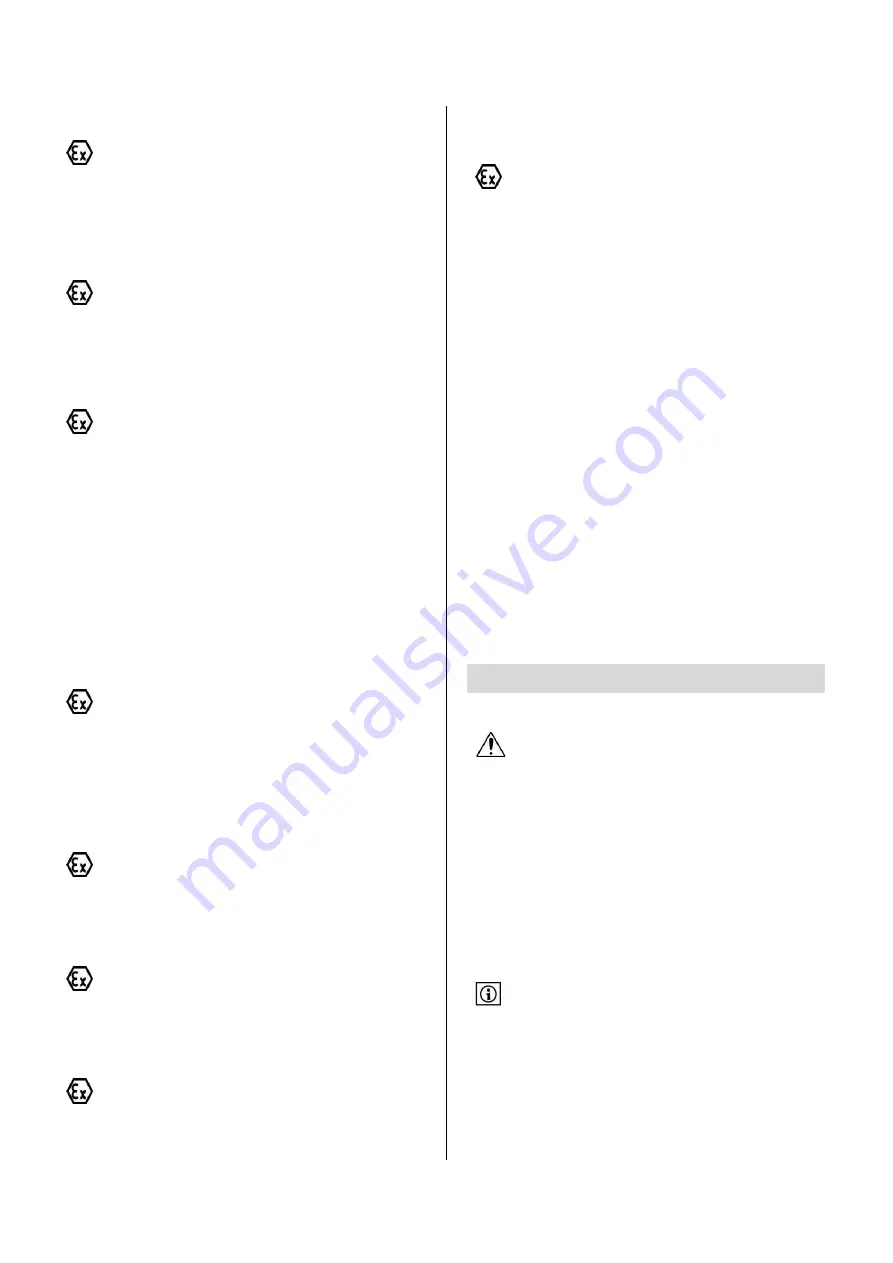
ENGLISH
7
The shaft seal and bearings temperature rise due to the minimum
permitted flow rate are taken into account.
The fluid temperatures indicated are given accordingly :
T1
350°C
T2
270°C
T3
175°C
T4
110°C
T5
75°C
T6
need WILO approval
A temperature sensor must be installed in pump casing to check
that fluid temperature never exceeds the permitted temperature
during priming time.
Motor overload trips should be correctly calibrated.
If pump is installed in dirty or dusty environment, it is necessary to
proceed with regular cleanings.
2.9.3
BUILD UP OF EXPLOSIVE MIXT URE
Ensure that pump casing and mechanical seal chamber are
correctly vented and that pump will not turn dry.
