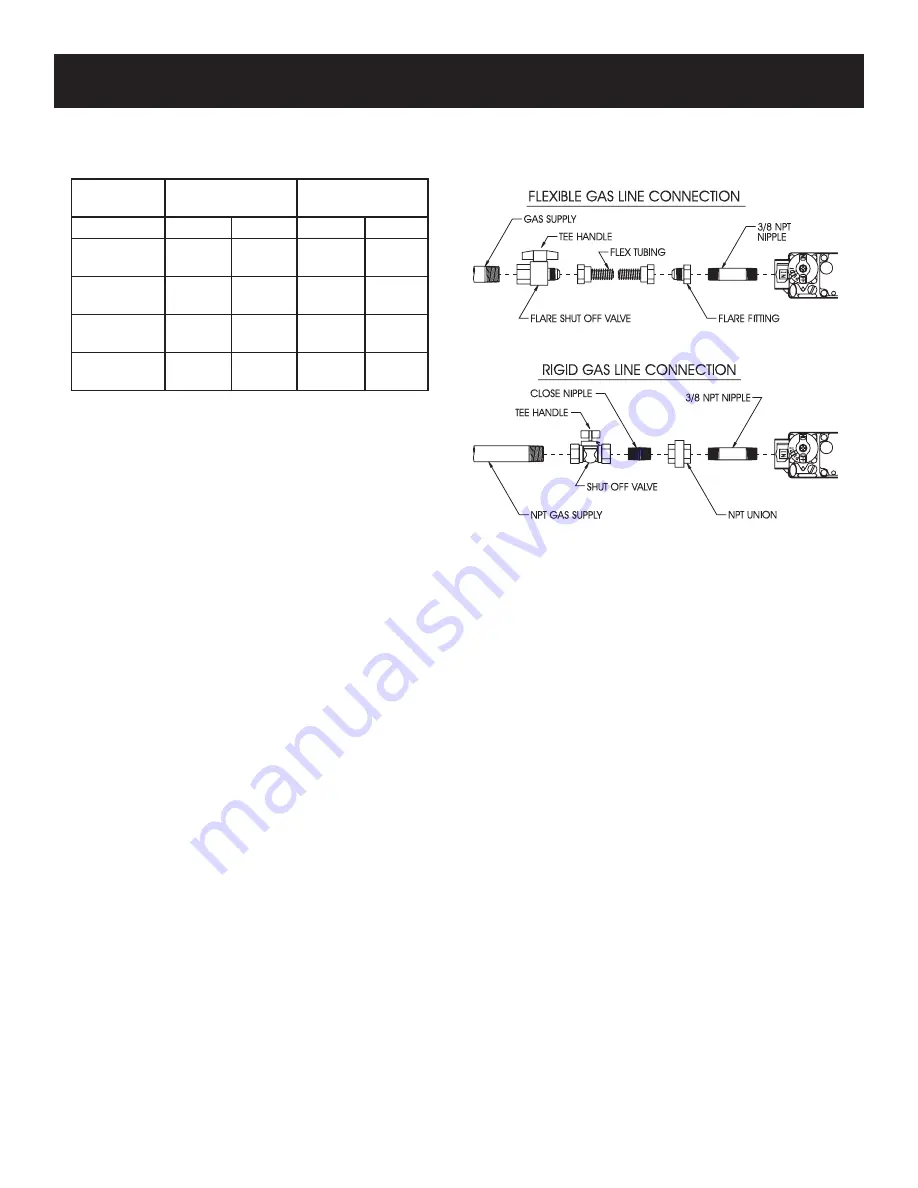
25783-5-1011
Page 8
Check all local codes for requirements, especially for the size and
type of gas supply line required.
NOTICE
:
Never use plastic pipe. Check to confirm whether your
local codes allow copper tubing or galvanized.
NOTICE
:
Since some municipalities have additional local codes, it is
always best to consult your local authority and installation code.
Installing a New Main Gas Cock
Each appliance should have its own manual gas cock.
A manual main gas cock should be located in the vicinity of the unit.
Where none exists, or where its size or location is not adequate,
contact your local authorized installer for installation or relocation.
