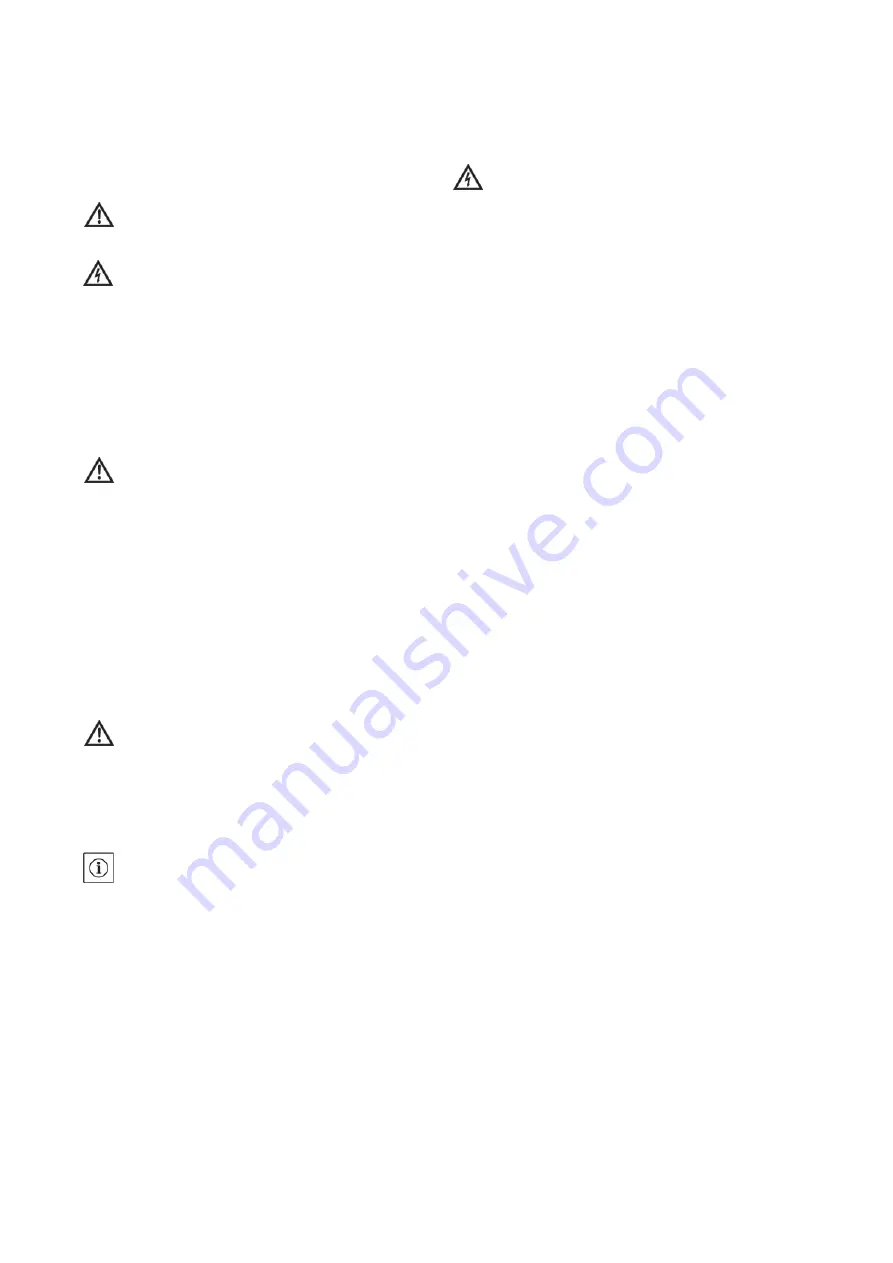
8
WILO SE 03/2017
English
7. Installation and electrical connection
All installation and electrical connection work
must be carried out solely by authorised and
qualified personnel, in accordance with applica-
ble regulations.
WARNING! Physical injuries!
The applicable regulations for the prevention of
accidents must be complied with.
WARNING! Risk of electric shock!
Danger from electric current must be eliminated.
7.1 Upon receipt of the product
• Unpack the pump and recycle or dispose of the
packaging in an environmentally responsible
manner.
7.2 Installation
• The pump must be installed in a dry, well-venti-
lated location free of frost.
ATTENTION! Risk of damage to the pump!
The presence of foreign matter or impurities in
the pump housing may affect the functioning of
the product.
• We recommend carrying out all soldering and
brazing work before installing the pump.
• Rinse the circuit completely before installing
and commissioning the pump.
• Remove the blanking caps on the pump hous-
ing before installation.
• The pump must be installed in a place easy to
access for the purposes of inspection or replace-
ment.
• Secure the pump through 2 slotted holes on the
pedestal bearing (for Ø M5 fasteners) (Fig. 5)
WARNING! Risk of accident due to hot surfaces!
The pump must be installed in such a way that
no one can touch the hot surfaces of the product
when it is in operation.
• Install the pump in a horizontal position, on a flat
concrete surface, using the appropriate acces-
sories.
NOTE: As the pump may have been tested in the
factory, there may be some residual water in the
product. We recommend rinsing the pump.
7.3 Connection to mains
• We recommend installing gate valves on the
suction and pressure sides of the pump. (Fig. 3)
• The pipe cross-section must be at least equal
to the diameter of the suction port on the pump
housing.
• A non-return valve can be placed at the pres-
sure connection to protect the pump from water
hammer.
• If connected directly to the public potable water
mains, the suction pipe socket must also be
fitted with a non-return valve and a stop valve.
(Fig. 2)
• If connected indirectly via a tank, the suction
pipe socket must be fitted with a suction strainer
to stop impurities from entering the pump, and a
non-return valve.
7.4 Electrical connection
ATTENTION! Risk of electric shock!
Danger from electrical current must be eliminat-
ed.
• Have all electrical work carried out by a quali-
fied electrician only!
• Before any electrical connection is made, the
pump must be de-energised (switched off) and
protected against unauthorised restarting.
• To ensure safe installation and operation, the
unit must be earthed correctly with the earth
terminals of the power supply.
• Check that the nominal current, the voltage and
the frequency correspond to the information on
the motor’s rating plate.
• The pump must be connected to the network via
a rigid cable with male connector or a power iso-
lator.
Use a cable conforming with applicable stan-
dards (3 cores: 2 earth):
H05RN-F 3 G 1.5 minimum
H05RN-F 3 G 2.5 maximum
• The connecting cable should be routed so that it
never comes in contact with the water main and/
or the pump housing and motor housing.
• The pump/unit should be earthed in accordance
with the local regulations. A residual current
device may be used for additional protection.
• Unscrew the cap of the terminal box.
• Remove the cap.
• Turn the threaded cable connection the other
way around.
• Connect to the power supply. The connection
to the power supply must follow the connection
diagram (Fig. 1).
• Put the cap back on the terminal box.
• Screw the cap firmly in place on the terminal box.
Summary of Contents for HiPeri 1-4
Page 2: ...Fig 1 Fig 2 L1 L2 N L HA max 7m ...
Page 3: ...Fig 3 Fig 4 ou or ...
Page 25: ...25 Notes ...