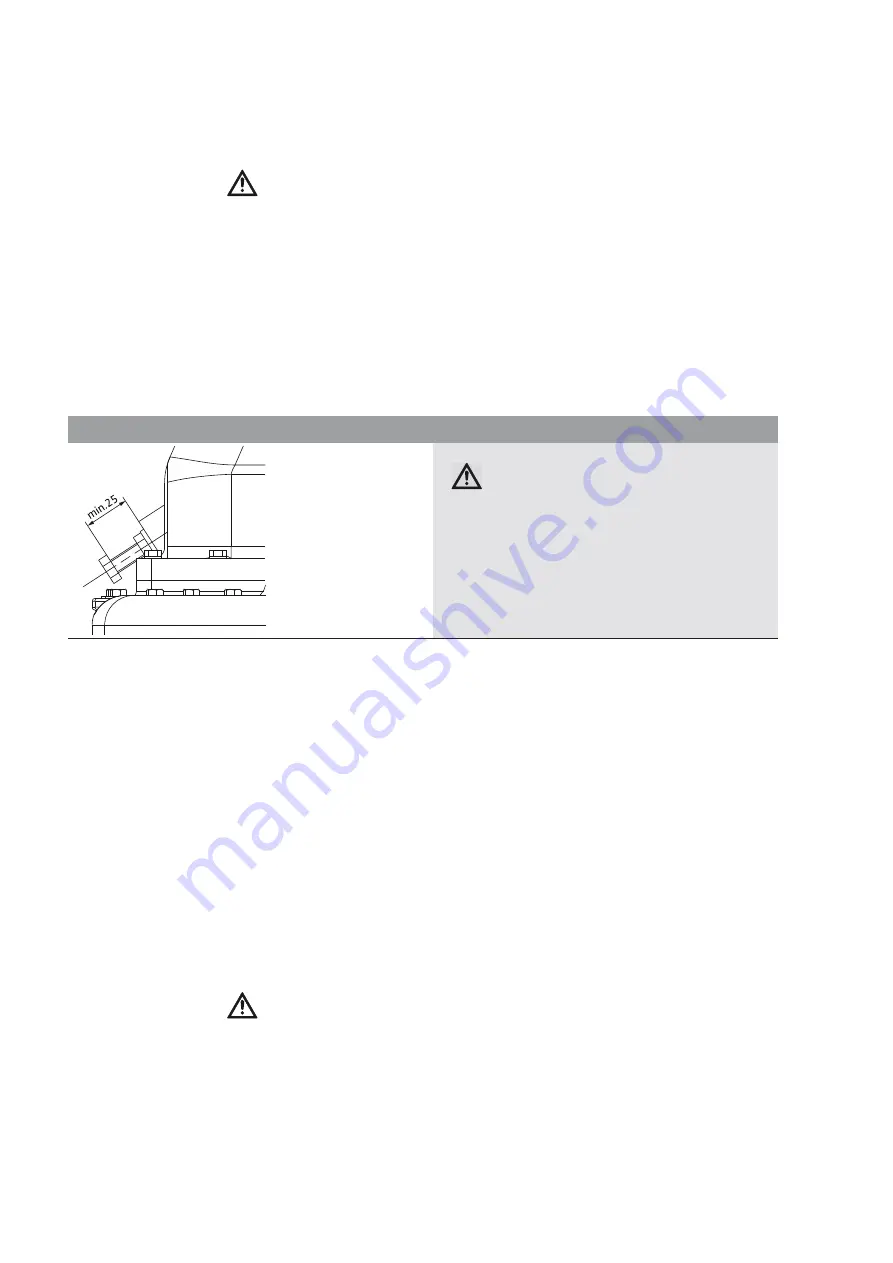
English
34
WILO SE 03/2011
8 Commissioning
It is recommended to have commissioning performed by Wilo's customer service.
8.1 Inspection of the unit
CAUTION! Risk of property damage!
Dirt and solids as well as incorrect commissioning can cause damage to the unit or indi-
vidual components during operation.
• Clean the entire unit to remove any dirt, in particular solids, prior to commissioning.
• Observe the installation and operating instructions for the switchgear and the acces-
sories.
Commissioning may be carried out only if the relevant safety regulations, VDE regulations
as well as regional regulations are met.
• Check for the presence of and proper versions of all required components and connections
(inlets, discharge pipe with check valve, ventilation via the roof, floor fixation, electrical
connection).
• Check the position of the venting screw on the non-return valve to make sure the flap can
move freely in its seat and for the sealing position of the sealing nut.
8.2 Initial commissioning
• Plug in the mains plug.
• Check or make the settings acc. to sections 8.2.1, 8.2.2 and 8.2.3.
• Open the check valves.
• Fill the system via the connected inlet until each pump has pumped out at least once and
the pressure pipeline is completely filled.
The filling level in the tank must not rise when the discharge piping is filled and the inlet
closed. If the filling level continues to rise, the flap of the non-return valve is leaky (must
check the flap and the position of the venting screw).
For a test start-up, the “manual mode” button on the switchgear can also be pressed
before reaching the switch-on level in the tank.
• Check the unit and pipe joints for impermeability and perfect function (switch the pump
on and off).
• Fill the unit with a maximum possible inlet and check whether the unit is working perfectly.
Observe in particular:
• Correct position of switching points.
• Adequate volume flow of the pumps at maximum flow whilst the pump is running (level
must fall).
• Vibration-free operation of the pumps without air inclusions in the fluid.
CAUTION! Risk of property damage!
Air in the fluid causes considerable vibrations which can destroy the pumps and the
entire unit, depending on the respective operating conditions of the pumps. The mini-
mum water level in the tank for the “Pump ON level switching point” (see technical
data) must be guaranteed.
Fig. 12: Position of the venting screw while the unit is in operation
CAUTION! Risk of property damage!
If the venting screw with sealing nut is not in
the required position, this can lead to damage
on the flap and unit, as well as to high noise
development (Fig. 12).
Summary of Contents for DrainLift XL
Page 2: ...Fig 10...
Page 3: ...Fig 11...