Self-priming pump are designed to ensure that an amount of liquid
always remains inside the pump casing even after pump stop. This
allows the pump to prime and never run dry. After a long term stop, it
will be necessary to check that there is still enough liquid inside the
pump (some liquids may evaporate due to external temperature) before
starting up the pump again.
Make sure that the pump runs with filled-in suction and discharge lines
to avoid build up of an explosive atmosphere. In addition, it is essential
that auxiliary sealing systems are properly filled and working.
To avoid potential hazards creation from fugitive emissions of vapor or
gas to atmosphere the surrounding area should be correctly ventilated.
2.9.4
PREVENTING LEAKAGE
The pump must only be used to handle the liquids for which it has
been defined.
If the pump is installed outdoor, make sure liquid containing parts are
drained and/or protected against freezing.
If leakage of liquid to the atmosphere can result in a hazard then a
leakage detection sensor should be installed.
2.9.5
COMPLETE UNIT
ATEX certification for a complete unit according to ATEX Directive
94/9/CE is given according to lower protection level of the
integrated component. This comment applies particularly to the electric
motor protection.
2.9.6
PUMP UNIT DELIVERED WITHOUT MOTOR /
WITHOUT SENSORS
If a partial delivery is required (electric motor, flexible coupling,
coupling guard or sensor not supplied), an integration certificate
will be established.
It will be the integrator’s responsibility to supply missing parts in order
to fulfill ATEX requirements for the complete machine.
2.9.7
COUPLING GUARD
The coupling guard used in a potentially ATEX atmosphere shall
meet following requirements :
Consist of non-sparking material (e.g brass),
Must be made of antistatic material,
Must be designed in such a way that the rotating parts will
not come in contact with any part of the guard after a choc.
2.9.8
MAINTENANCE TO AVOID HAZARD
When a pump is used in a potentially ATEX atmosphere it is
necessary to check regularly the following parameters and respect
a maintenance plan to ensure that the equipment runs in perfect
technical conditions.
Following regular checks are mandatory :
No leakage of the shaft seal,
Ball bearings temperature (on bracket housing surface),
No cavitations and no abnormal running noises,
Correct position of isolating valves and function of motorized
valves.
If some parts are worn or working in bad conditions the pump must be
stopped immediately and put in safety until maintenance operations are
performed. Origin of default(s) should be eliminated.
2.9.9
PREVENTING SPARKS CR EATION
Necessary measures must be taken to avoid sparks creation in case of
external impact.
Base plate and pumpset elements must be properly grounded. Ensure
continuity between components of the group.
It applies to :
-
Pump hydraulics,
-
Coupling guard,
-
Motor frame,
-
Baseplate.
The threaded hole or the earthing plate located on the base plate should
be used to make proper earthing.
3
TRANSPORT AND STORAGE
3.1
SAFETY MEASURES
Never rest below a suspended load.
Keep a safe distance while the load is being transported.
Check equipment weight and choose slings and other lifting
devices accordingly. Lifting equipments should be in good
conditions.
Adjust the length of the lifting devices so that pump or/and pumps
set is moved horizontally.
Lifting lugs or eyebolts that are sometimes attached to the pump
or to the motor should not be used to lift a complete pump set.
They should be used only to lift pump parts during dismantling
operations.
Use the lifting points that are mentioned on the pump set or refer
to following information.
3.2
DELIVERY
After reception of goods, the delivered items must be inspected
for damage. Check that all parts are present (check description
and quantities against delivery/shipping documents). If any parts are
damaged, missing or if transportation damage is visible, this should be
noted on the freight documentation or on the delivery note.
Do not separate attached documentation from the pump.
Unpack the good and eliminate packaging according environmental
requirements.
Do not remove caps from pump flanges if pump will not be installed
immediately.
Summary of Contents for Wilo-Drain SP
Page 2: ......
Page 3: ...FR Notice de montage et de mise en service Wilo Drain SP 4186313 Ed 02 2013 10 Wilo...
Page 4: ...FRAN AIS 2...
Page 25: ......
Page 26: ...24...
Page 27: ...EN Installation and operating instructions Wilo Drain SP 4186313 Ed 02 2013 10 Wilo...
Page 28: ...ENGLISH 2...
Page 49: ...ENGLISH 23...
Page 50: ......
Page 51: ......