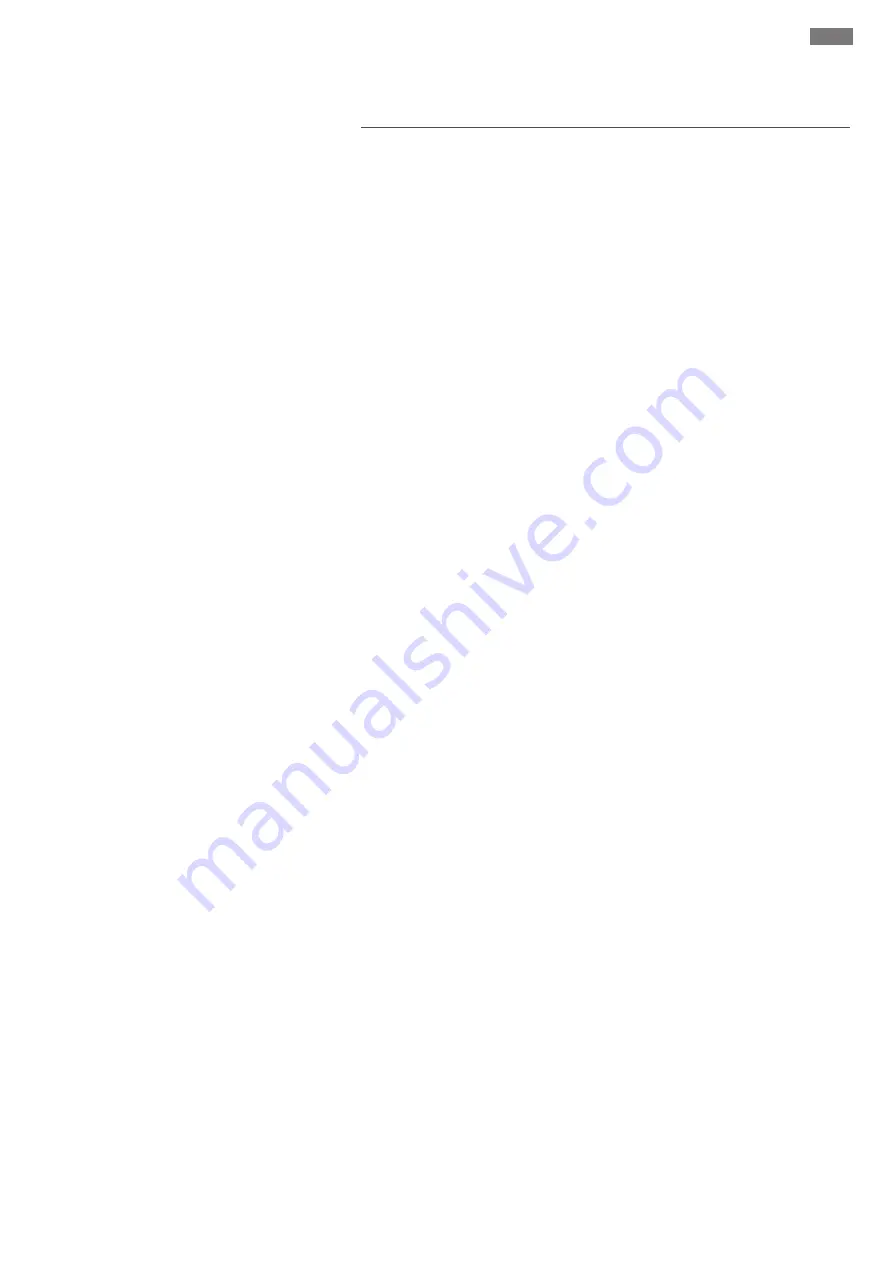
Maintenance and repair
en
Installation and operating instructions Wilo-EMU TR/TRE 50-2 ... 120-1
33
the maximum bearing capacity of the lifting equipment! Check that lifting equip-
ment is functioning properly before use!
ƒ
Carry out maintenance tasks in a clean location with good lighting and ventilation.
Set the mixer down horizontally on a firm surface and secure it against tipping over /
slipping away.
NOTICE! Do not set the mixer down on the propeller!
ƒ
Only carry out maintenance tasks mentioned in these installation and operating in-
structions.
ƒ
Wear the following protective equipment while performing maintenance tasks:
–
Safety goggles
–
Safety shoes
–
Safety gloves
9.1
Personnel qualifications
ƒ
Electrical work: A qualified electrician must carry out the electrical work.
ƒ
Maintenance tasks: The technician must be familiar with the use of operating fluids
and their disposal. In addition, the technician must have basic knowledge of mech-
anical engineering.
9.2
Operator responsibilities
ƒ
Provide the necessary protective equipment and make sure that the personnel wears
it.
ƒ
Collect operating fluids in suitable tanks and dispose of properly.
ƒ
Dispose of protective clothing used in accordance with regulations.
ƒ
Use only original parts of the manufacturer. Use of parts other than the original parts
releases the manufacturer from any liability.
ƒ
Collect any leakage of fluid and operating fluid immediately and dispose of it ac-
cording to the locally applicable guidelines.
ƒ
Provide the tools required.
ƒ
If flammable solvents and cleaning agents are used, open flames, naked lights and
smoking are prohibited.
9.3
Operating fluid
9.3.1
Oil types
Medicinal white oil is filled into the sealing chamber ex-factory. The following oil types
are recommended when changing the oil:
ƒ
Aral Autin PL*
ƒ
Shell ONDINA 919
ƒ
Esso MARCOL 52* or 82*
ƒ
BP WHITEMORE WOM 14*
ƒ
Texaco Pharmaceutical 30* or 40*
The gear and pre-chamber has been filled with CLP gear oil (ISO VG 220). The following
oil types are recommended when changing the oil:
ƒ
Aral Degol BG 220
ƒ
Shell Omala 220
ƒ
Esso Spartan EP 220
ƒ
BP Energol GR-XP 220
ƒ
Texaco Meropa 220
ƒ
Tripol Food Proof 1810/220*
All oil types marked with “*” are approved for use with foods in accordance with
“USDA-H1”.
9.3.2
Grease
Use the following greases:
ƒ
Esso Unirex N3
ƒ
Tripol Molub-Alloy-Food Proof 823 FM (with
“USDA-H1” approval
)
9.3.3
Filling quantities
ƒ
Pre-chamber: 1.20 l (41 US.fl.oz.)
ƒ
Gear chamber: 0.50 l (17 US.fl.oz.)
ƒ
Sealing chamber: 1.10 l (37 US.fl.oz.)
Stated filling quantities apply for described installation types. Refer to the enclosed
data sheet for the filling quantities required for deviating installation types.
9.4
Maintenance intervals
To ensure reliable operation, maintenance tasks must be carried out regularly. Depend-
ing on the real ambient temperatures, maintenance intervals different to those men-
tioned in the contract can be established! If strong vibrations occur during operation,