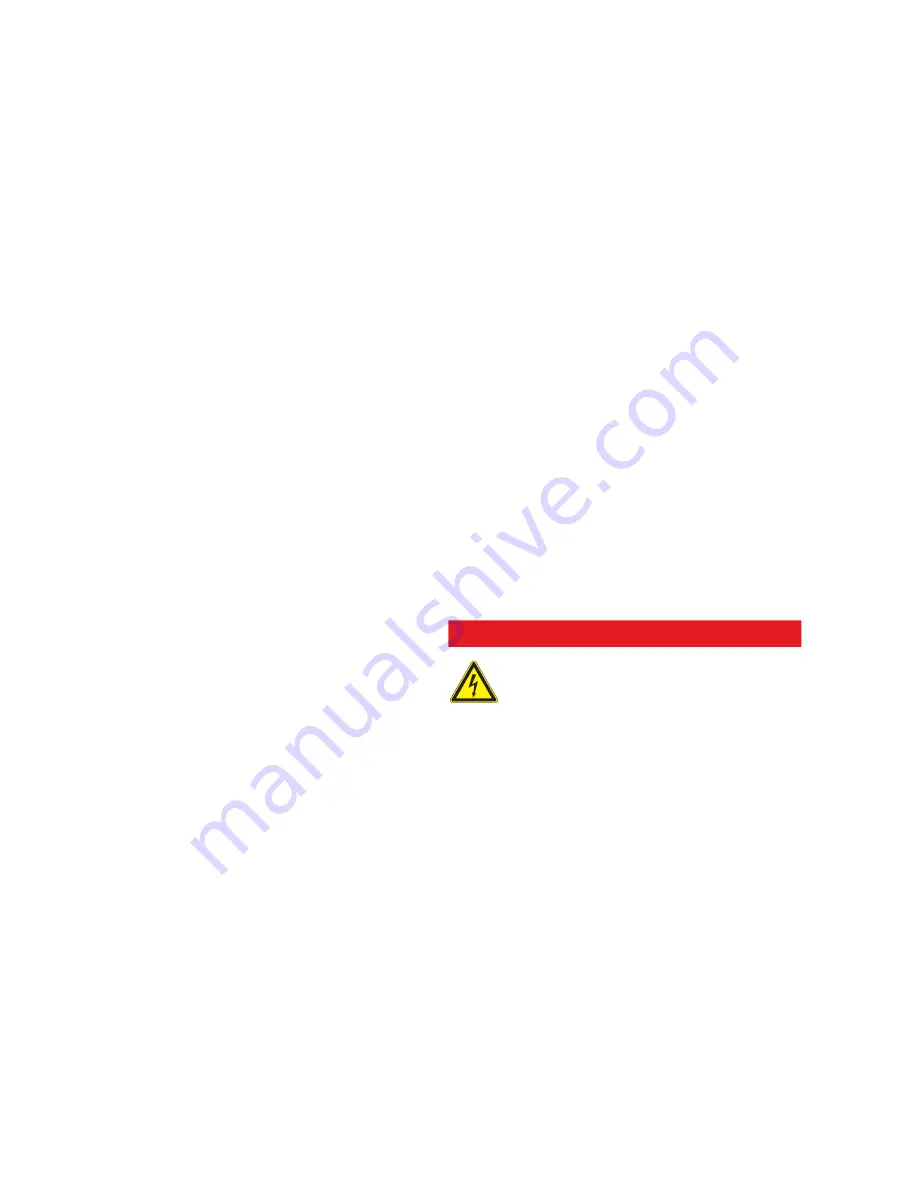
24
WILO SE 2015-07 V05 Letter
US English COMMISSIONING
Star-delta activation
The motor protection setting depends on the
installation:
•
Motor protection installed in the motor line: Set
the motor protection to 0.58 x the rated current.
• Motor protection installed in the power supply
cable: Set the motor protection to the rated cur
-
rent.
The maximum start-up time in star connection is
3 seconds.
Soft start activation
• At full load, the motor protection should be set to
the rated current at the duty point. At partial load,
we recommend that the motor protection be set
5% above the current measured at the duty point.
• The current consumption must be below the rated
current throughout the entire operation.
• Due to the upstream motor protection, starting or
stopping should be completed within 30 seconds.
• To avoid power dissipation during operation, bypass
the electronic starter (soft start) once normal op-
eration is reached.
Pumps with a plug
At full load, the motor protection should be set
to the rated current shown on the rating plate. At
partial load, we recommend that the motor protec-
tion be set 5% above the current measured at the
duty point.
Plugs are not immersion-proof. Note the protec-
tion class (IP). The socket must be installed where
it will not be submersed.
5.6.3. Operation with frequency converters
Operation on a frequency converter is possible.
Note the information about this in the appendix.
6. Commissioning
The “Commissioning” section contains all the im
-
portant instructions for the operating personnel for
starting up and operating the pump.
The following conditions must be adhered to and
monitored:
• Type of installation
• Operating mode
• Minimum water submersion/max. immersion depth
These general conditions must also be checked
after a long period without operation, and any
defects detected must be repaired!
Always keep this manual either by the pump or in a
place specially reserved for it, where it is accessible
for the entire operating personnel at all times.
In order to prevent damage or serious injury when
commissioning the pump, the following points must
be observed:
• Commissioning of the pump may only be carried out
by qualified and trained personnel in accordance
with the safety instructions.
• All persons working on or with the pump must have
received, read, and understood this operating and
maintenance manual.
• All safety devices and emergency cut-outs must be
connected and checked to ensure that they work
properly.
• Electrical and mechanical adjustments must be
made by qualified personnel.
•
The pump is suitable for use under the specified
operating conditions.
• In general, people should be kept out of the working
area of the pump. No persons should be allowed in
the working area during startup or operation.
• When working in sumps, a second person must be
present. Adequate ventilation must be ensured if
there is danger of toxic gases forming.
6.1. Electrical system
Connect the pump and install the power supply
cables as described in the “Installation” section and
in accordance with applicable national regulations.
The pump must be properly protected and ground-
ed.
Ensure correct direction of rotation. If the direction
of rotation is incorrect, the pump will not perform as
specified and may be damaged.
Ensure all monitoring devices are connected and
have been tested.
DANGER: electrical hazard!
Electrical current can cause fatal injuries if not
handled correctly! All pumps with free cable
ends (i.e. without plugs) must be connected by a
qualified electrician.
6.2. Rotation control
The pump is checked and adjusted in the factory to
ensure that the direction of rotation is correct. The
connection must be made according to the wiring
markings.
A test run must be performed under general oper-
ating conditions!
6.2.1. Checking the direction of rotation
The direction of rotation must be checked by a
local electrician using a phase sequence tester. For
the correct direction of rotation, a clockwise phase
sequence must be present.
The pump is not approved for operation with a
counterclockwise phase sequence!
6.2.2. If the direction of rotation is incorrect
If the direction of rotation is incorrect for direct
start motors, two phases must be swapped. In the
case of motors with star-delta starting, the con-
Summary of Contents for Rexa PRO Series
Page 5: ...Fig 9 1...