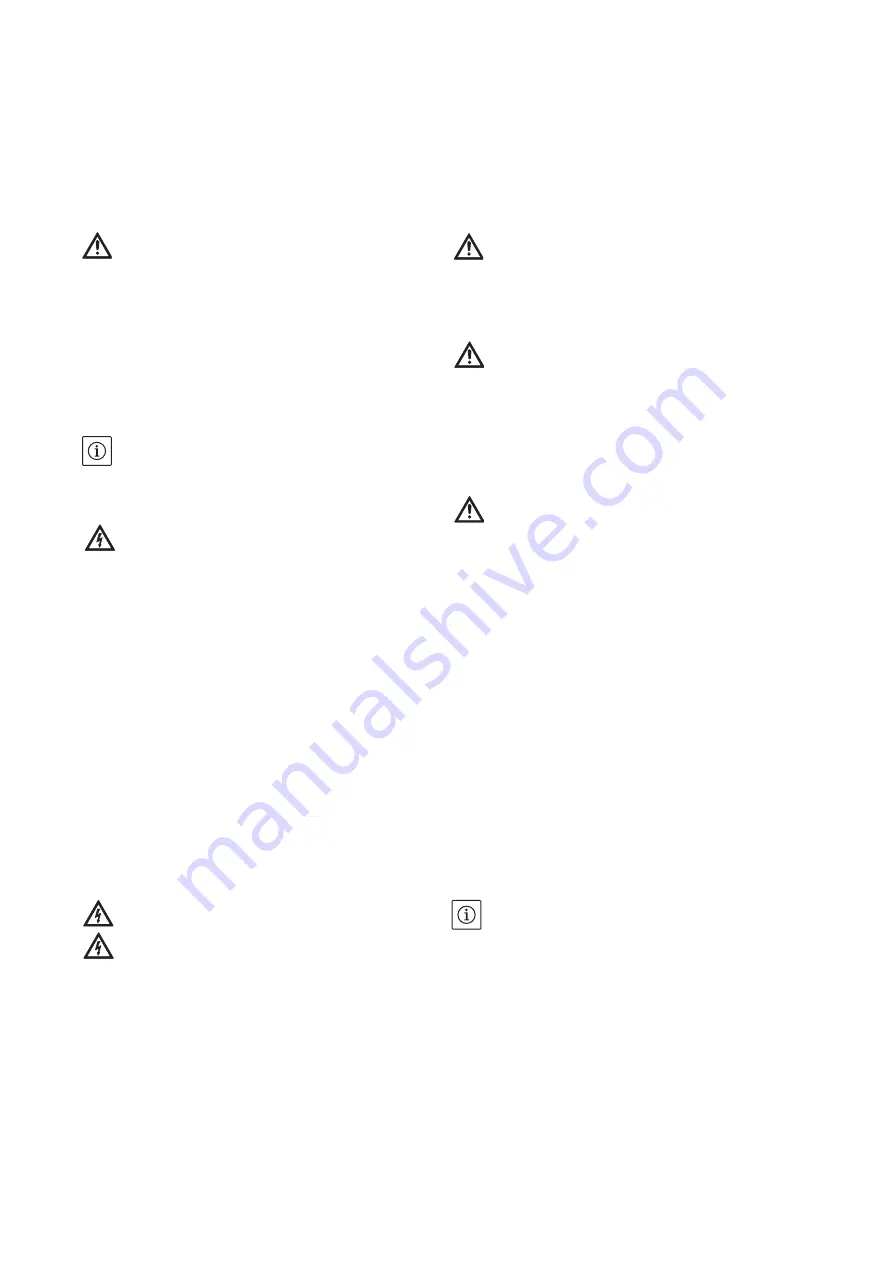
13
WILO AG 02/2006
English
5.2 Hydraulic connections
By threaded tubes to screw directly on the oval
tapped counterflanges delivered with the pump.
The diameter of the pipe must never be smaller
than the one of the counterflange.
Limit the length of the suction pipe and avoid all
features that cause losses of head (bends, valves,
tapers...).
CAUTION !
Connections has to correctly sealed:
No air entrance is allowed on the suction pipe
which is showing a mounting declivity (2 %)
(fig. 1).
- Use supports or collars so that the pump does
not bear the weight of the pipes.
- The circulation sense of the fluid is indicated on
the identification label of the pump.
- Connect the non-return valve to the pump
discharge to protect it from hammer blow
effects.
To pump water with a large content of air or hot
water,we recommend installing the by-pass kit
(fig. 1).
5.3 Electrical connections
The electrical connections and the inspections
have to be done by a qualified electrician and
comply with the applicable local standards.
- The electrical characteristics (frequency, voltage,
nominal current) of the motor are mentionned on
the name plate).
- check if the motor it complies with the mains
supply used.
- The motors must be protected by a circuit-
breaker set to the current mentionned on the
name plate of the motor.
- Provide a fuse disconnecting switch (type aM) to
protect the mains supply.
Supply network
- Use an electrical cable conforming with the
National Electric Supply Company.
-
Three-phase:
4 conductors (3 earth).
If necessary, cut an opening in the terminal box,
fit the cable gland stuffing box and connect the
motor as shown by the diagram inside the cover
of the terminal box (fig. 4).
DO NOT FORGET TO CONNECT TO EARTH.
CAUTION ! A connection error would damage
the motor. The power cable must never touch
the pipe or the pump; make sure that it is shel-
tered from any humidity.
The electric motors used on the pumps can be
connected to a frequency converter. Strictly fol-
low the instructions given by the data sheet of
the converter's manufacturer.
The converter must not generate voltage peaks
at the motor terminals higher than 850 V and
dU/dt (Voltage/Time variation) higher than
2500 V/µs. If the value of the voltage signal are
higher than those, risk of damage the motor are
to forecast.
In the contrary provide a LC filter (inductance –
capacitor) between the converter and the motor.
It must be connected to the motor with a mini-
mum length cable, armoured if necessary.
6. Starting up
6.1 Prior cleaning
An hydraulic test is carried out for each pump in
our factory. If some water stays inside them. It is
recommended for hygien reasons to clean the
pump before using it with potable water supply.
6.2 Filling - degassing
CAUTION !
Never operate the pump dry, even
briefly.
Pump under pressure (fig. 2)
- Close the discharge valve (3),
- Open the venting plug (5), and the suction valve
(2) and completely fill the pump.
Close the venting plug only after water flows out
and complete air exit.
WARNING ! In hot water, a stream of water
may escape from the venting port. Take all
required precautions as regards persons and
motor.
Pump in suction
Two possible cases:
1st CASE (fig. 5-1):
- Close the discharge valve (3), open the suction
valve (2).
- Remove the venting plug (5).
- Unscrew the bottom drain-priming plug (6)
located on the pump casing 4 to 5 turns.
- Put a funnel into the venting plug port and com-
pletely fill the pump and the suction pipe.
- After water flows out and total air exit, filling is
complete.
- Screw the venting plug and the bottom drain-
priming plug back in.
2nd CASE (fig. 5-2):
Filling can be made easier by fitting on the suc-
tion pipe of the pump, a vertical pipe fitted with
a Ø
1/2
” stopcock and a funnel.
The length of the pipe must be at least 50 mm
taller than the venting level.
- Close the discharge valve (3), open the suction
valve (2).
- Open the stopcock and the venting plug.
- Unscrew 4 to 5 turns the drain-priming plug (6).
- Fill the pump and the suction pipe completely
until water flows out of the venting plug (5).
- Close the stopcock (which can be left in place),
remove the pipe and close the bleed device (5)
and screw again the drain-priming plug (6).