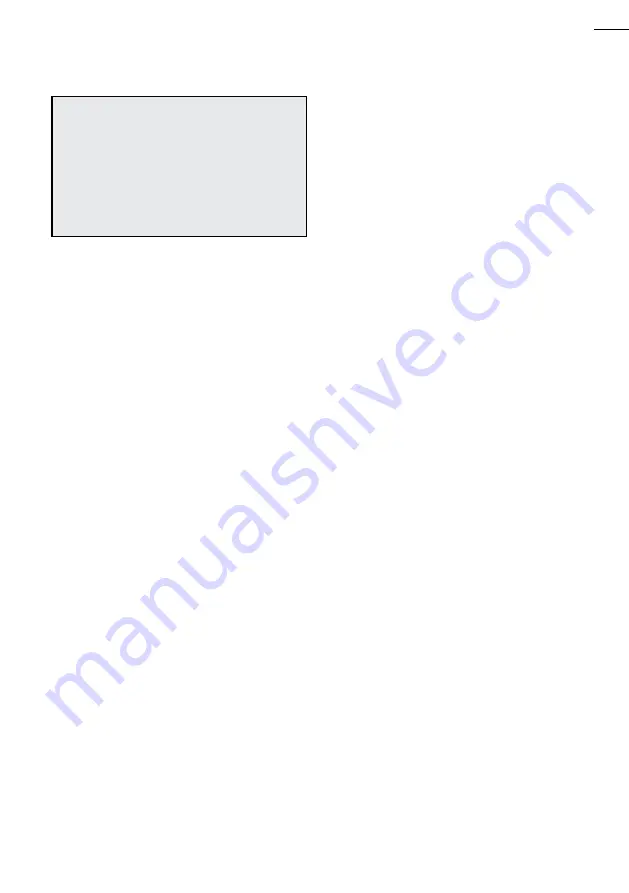
Weldmatic 200i + Weldmatic 250i
Model No CP137, CP138
23
Before removing the equipment
cover, ENSURE that the equipment
is disconnected from the mains
power supply. When the equipment
is energised LETHAL VOLTAGES are
present on the electrical components
enclosed.
Dust
Care should be taken to prevent excessive
build-up of dust and dirt within the welding
power source. It is recommended that at
regular intervals, according to the prevailing
conditions, the equipment covers be removed
and any accumulated dust be removed by the
use of dry, low pressure compressed air, or a
vacuum cleaner.
Wirefeed
In order to obtain the most satisfactory
welding results from the GMAW process,
the wirefeed must be smooth and constant.
Most causes of erratic wirefeed can be cured
by basic maintenance. Check that the:
1 Feed rolls are the correct size and type for
the wire in use. Check also that the drive
groove is aligned with the wire, and that
the groove is not worn;
2 Gun cable liner is clear of dust and swarf
build-up. When replacement becomes
necessary, fit only the correct liner (see
page 35). The build-up of dust can be
minimised by regular purging of the liner
with dry compressed air. This may be
conveniently done each time the wire
spool is replaced;
3 Welding tip is free of obstructions such
as spatter build-up. Ream out the tip
bore with a suitable size oxy-tip cleaner.
Replace the welding tip as it becomes
worn;
4 Feed roll pressure is not excessive. The
pressure should be just sufficient to feed
the wire evenly. Excessive pressure will
deform the electrode wire and make
feeding more difficult;
5 Consumable wire spool holder rotates
smoothly and that the braking action is
not excessive. The spool should only have
sufficient braking to prevent over run
when the motor stops. This also may be
conveniently checked each time the wire
is replenished;
7 Welding wire is straight and free of
buckles or ‘waviness’. To check, remove
2 or 3 metres of wire from the spool.
Clamp one end in a vice or similar, then
holding the other end pull the wire out
straight. Look down the length of the
wire, any buckles will be obvious. Buckled
wire is extremely difficult to feed reliably
and should be replaced;
8 Welding wire is free of surface rust.
Replace if rust is evident.
8 General Maintenance