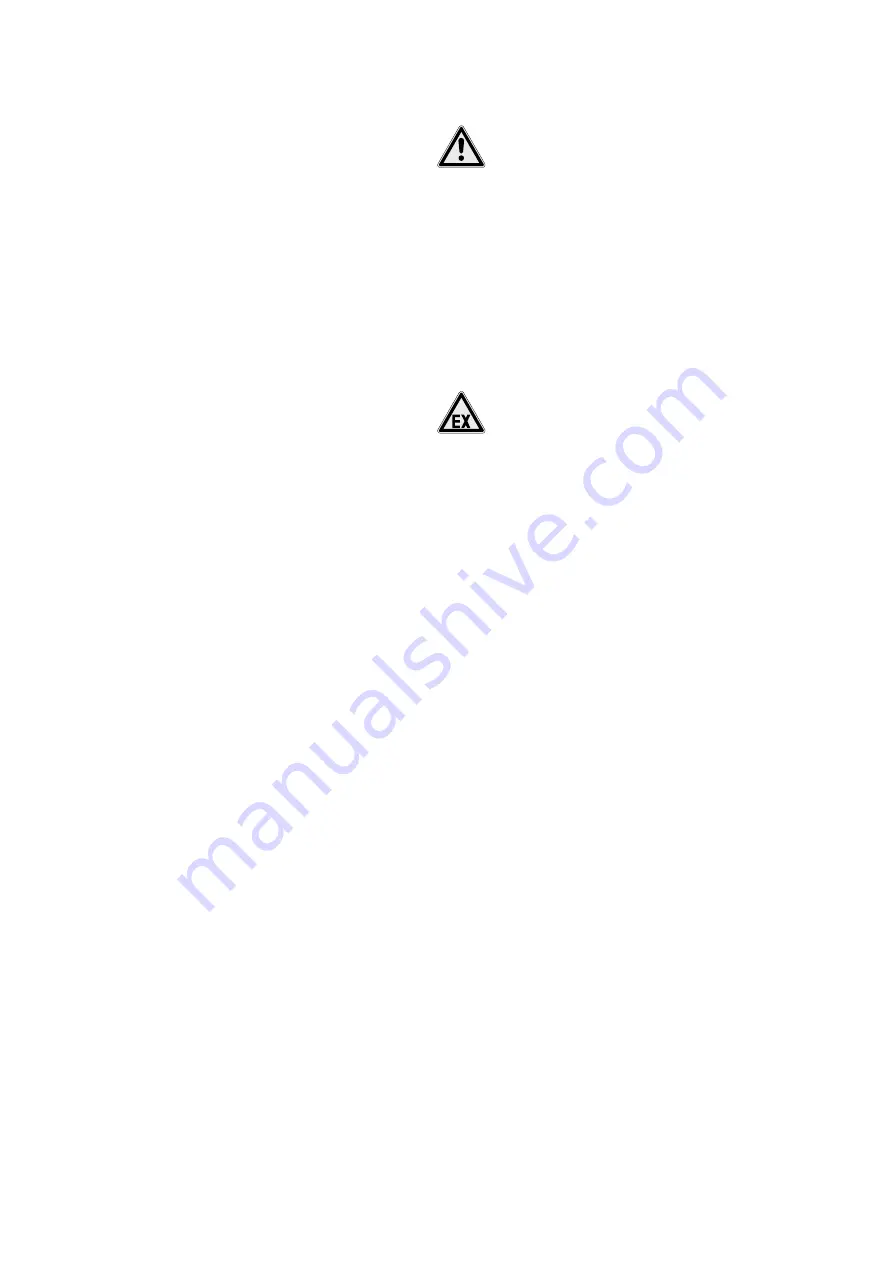
32
WILO SE 03/2016 V06 DIN A4
English INSTALLATION
4.4. Return delivery
Lifting units that are sent back to the factory
must be cleaned to remove impurities and, if they
have been used with fluids that are harmful to
health, they must also be decontaminated.
For shipping, the parts must be packed in tear-
proof plastic bags of sufficient size in such a
manner that they are tightly sealed and leak-
proof. Furthermore, the packaging must protect
the lifting unit from damage during transporta-
tion. If you have any questions, please contact
the manufacturer!
5. Installation
In order to prevent damage to the product or seri-
ous injury during installation, the following points
must be observed:
• Installation work – assembly and installation
of the lifting unit – may only be carried out by
qualified persons. The safety instructions must be
followed at all times.
• The lifting unit must be inspected for transport
damage before any installation work is carried
out.
5.1. General
For design and operation of technical sewage sys-
tems, observe the pertinent local regulations and
directives for sewage technology (such as those
of the German Association for Water, Wastewater
and Waste).
In particular, pressure surges which occur, e.g.
when closing the non-return valve, may be sever-
al times higher than the pump pressure, depend-
ing on the operating conditions. These pressure
surges can cause irreparable damage to the unit.
Therefore, pay attention to the pressure resist-
ance and the longitudinal force fit connection
of the pipe.
Furthermore, the existing piping must be checked
to ensure it is correctly connected to the unit. The
existing pipe system must be self-supporting and
is not allowed to be supported by the lifting unit.
In particular, the following applicable regulations
must be complied with for installation of lifting
units:
• DIN 1986-100
• EN 12050‑1 and EN 12056 (gravity drainage
stations within buildings)
Comply with the locally applicable regulations
in your country accordingly (e.g. national build-
ing regulations)!
5.2. Installation types
• Stationary dry well installation in buildings and
pump chambers
5.3. Installation
DANGER due to overpressure
Exceeding the application limits can result in
excessive pressure in the collection reser-
voir. This can cause the collection reservoir
to burst! There is a health risk due to contact
with sewage polluted by bacteria (faeces).
Ensure that the inlet is blocked if the unit
malfunctions.
The following application limits must be ob-
served strictly:
• Max. intake/h: 600 l
• Max. suction head: 5 m
• Max. permitted pressure in pressure pipe:
1.5 bar
DANGER - explosive atmosphere!
An explosive atmosphere can form within the
collection reservoir. If the collection reservoir
is opened (e.g. maintenance, repair, defect),
this atmosphere could spread within the
operating space. There is a risk of fatal injury
due to explosion! The operator is responsible
for defining a corresponding explosion zone.
Observe the following:
• The lifting unit and mounted switchgear are
not Ex-rated!
• Take appropriate countermeasures to avoid an
explosive atmosphere in the operating space!
The following information must be observed
when installing the lifting unit:
• This work must be performed by specialist per-
sonnel and electrical work must be performed by
a qualified electrician.
• The operating space must be clean, dry, well lit
and free from frost, and furthermore equipped for
the particular lifting unit.
• The operating space must be easily accessible.
Make sure that there are adequate access oppor-
tunities for the transport equipment including
lifting unit, and that any elevators required are
sufficiently large and have an adequate bearing
capacity.
• Adequate ventilation of the operating space must
be assured.
• The lifting unit must be easily accessible for oper-
ation and maintenance. A space of at least 60 cm
must be left clear around the unit (WxHxD).
• The installation surface must be solid (suitable for
accommodating dowels), horizontal and flat.
• The placement of any existing or still-to-be
installed piping (for inlet, pressure and venting) is
to be checked with regard to connection options
to the unit.
• A pump sump must be arranged within the op-
erating space for draining it. This must have the
minimum dimensions of 500 x 500 x 500 mm.