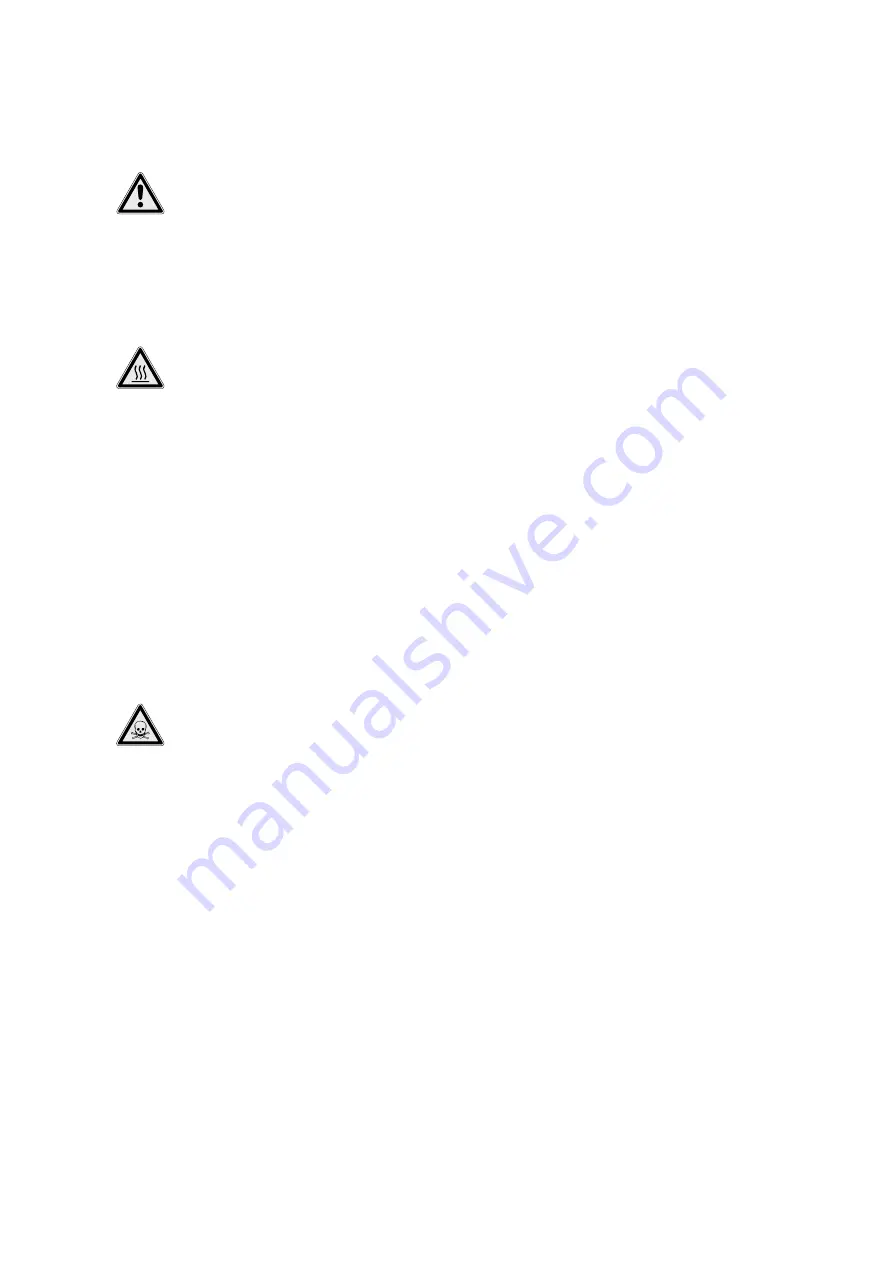
Installation and operating instructions Wilo-DrainLift S 39
MAINTENANCE AND REPAIR English
• Lifting equipment in perfect technical condition
and officially approved load‑bearing equipment
must be used for lifting and lowering the lifting
unit.
RISK of death due to malfunction!
Lifting gear and equipment must be in
perfect technical condition. Work may only
commence if the lifting equipment has been
checked and found to be in perfect working
order. If it is not inspected, fatal injuries may
result.
7.1. Switching off the unit
BEWARE of burns!
The motor housing can reach temperatures
well in excess of 40 °C. There is a risk of
burns! After switching off, first let the motor
cool down to ambient temperature.
1. Close the gate valve in the inlet pipe.
2. Drain the collection reservoir. To do this, switch
the unit on in manual operation using the manual
button for no more than 20 seconds.
3. Switch the lifting unit to standby mode via the
switchgear.
4. Pull the plug out of the socket.
5. Secure the unit against being unexpectedly
switched back on!
6. Close the gate valve in the pressure pipe.
7. Now it is possible to start the work of removal,
maintenance and putting into storage.
7.2. Removal
DANGER due to toxic substances!
During removal, there is potential for contact
with fluids that represent a health hazard. The
following points must be observed without
fail:
• Wear appropriate full-body protection as well
as protective goggles and mouth protection.
• Immediately wipe up drips.
• All components must be cleaned and disin-
fected!
• Channel the flushing water into the sewer
system at suitable points!
• The protective clothing and cleaning cloths
must be disposed in accordance with waste
code TA 524 02 and EC Directive 91/689/EEC
or with local directives.
1. Switch off the unit as described in the “Switching
off the unit” section.
2. Close all gate valves.
3. Open the non-return valve using the ventilation
device in order to drain the pressure pipe into the
reservoir.
4. Disconnect the connection between the inlet
pipe and the inlet seal, and pull the inlet pipe out
of the seal.
5. Disconnect the connection between the non-re-
turn valve and the pressure port.
6. Disconnect the connection between the ventila-
tion pipe and the ventilation connection, and pull
the pipe up off the connecting piece.
7. Also remove the DN 40 inlets if there are any.
8. Then disconnect the diaphragm hand pump from
the lifting unit if it is installed.
9. Once all connections have been disconnected,
release the anchoring points of the lifting unit in
the floor
10. Now the lifting unit can be pulled carefully out of
the pipework.
11. Flush through the lifting unit with clean water and
disinfect it
12. Firmly close all connecting pipes, clean and disin-
fect them.
13. Clean the operating space and disinfect it if
necessary.
7.3. Return delivery/storage
Lifting units that are sent back to the factory
must be cleaned to remove impurities and, if they
have been used with fluids that are harmful to
health, they must also be decontaminated.
For shipping, the parts must be packed in tear-
proof plastic bags of sufficient size in such a
manner that they are tightly sealed and leak-
proof. Furthermore, the packaging must protect
the lifting unit from damage during transporta-
tion. If you have any questions, please contact
the manufacturer!
For return delivery and storage please also refer
to the “Transport and storage” section!
7.4. Disposal
7.4.1. Protective clothing
The protective clothing and cleaning cloths
must be disposed in accordance with waste code
TA 524 02 and EC Directive 91/689/EEC or with
local directives.
7.4.2. Product
Proper disposal of this product avoids damage to
the environment and risks to personal health.
• Use the services of public or private waste dis-
posal companies, or consult them for the disposal
of the product or parts thereof.
• For more information on proper disposal, please
contact your local council or waste disposal office
or the supplier from whom you obtained the
product.
8. Maintenance and repair
For reasons of safety, and thus to guarantee cor-
rect function of the lifting unit, it must always be
maintained by Wilo customer service.
The maintenance intervals for lifting units are
determined by EN 12056‑4:
• ¼ year in the case of commercial companies
• ½ year for units in multi-family houses
• 1 year for units in single-family houses