Compounds used on threaded joints of gas piping shall be resistant
to the action of liquefied petroleum gases. The gas lines must be
checked for leaks by the installer. This should be done with a soap
solution watching for bubbles on all exposed connections, and if
unexposed, a pressure test should be made.
Never use an exposed flame to check for leaks. Appliance must
be disconnected from piping at inlet of control valve and pipe
capped or plugged for pressure test. Never pressure test with
appliance connected; control valve will sustain damage!
A gas valve and ground joint union should be installed in the gas
line upstream of the gas control to aid in servicing. It is required by
the National Fuel Gas Code that a drip line be installed near the gas
inlet. This should consist of a vertical length of pipe tee connected
into the gas line that is capped on the bottom in which condensation
and foreign particles may collect.
The use of the following gas connectors is recommended:
— ANS Z21.24 Appliance Connectors of Corrugated Metal Tubing
and Fittings
— ANS Z21.45 Assembled Flexible Appliance Connectors of Other
Than All-Metal Construction
The above connectors may be used if acceptable by the authority
having jurisdiction. The state of Massachusetts requires that a flex
-
ible appliance connector cannot exceed three feet in length.
Pressure Testing of the Gas Supply System
1. To check the inlet pressure to the gas valve, a 1/8" (3mm) N.P.T.
plugged tapping, accessible for test gauge connection, must
be placed immediately upstream of the gas supply connection
to the appliance.
2. The appliance and its individual shutoff valve must be
disconnected from the gas supply piping system during any
pressure testing of that system at test pressures in excess of
1/2 psig (3.5 kPa).
3. The appliance must be isolated from the gas supply piping
system by closing its individual manual shutoff valve during
any pressure testing of the gas supply piping system at test
pressures equal to or less than 1/2 psig (3.5 kPa).
Figure 3
Attention!
If one of the above procedures results in pressures in
excess of 1/2 psig (14" w.c.) (3.5 kPa) on the appliance gas valve,
it will result in a hazardous condition.
Checking Manifold Pressure
Millivolt Models
Natural gas will have a manifold pressure of
approximately 3.5" w.c. (.871kPa) for maximum input or 1.7" w.c.
(.423kPa) for minimum input at the pressure regulator outlet with
the inlet pressure to the pressure regulator from a minimum of 5.0"
w.c. (1.120kPa) for the purpose of input adjustment to a maximum
of 10.5" w.c. (2.614kPa).
Hydraulic Thermostat Models
Natural gas will have a manifold
pressure of approximately 6.0" w.c. (1.49kPa) at the pressure
regulator outlet with the inlet pressure to the pressure regulator
from a minimum of 7.0" w.c. (1.74kPa) for the purpose of input
adjustment to a maximum of 10.5" w.c. (2.615kPa).
Millivolt Models
Propane gas will have a manifold pressure
approximately 10.0"w.c. (2.49kPa) for maximum input or 6.3"w.c.
(1.568kPa) for minimum input at the pressure regulator outlet with the
inlet pressure to the pressure regulator from a minimum of 11.0"w.c.
(2.739kPa) for the purpose of input adjustment to a maximum of
13.0"w.c. (3.237kPa).
Hydraulic Thermostat Models
Propane gas will have a manifold
pressure approximately 10.0"w.c. (2.49kPa) at the pressure regulator
outlet with the inlet pressure to the pressure regulator from a minimum
of 11.0"w.c. (2.739kPa) for the purpose of input adjustment to a
maximum of 13.0"w.c. (3.237kPa).
GAS SUPPLY
Recommended Gas Pipe Diameter
Pipe Length
Schedule 40 Pipe
Inside Diameter
Tubing, Type L
Outside Diameter
Nat.
L.P.
Nat.
L.P.
0-10 feet
0-3 meters
1/2”
12.7mm
3/8”
9.5mm
1/2”
12.7mm
3/8”
9.5mm
10-40 feet
4-12 meters
1/2”
12.7mm
1/2”
12.7mm
5/8”
15.9mm
1/2”
12.7mm
40-100 feet
13-30 meters
1/2”
12.7mm
1/2”
12.7mm
3/4”
19mm
1/2”
12.7mm
100-150 feet
31-46 meters
3/4”
19mm
1/2”
12.7mm
7/8”
22.2mm
3/4”
19mm