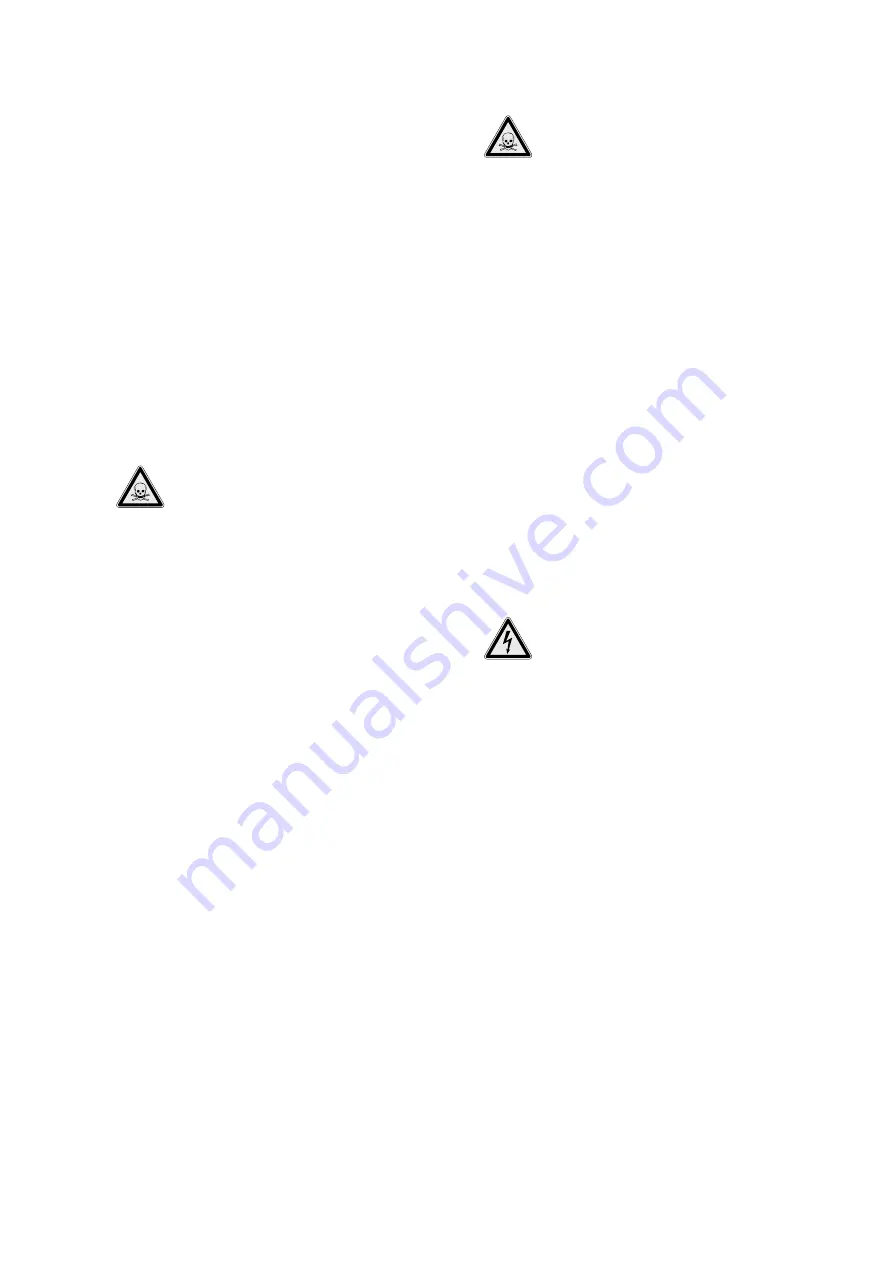
Installation and operating instructions Wilo-DrainLift S 31
TRANSPORTATION AND STORAGE English
• Flange gate valve DN 80 made of cast material
• On intake side:
• Flange connector DN 100 for connection of a
flange gate valve
• Flange gate valve DN 100 made of cast material
• DN 100 gate valve made of PVC with fixed pipe
ends
• Inlet seal DN 100
• General:
• Diaphragm hand pump with R1½ connection
(without hose)
• 3-way cock for switching over to the manual
suctioning from the pump sump/tank
• Horn 230 V, 50 Hz
• Flash light 230 V, 50 Hz
• Signal lamp 230 V, 50 Hz
• Smart Home radio transmitter for networking
with the Wilo wibutler
4. Transportation and storage
DANGER due to toxic substances!
