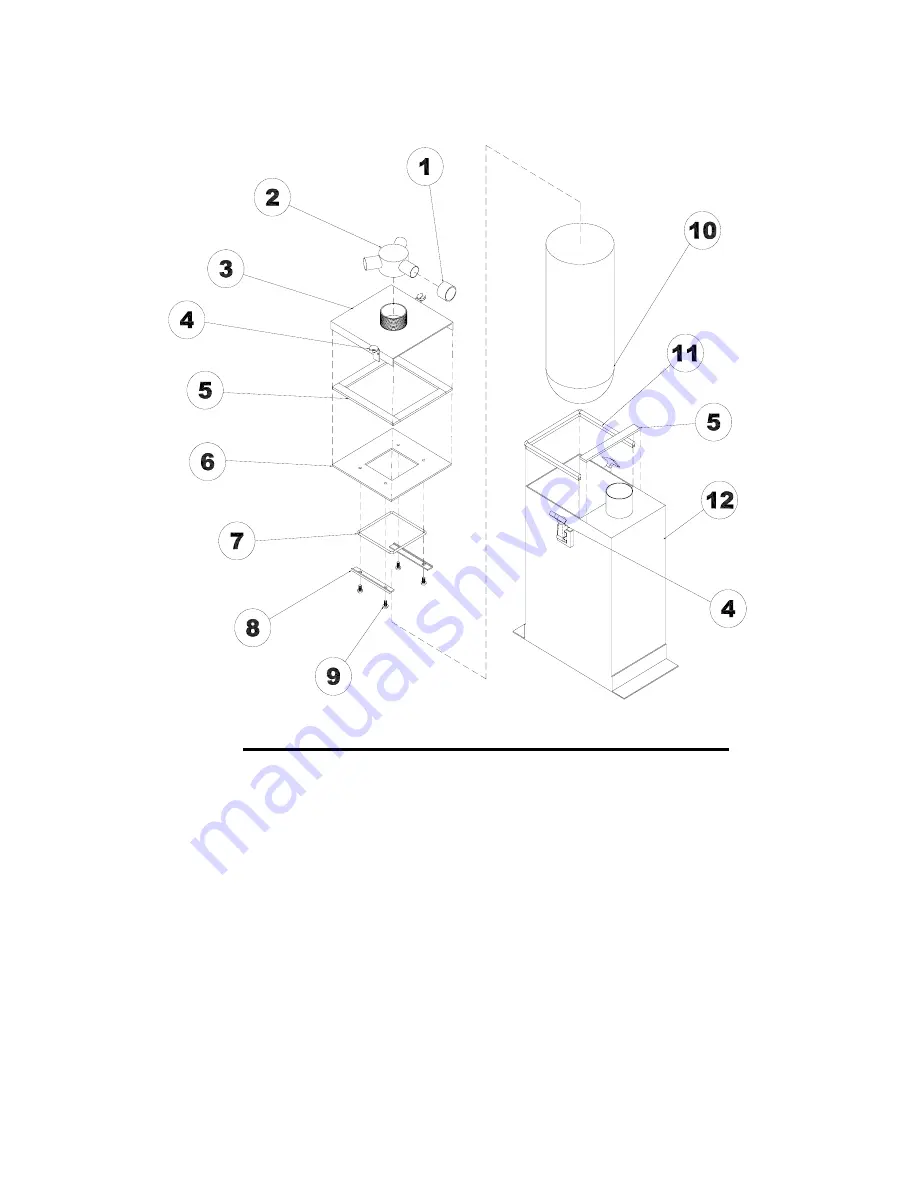
White Magic Carpet Cleaners Accessories Catalog
TARFS3-A - FILTER BOX
1 E109C VACUUM END CAP
2 K013-1 VACUUM TRI PORT
3 K013-2 FILTER BOX LID
4 K012 RUBBER TEE CLAMP
5 D002 1/4 X 1” SELF ADHESIVE FOAM TAPE
6 K013-3 FILTER MOUNTING PLATE
7 K016A FILTER RING - SS
8 K013-4 RING CLAMP
9 D121 5/16-18 X 5/8” LG BUTTON HEAD CAP SCREW
10 K016 FILTER BAG ELEMENT
11 D0025 EDGE TRIM GASKET
12 TARFS3-1 FILTER BOX MAIN BODY
ITEM# / P/N / DESCRIPTION
6-D1
Summary of Contents for PRO 1900
Page 2: ......
Page 6: ......
Page 11: ...Muffler Installation Hanger may need modification 8 ...
Page 15: ...12 ...
Page 20: ......
Page 24: ...20 ...
Page 34: ......
Page 56: ......
Page 58: ......
Page 61: ...White Magic Carpet Cleaners Accessories Catalog FP1900A LOWER FACE PANEL ASSEMBLY 6 A2 ...
Page 67: ...White Magic Carpet Cleaners Accessories Catalog BA1900 BLOWER ASSEMBLY 6 A8 ...
Page 69: ...White Magic Carpet Cleaners Accessories Catalog EA1900 FORD ENGINE ASSEMBLY 6 A10 ...
Page 73: ...White Magic Carpet Cleaners Accessories Catalog FA1900 PRO 1900 MAIN FRAME ASSEMBLY 6 A14 ...
Page 77: ...White Magic Carpet Cleaners Accessories Catalog 6 A18 ...
Page 87: ......
Page 88: ......
Page 89: ......
Page 90: ......