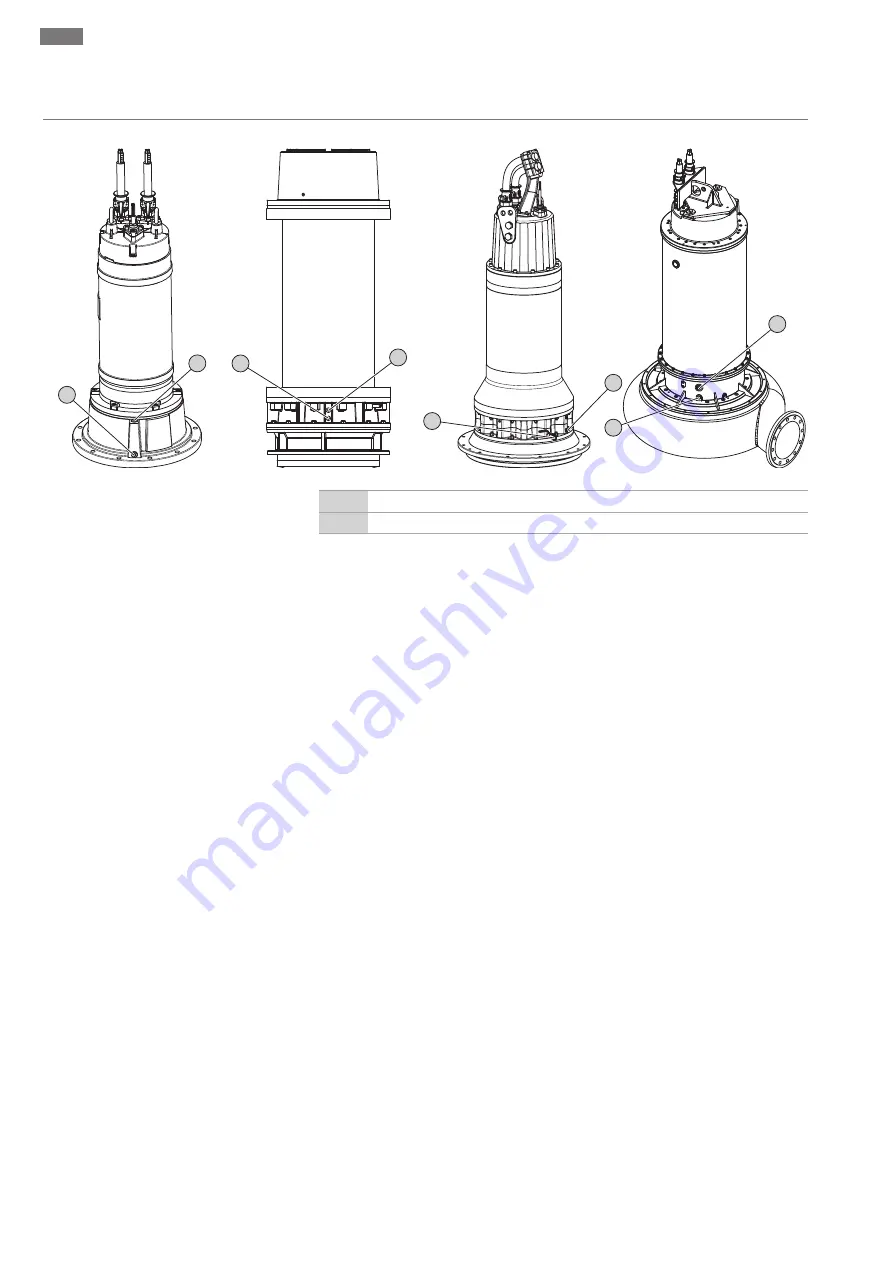
en
Maintenance and repair
46
WILO SE 2019-01
Motors T 30, T 34, T 42, T 49, T 50.1, T 56, T 57, T 63.x, T 72
-
-
T 30, T 34, T 42
T 50.1, T 57, T 63.1
T 63.2, T 72
T 49, T 56
+
+
+
+
-
-
Fig. 16:
Sealing chamber: Oil change
+
Add the oil to the sealing chamber
-
Drain the oil in the sealing chamber
‡
Protective equipment has been put on!
‡
Pump has been dismantled and cleaned (decontaminated if required).
1. Place the pump upright on a firm surface.
WARNING! Risk of hands being crushed.
Ensure that the pump cannot fall over or slip away!
2. Place a suitable tank to collect the operating fluid.
3. Unscrew the screw plug
(+)
slowly, but do not unscrew it completely.
WARN-
ING! Overpressure in the motor! Stop turning the screw plug further if hissing
or whistling is audible! Wait until the pressure has completely dissipated.
4. After the pressure has dissipated, fully unscrew the screw plug
(+)
.
5. Unscrew screw plug
(-)
and drain the operating fluid. If a shut-off ball cock is in-
stalled on the outlet opening, open the shut-off ball cock.
6. Check the operating fluid: Notify customer service if the operating fluid contains
swarf!
7. If a shut-off ball cock is installed on the outlet opening, close the shut-off ball
cock.
8. Clean the screw plug
(-)
, replace the seal ring and screw it back in.
Max. tightening
torque: 8 Nm (5.9 ft·lb)!
9. Pour the new operating fluid in through the hole of the screw plug
(+)
.
⇒ Comply with the specifications for operating fluid type and quantity!
10.Clean the screw plug
(+)
, replace the seal ring and screw it back in.
Max. tightening
torque: 8 Nm (5.9 ft·lb)!
Summary of Contents for EMU FA
Page 2: ......