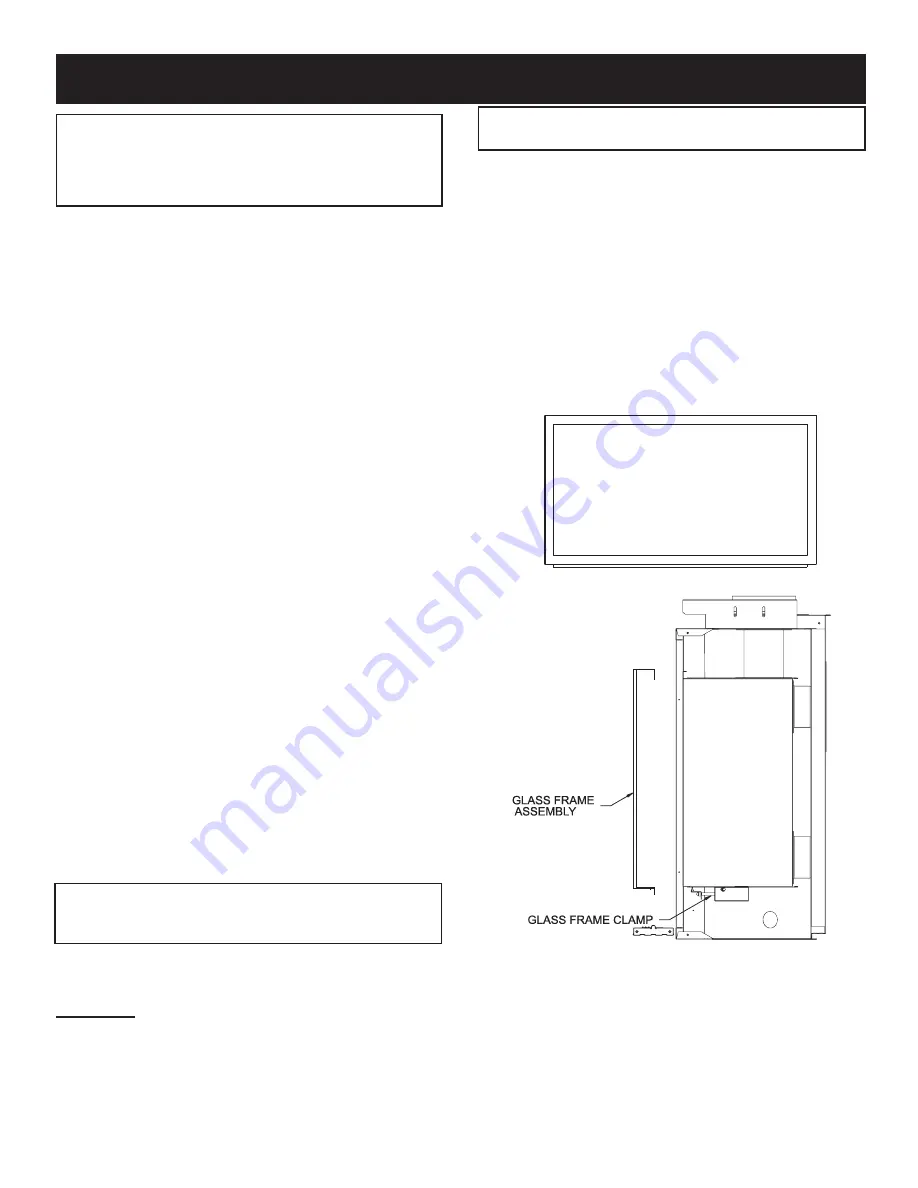
Page 44
17375-6-0705
PLEASE NOTE
It is normal for appliances fabricated of steel to give off
some expansion and/or contraction noise during the start
up or cool down cycle. Similar noises are found with your
furnace heat exchanger or car engine.
It is not unusual for your gas fireplace to give off some odor the
first time it is burned. This is due to the curing of the paint and
any undetected oil from the manufacturing process.
Please ensure that your room is well ventilated - open all
windows.
It is recommended that you burn your fireplace for at least six
(6) hours the first time you use it. If optional fan kit has been
installed, place fan in the “OFF” position during this time.
IMPORTANT:
Turn off gas before servicing appliance. It is
recommended that a qualified service person perform these check-
ups at the beginning of each heating season.
• Clean Burner and Control Compartment
Keep the control compartment, logs, and burner areas surrounding
the logs clean by vacuuming or brushing at least twice a year.
Cleaning Procedure
1. Turn off pilot light at gas valve.
2. Remove glass front. (See Glass Removal)
3. Vacuum burner compartment.
4. Reinstall glass front.
5. Ignite pilot. (See Lighting Instructions)
6. Operate the pilot burner. If it appears abnormal call a service
person.
• Check Vent System
The appliance and venting system should be inspected before
initial use and at least annually by a qualified service person.
Inspect the external vent cap on a regular basis to make sure
that no debris is interfering with the air flow.
Glass Cleaning
It will be necessary to clean the glass periodically. During start-up
condensation, which is normal, forms on the inside of the glass and
causes lint, dust and other airborne particles to cling to the glass
surface. Also initial paint curing may deposit a slight film on the
glass. It is therefore recommended that the glass be cleaned two
or three times with a non-abrasive household cleaner and warm
water (we recommend gas fireplace glass cleaner). After that the
glass should be cleaned two or three times during each heating
season depending on the circumstances present.
General Glass Information
WARNING: Do not operate appliance with the glass front
removed, cracked or broken. Replacement of the glass should
be done by a licensed or qualified service person.
Only glass approved for use by the manufacturer in fireplace may
be used for replacement. The glass replacement should be done
by a licensed or qualified service person.
WARNING:
1. The use of substitute glass will void all product warranties.
2. Care must be taken to avoid breakage of the glass.
3. Under no circumstances should this appliance be operated
without the glass front or with a broken glass front. Replacement
of the glass (with gasket) as supplied by the manufacturer
should be done by a qualified service person.
4. Do not abuse the glass by striking or hitting the glass.
WARNING: Do not use abrasive cleaners on glass. Do not
attempt to clean glass when glass is hot.
Glass Removal and Replacement (Figure 55)
1. Remove top louver, grasp louver and pull forward.
2. Lower bottom louver.
3. Release two glass frame clamps at bottom of firebox.
4. Remove glass frame.
5. Place glass frame onto firebox.
6. Attach two glass frame clamps at bottom of firebox.
7. Align clips on top louver with slots on front posts. Replace
top louver into fireplace.
8. Close bottom louver.
Louver Removal and Installation
1. Remove top louver, grasp louver and pull forward.
2. Lower bottom louver.
3. Align clips on top louver with slots on front posts. Replace
top louver into fireplace.
4. Close bottom louver.
MAINTENANCE AND SERVICE
Figure 55