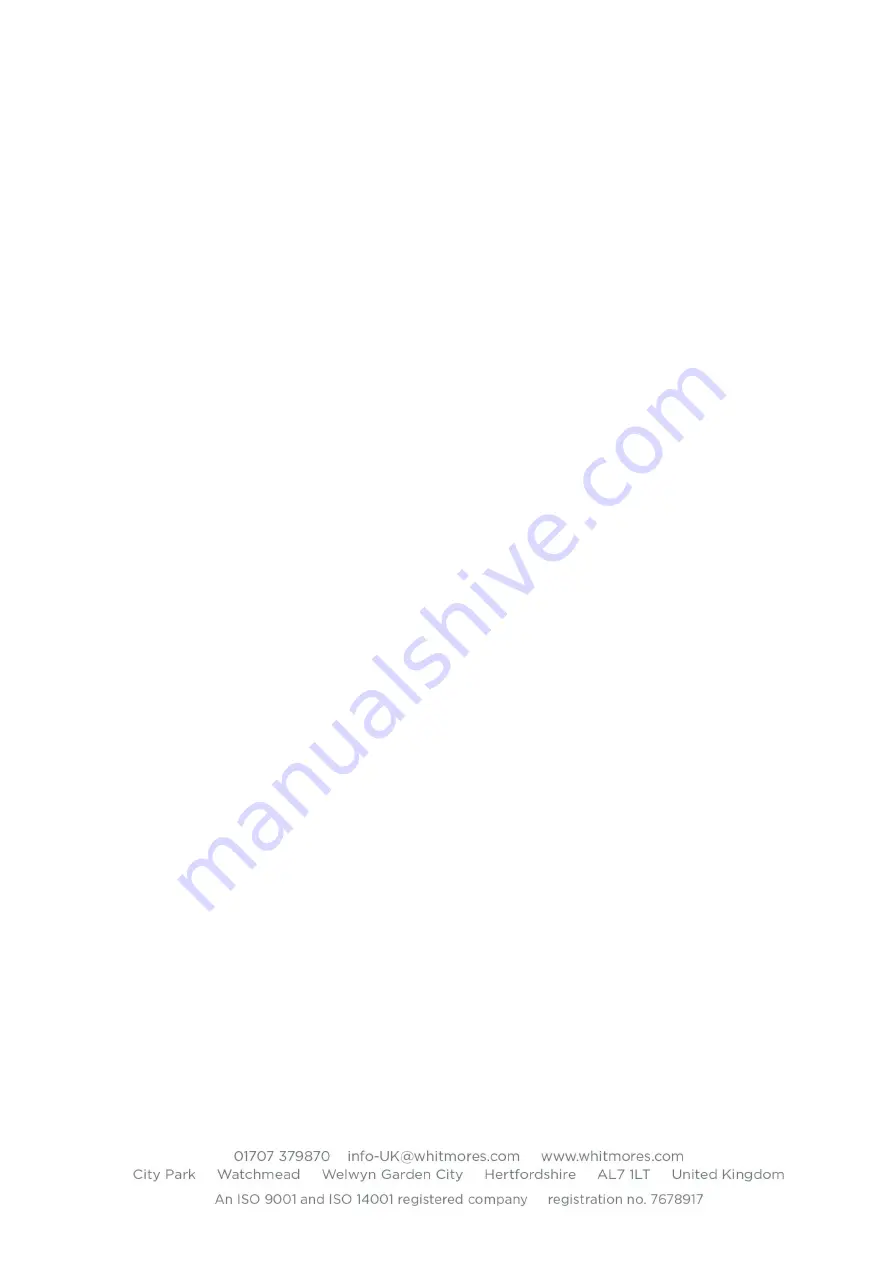
25
12.8.3
The site must be cleared of excess grease.
12.8.4
If oil absorbent granules are being used, the existing, soiled granules should be removed
and replaced with fresh granules. This must be done with extreme caution, if the granules
are allowed to get into the lubricator system via the blades, the system may become
blocked.
12.8.5
The surrounding rail chairs and clips, all rails in the immediate vicinity and the insulator
pots need to be cleaned. 3rd and 4th rail are needed to be cleaned to ensure they are free
of grease and dirt, this is to avoid causing a fire risk and hazardous under footing.
Do not attempt to clean live traction current rails with the current switched on.
12.9
Checking for Leaks
12.9.1
The lubricator should be checked for leaks. With some leaks it will be necessary to take
the leak into consideration in regards to the grease output that you have noted.
12.9.2
Leaks on the primary side (i.e. within the cabinet) of the lubricator will cause an increase in
grease output that is not due to the settings of the lubricator.
12.9.3
Tighten any hose clips or nuts / bolts / screws that maybe the cause of the leak and / or
replace the faulty part that is causing the leak.
12.10
Measuring / Testing the Wheel Sensor
12.10.1
The sensor height to be measured is the vertical distance between the top of the green
sensor body, and the top of the crown of the rail.
12.10.2
The sensor height should be set at 42 to 45mm. below the top of the rail
12.10.3
If the lubricator has not used the amount of grease that is required for this lubricator since
the last time that it was maintained.
Check that the sensor heights are the same as when the lubricator was last maintained.
You may find that the sensor height has changed due to loose bolts on the mounting
bracket causing the assembly unit to move, check the bolts and tighten if necessary. If
necessary reset the heights once all other checks have been carried out.
If the sensor height has been reset on this visit record the new heights.
12.10.4
Check the sensor is operating:
With the Control Panel powered a ‘green’ LED will be visible at one end of the Wheel
Sensor (opposite end to cable entry). If the lamp is not illuminated there is no power to
the sensor and the cause should be investigated.
With the Control Panel powered move a solid metallic ferrous object (i.e. 2lb Ball Pein
hammer) over the sensor. The second indicating LED should illuminate ‘yellow’ to show
the sensor has ‘seen’ the object.
Repeat the test with a person viewing the red sensor-indicating lamp on the Control
Panel. The lamp should illuminate when the sensor is activated.
Summary of Contents for LUBRICURVE ELECTRO 5
Page 30: ...30 ...