine.
Trying to start a larger motor or higher code motor, i.e. ‘J’
or ‘K’, may result in damage to both the generator and the
electric motor, especially 120 Volt motors.
LOAD TYPES
This generator is designed and rated for general
commercial use. The running watts rating assumes a
variable load. If your application has a fixed load that does
not vary, an additional derate of 20% from the running
watts is recommended to ensure the longest useful life of
the engine and generator end.
UNIT CAPABILITIES
GENERATOR CONNECTIONS
EC6010: 120 Volt and 240 Volt receptacles are provided
for connection to various loads. The following diagram
represents this 5,160 watt (rated output) generator. A &
B represent the 120 volt output legs of this generator. Up
to 2,580 watts at 120 volts (43 Amps) can be drawn from
the receptacles attached to either A or B output legs. This
generator is capable of producing 21.5 Amps of 240 volt
current at C. Check the appliance or tool nameplates for the
current and voltage to insure compatibility. Remember that
power taken from C reduces the power available equally at
both A and B and vice versa.
STARTING ELECTRIC MOTORS
Electric motors require much more current (amps) to start
them than to run them. Some motors, particularly low cost
split-phase motors, are very hard to start and require 5 to 7
times as much starting current as running current. Capacitor
motors are easier to start and usually require 2 to 4 times
as much starting current as running current. Repulsion
Induction motors are the easiest to start and require only 1
1/2 to 2 1/2 times as much starting as running current.
Most fractional horsepower motors take about the same
amount of current to run them whether they are Repulsion
Induction (RI), Capacitor (Cap), or Split-Phase (SP) type. The
following chart shows the approximate current required to
start and run various types and sizes of 120 Volt 60 cycle
electric motors under average load conditions.
STARTING AMPS
HP
Running
Amps
Split Phase
Motor
Capacitor
Motor
Repulsion
Induction Motor
1/6
3.2
16 to 22
6 to 13
5 to 8
1/4
4.5
22 to 32
9 to 18
7 to 12
1/3
5.2
26 to 35
10 to 21
8 to 17
1/2
7.2
Not Made
14 to 29
11 to 18
1
13
Not Made
26 to 52
20 to 33
The figures given in the previous chart are for an
average load such as a blower or fan. If the electric
motor is connected to a hard starting load such as an air
compressor, it will require more starting current. If it is
connected to a light load, or no load such as a power saw,
it will require less starting current. The exact requirement
will also vary with the brand or design of the motor.
Self-exciting generators respond to severe overloading
differently than utility power. When overloaded, the engine