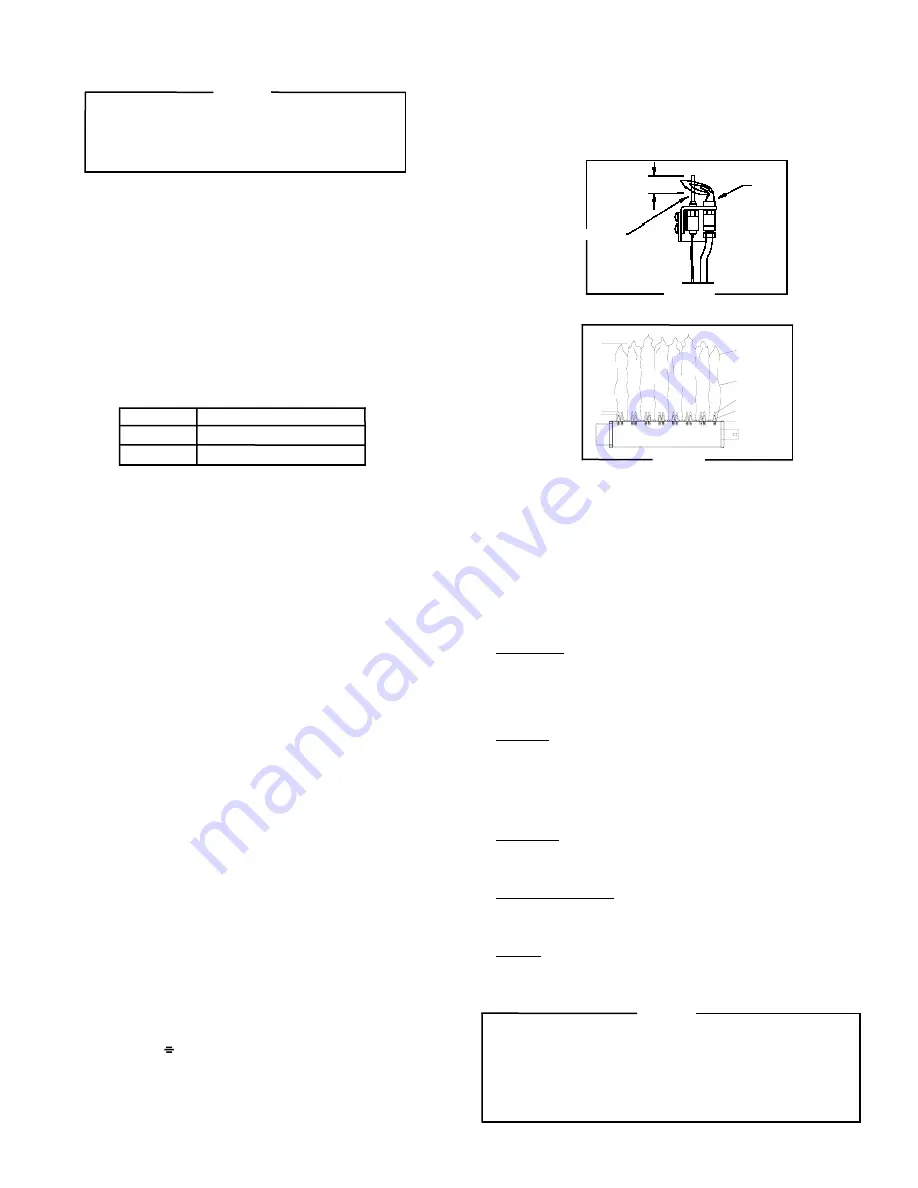
Start-Up Procedure
Check the heater operation as outlined in the following instructions. If
any sparking, odors or unusual noises are encountered, shut off electric
power immediately. Recheck for wiring errors, or obstructions in or
near fan motor (if equipped).
Check Gas Input and Pressures
For heaters located at elevations between sea level and 4,500 feet, the
measured input must not be greater than the input shown on the rating
plate of the furnace. For elevations above 4,500 feet, the measured
input must not exceed the input of the rating plate reduced by 4 percent
for each 1,000 feet that the heater is above sea level.
Gas supply pressure and manifold pressure with the burner operating
must also be as specified on the rating plate.
Rated input will be obtained on the heating valve of 2510 Btu/hr for
propane at 10.5-inches manifold pressure and factory-sized orifices. If
L.P. Gas having a different heating value is supplied, orifices must be
changed by a qualified service technician before the heater is operated.
