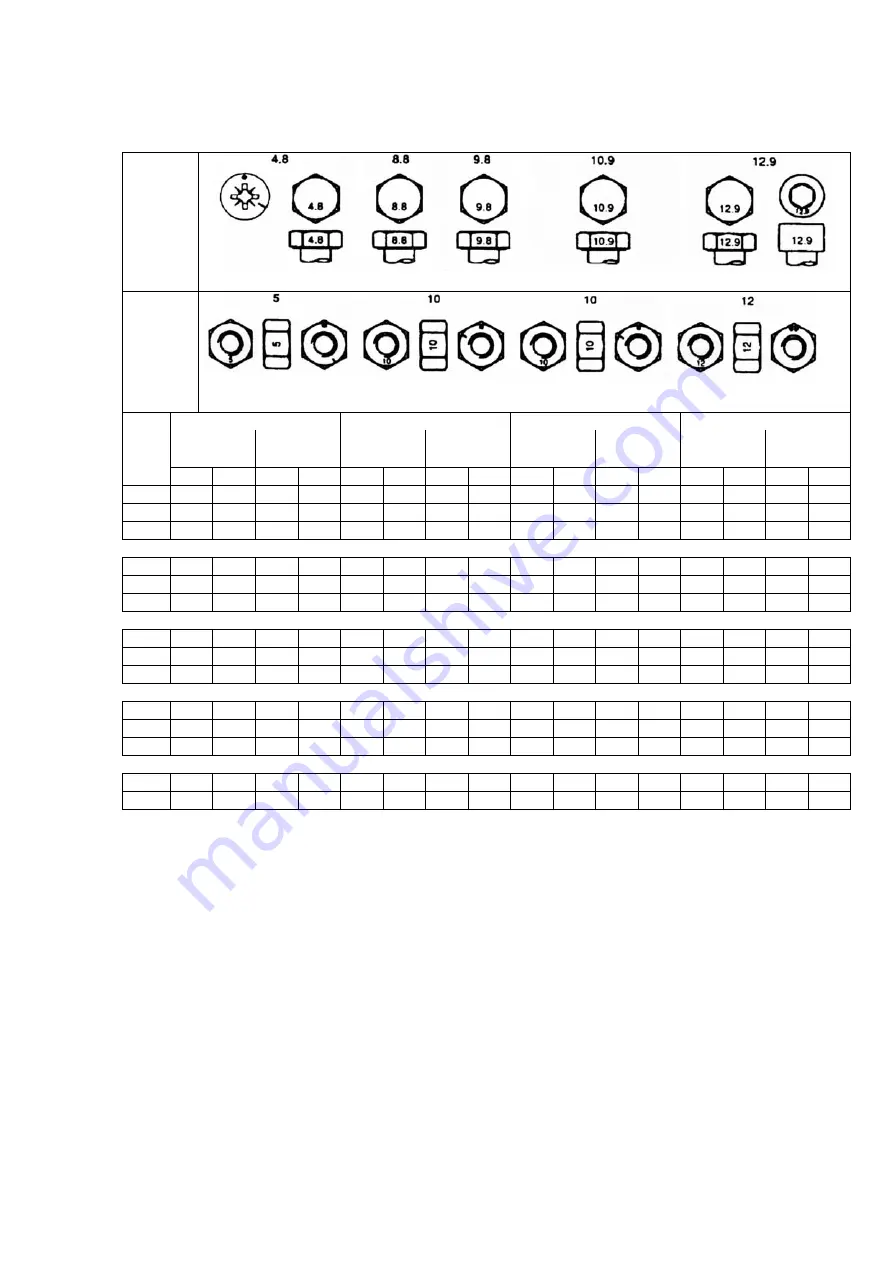
All information, illustrations and specifications in these Operating Instructions are based on the latest information available at the time of
publication. We reserve the right to make design changes at any time without prior notification
42
10.0. Technical Specifications
10.3. Metric bolt and cap screw torque values
Property
Class and
Head
Markings
Property
Class and
Nut
Markings
class 4.8
class 8.8 or 9.8
class 10.9
class 12.9
Lubricated *
Dry **
Lubricated *
Dry **
Lubricated *
Dry **
Lubricated *
Dry **
Size
N-m lb-ft N-m lb-ft N-m lb-ft N-m lb-ft N-m lb-ft N-m lb-ft N-m lb-ft N-m lb-ft
M6 4,8 3,5 6 4,5 9 6,5 11 8,5 13 9,5 17 12 15 11,5
19 14,5
M8 12 8,5 15 11 22 16 28 20 32 24 40 30 37 28 47 35
M10
23 17 29 21 43 32 55 40 63 47 80 60 75 55 95 70
M12
40 29 50 37 75 55 95 70 110
80 140
105
130
95 165
120
M14 63 47 80 60 120 88 150 110 175 130 225 165 205 150 260 190
M16 100 73 125 92 190 140 240 175 275 200 350 255 320 240 400 300
M18 135 100 175 125 260 195 330 250 375 275 475 350 440 325 560 410
M20 190 140 240 180 375 275 475 350 530 400 675 500 625 460 800 580
M22 260 190 330 250 510 375 650 475 725 540 925 675 850 625 1075 800
M24 330 250 425 310 650 475 825 600 925 675 1150
850 1075
800 1350 1000
M27 490 360 625 450 950 700 1200 875 1350 1000 1700
1250
1600
1150 2000 1500
M30 675 490 850 625 1300 950 1650 1200 1850 1350 2300
1700
2150
1600 2700 2000
M33 900 675 1150 850 1750 1300 2200 1650 2500 1850 3150 2350 2900 2150 3700 2750
M36 1150 850 1450 1075 2250 1650 2850 2100 3200 2350 4050 3000 3750 2750 4750 3500
DO NOT use these values if a
different torque value or tightening
procedure is given for a specific
application. Torque values listed are
for general use only. Check tightness
of fasteners periodically.
Shear bolts are designet to fail
under predetermined loads. Always
replace shear bolt with identical
property class
Fasteners should be replaced with the
same or higher property class. If
higher property class fasteners used,
these should only be tightened to the
strength of the original.
Make sure fasteners threads are
clean and that you properly start
thread engagement. This will
prevent therm from failing when
tightening.
Tighten plastic insert or crimped
steel-type lock nuts to
approximately 50 percent of the dry
torque shown in the chart, applied
to the nut, not to the bolt head.
Tighten toothed or serrated-type
lock nuts to the full torque value.
** “Lubricated“ means coated with a lubricant such as engine
oil, or fasteners with phossphate and oil coatings.
** “Dry“ means plain or zinc platend without any
lubrication.