Lifting units that pump fluids that are harmful
to health must be decontaminated before any
other work is performed! Otherwise there is
a risk of death. Wear the necessary physical
protection equipment!
4.1. Delivery
On delivery, check immediately that the ship-
ment is complete and undamaged. If any parts
are damaged or missing, the transport company
or the manufacturer must be notified on the day
of delivery. Claims made after this date cannot be
recognised. Damage to parts must be noted on
the freight documentation.
4.2. Transport
Only the designated and approved fastening
devices, transportation and lifting equipment
may be used for transportation. It must have
a sufficient bearing capacity and safe working
load in order for the lifting unit to be transported
safely. When using chains, they must be secured
against slipping.
The personnel must be qualified for the tasks and
must follow all applicable national safety regula-
tions during the work.
The lifting units are supplied by the manufacturer
or supplier in suitable packaging. This normally
precludes the possibility of damage occurring
during transportation and storage. The packaging
should be stored in a safe place for reuse if the
product is frequently used at different locations.
4.3. Storage
Newly delivered lifting units are prepared in such
a way that they can be stored for at least 1 year.
For temporary storage, the lifting unit must be
thoroughly rinsed with clean water before storage
in order to prevent encrustations and deposits
building up in the collection reservoir, on the level
control and the pump hydraulics.
DANGER due to toxic substances!
Flushing through the lifting unit contami-
nates the flushing water with faeces. Risk of
fatal injury due to contact with fluid that is
harmful to health! Always wear the necessary
physical protection equipment and channel
the flushing water into the sewer system at
suitable points!
The following should be taken into consideration
for storage:
• Place the lifting unit securely on a firm bearing
surface, and secure it to prevent tipping over and
sliding. Lifting units are stored horizontally.
• Lifting units can be stored at temperatures down
to ‑ 15 °C if completely emptied. The store room
must be dry. We recommend a frost-protected
room for storage with a temperature between
5 °C and 25 °C.
• The lifting unit is not allowed to be stored in
rooms in which welding work is carried out, be-
cause the resulting gases or radiation can damage
the elastomer components.
• All connections must be sealed securely to pre-
vent contamination getting in.
• The power supply cables should be protected
against kinking, damage, and moisture. Further-
more, mounted plugs and switchgear must also
be protected against moisture ingress.
DANGER due to electrical voltage!
Defective electrical components (e.g. power
supply cables, switchgear, plugs) represent
a risk of fatal injury due to electric shock!
Defective components must be replaced by a
qualified electrician immediately.
BEWARE of moisture!
Ingress of moisture into the electrical compo-
nents (cables, plugs, switchgear) will result in
damage to these components and the lifting
unit. Never immerse the electrical compo-
nents in a liquid, and protect them against the
ingress of moisture.
• The lifting unit must be protected from direct
sunlight and frost. This can lead to significant
damage to the collection reservoir or the electri-
cal components!
• Following lengthy storage, the maintenance work
according to EN 12056‑4 must be carried out
prior to commissioning.
If you comply with these rules, your pump can
be stored over a lengthy period. However, note
that the elastomer components and coatings are
subject to natural embrittlement. If the prod-
uct is to be stored for longer than 6 months, we
recommend checking these parts and replacing
them as necessary. Consult the manufacturer for
further details.