Check the Manifold Gas Pressure
A tapped opening is provided in the gas valve to facilitate measuring the
manifold gas pressure. A “U Tube” manometer having a scale range
from 0 to 12 inches of water should be used for this measurement. The
manifold pressure must be measured with the burner and pilot operating.
Any major changes in the flow must be made by changing the size of the
burner orifice.
Check Thermostat
Check thermostat operation. When set above room temperature or
temperature shown on the thermostat, the main burner should light.
Make certain the thermostat turns off the heater when room temperature
reaches the selected setting and starts the heater when room
temperature falls a few degrees.
Check the Gas Input (Natural Gas Only)
Under-firing could cause inadequate heat, excessive condensation or
ignition problems. Over-firing could cause shooting flame impingement
or overheating of the combustion chamber.
Before starting natural gas input check, obtain heating value of gas (BTU
per cubic foot) at standard conditions from your local supplier.
To measure the input using the gas meter, proceed as follows:
Step 1: Turn off gas supply to all other appliances except the heater.
Step 2: With the heater operating, time the smallest dial on the meter for
one complete revolution. If this is a 2 cubic foot dial, use the time in
seconds as is. (3,600 = Sec. Per Hr.) This gives the seconds per cubic
foot of gas being delivered to the heater.
Step 3: Assuming natural gas with a heating value of 1,000 Btu per
cubic foot and 34 seconds per cubic foot as determined by Step 2 then,
input: 1,000 x 3,600 34 = 106,000 Btu Per hour. This measured input
must not be greater than the input indicated on the rating plate of the
heater.
Step 4: Relight all other appliances turned off in Step 1 above and verify
all pilot burners are operating.
Warning
Warning
Danger of property damage, bodily injury or death.
Liquified petroleum (L.P.) gas is heavier than air and it will
settle in any low area, including open depressions and it
will remain there unless area is ventilated. Never attempt
start-up of unit before throughly ventilating area.
Type of Gas
Natural
L.P.
Manifold Pressure, In. W.C.
4”
10.5”
Natural gas heating value (Btu per cubic foot) can vary
significantly; therefore, it is the installer’s responsibility to see that
the Btu input to the heater is adjusted properly. Failure to do so
could cause combustion chamber failure, asphyxiation, fire or
explosion, resulting in property damage, bodily injury or death.
Refer to the National Fuel Code (NFPA-54) to be sure the heater
is burning fuel at the proper rate.
Figure 7
Figure 8
1/2 TO 5/8
INCH
PILOT
FRONT
VIEW
GENERATOR
Burner Flame Characteristics
Start the furnace and let it operate at least 10 minutes. Open the
access door to view the burner flame. Limit your movements near
the furnace a few more minutes before making your final
observations. The flame may look yellow due to dust particles in
the room air. The flame should change to a nice blue color with firm
inner and secondary cones. An occasional flash of orange might be
seen as dust particles burn in the flame. This is normal. No burner
adjustment is provided, or is necessary. (Figure 8).
Normal Appearance
Natural Gas:
1. Inner cone - blue color - 3/8 to 5/8 inch above ports
2. Secondary inner cone - light blue - 1 to 2 inches above ports
3. Total flame - from blue to nearly invisible - approximately 6 inches
above ports.
L.P. Gas:
1. Inner cone - blue color - 1/2 to 3/4 inch above ports.
2. Secondary inner cone - light blue - 1 to 2 inches above ports.
3. Total flame - from blue to nearly invisible - approximately 6
inches above ports.
Abnormal Appearance
Lazy Flame
Long soft yellow cones moving around in the combustion chamber
lifting from ports (insufficient air).
Extremely Fast Flame
Will not hold to ports - entire cone sections blow off from noisy ports
(too much pressure).
Warning
If flame appears abnormal, contact the gas company or a qualified
service technician immediately.
Check Pilot Burner
The pilot flame must envelop 1/2- to 5/8-inches of the generator.
Pilot flame is preset at the factory, so ordinarily does not require field
adjustment. (Figure 7). On new installations, the gas lines will be
filled with air and may take several minutes to establish a pilot flame.
3
2
1
NEARLY
PALE BLUE
LIGHT BLUE
BLUE
PORT LEVEL
ROUND STAINLESS STEEL
BURNER BODY
INVISIBLE
10
Summary of Contents for 2001621
Page 17: ...16 Enclosed Front...
Page 19: ...Fireplace Look with Logs 18...