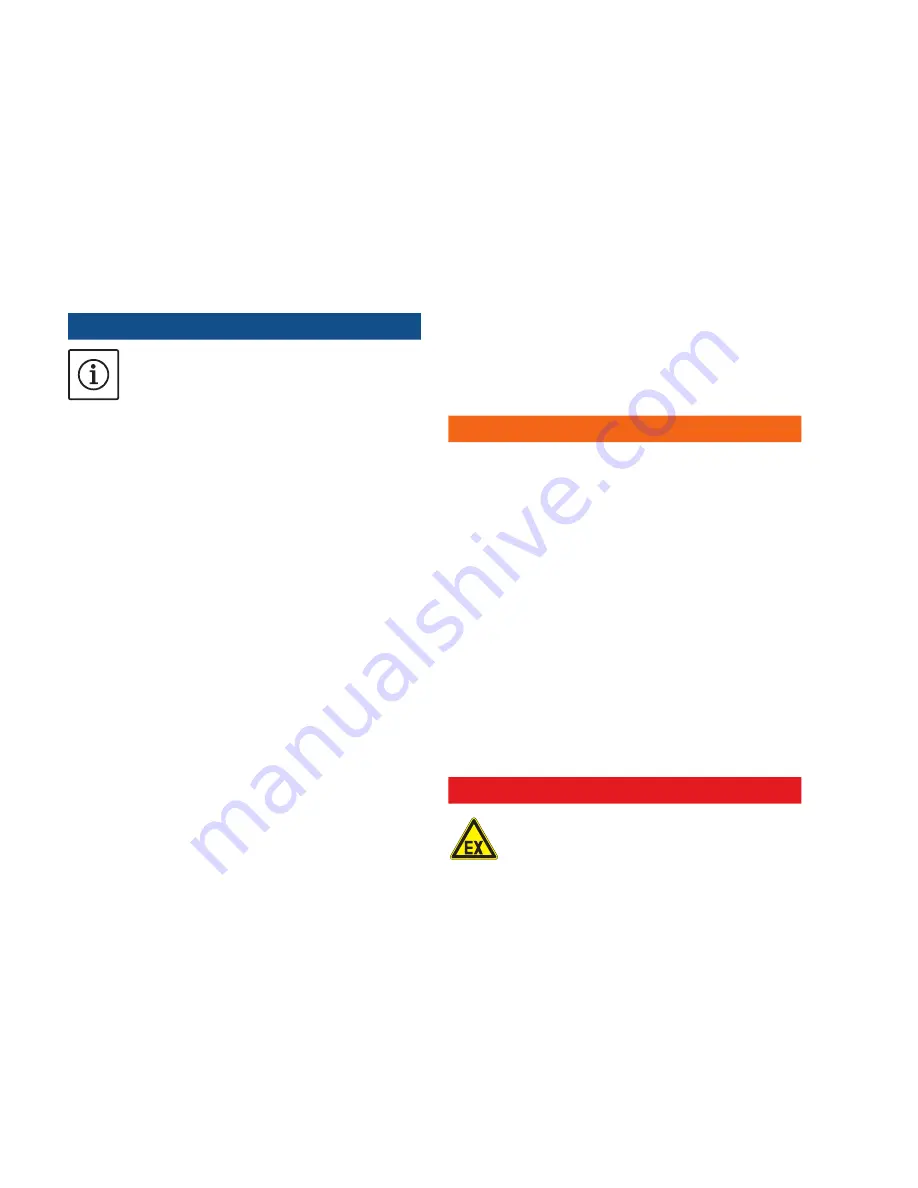
14
WILO SE 2015-07 V05 Letter
US English
PRODUCT DESCRIPTION
3.2.1. Hydraulics
Rotodynamic hydraulics with single-channel or
vortex impeller, with horizontal flange connection
on the pressure side.
The hydraulics are not self-priming, in other
words, the fluid must flow in either under natural
pressure or under supply pressure.
3.2.2. Motor
Single or three phase AC dry motors are used as the
motors. The motor is cooled by the fluid around it.
The waste heat is transferred directly to the fluid via
the motor housing.
NOTE
When the motor is non-immersed, observe and
comply with the specifications for “non-immersed
operating mode”!
In the single-phase version, the start and operat-
ing capacitor is integrated in an external capacitor
switchgear in the connection cable.
The connection cable has a length of 40 ft (12.5 m),
is longitudinally watertight, and is available in fol-
lowing versions:
• Cable with plug
• Bare cable end
3.2.3. Monitoring equipment
•
Motor compartment monitor:
The motor compartment monitor signals water
ingress into the motor compartment.
•
Thermal motor monitor:
The thermal motor monitor protects the motor
winding from overheating. Bimetallic strips are used
for this as standard. The motors can be equipped
with PTC sensors as an option.
•
P 13 motor:
Single-circuit temperature monitoring as tem-
perature limiter. When the threshold is reached,
the unit
must
switch off!
•
P 17 motor:
2-circuit temperature monitoring as temperature
controller and temperature limiter. When the low
threshold is reached, a preliminary warning
may
be issued, when the high threshold is reached, the
motor
must
switch off!
The motor can also be fitted with an external pencil
electrode to monitor the sealing chamber. This sig-
nals if there is water ingress into the sealing cham-
ber through the mechanical seal on the fluid side.
3.2.4. Seal
The seal for the fluid and the motor compart
-
ment is made via two mechanical seals. The sealing
chamber between the mechanical seals is filled with
environmentally safe medicinal white oil.
3.2.5. Materials
•
Motor housing:
ASTM A48 Class 35/40B (EN-GJL-250)
•
Hydraulic housing:
ASTM A48 Class 35/40B (EN-GJL-250)
•
Impeller:
ASTM A48 Class 35/40B (EN-GJL-250)
•
Shaft end: AISI 420 (1.4021)
•
Static gaskets: Nitrile (NBR)
• Seal
•
On pump side: SiC/SiC
•
On motor side: C/MgSiO4
3.2.6. Attached plug
In the "P" version, there is a corresponding plug for
either single-phase or three-phase power sockets.
These plugs are designed for use in commercially
available sockets and are not watertight (overflow-
proof).
CAUTION: beware of moisture!
Ingress of moisture will result in damage to the
plug. Never immerse the plug in fluid and always
protect it from moisture.
3.3. Operation in an explosive atmosphere
Pumps with the “Ex” marking are suitable for opera
-
tion in an explosive atmosphere. The pumps must
meet certain guidelines for this type of use. Certain
rules of conduct and guidelines must be also fol-
lowed by the operator.
Pumps that have been approved for use in an explo-
sive atmosphere must be marked as follows on the
rating plate:
•
“Ex” symbol
•
Information on Ex classification
For use in an explosive atmosphere, observe the
further specifications in the appendix to this
manual
DANGER: from incorrect use!
When used in an explosive atmosphere, the
pump must have a corresponding approval. Also,
the accessories must be approved for this appli-
cation. Check the pump as well as all accessories
before use to verify that they are approved in
accordance with regulations.
3.4. Operating modes
3.4.1.
Operating mode S1 (permanent operation)
The pump can operate continuously at the rated
load without exceeding the permissible tempera-
ture.
Summary of Contents for Rexa PRO Series
Page 5: ...Fig 9 1...