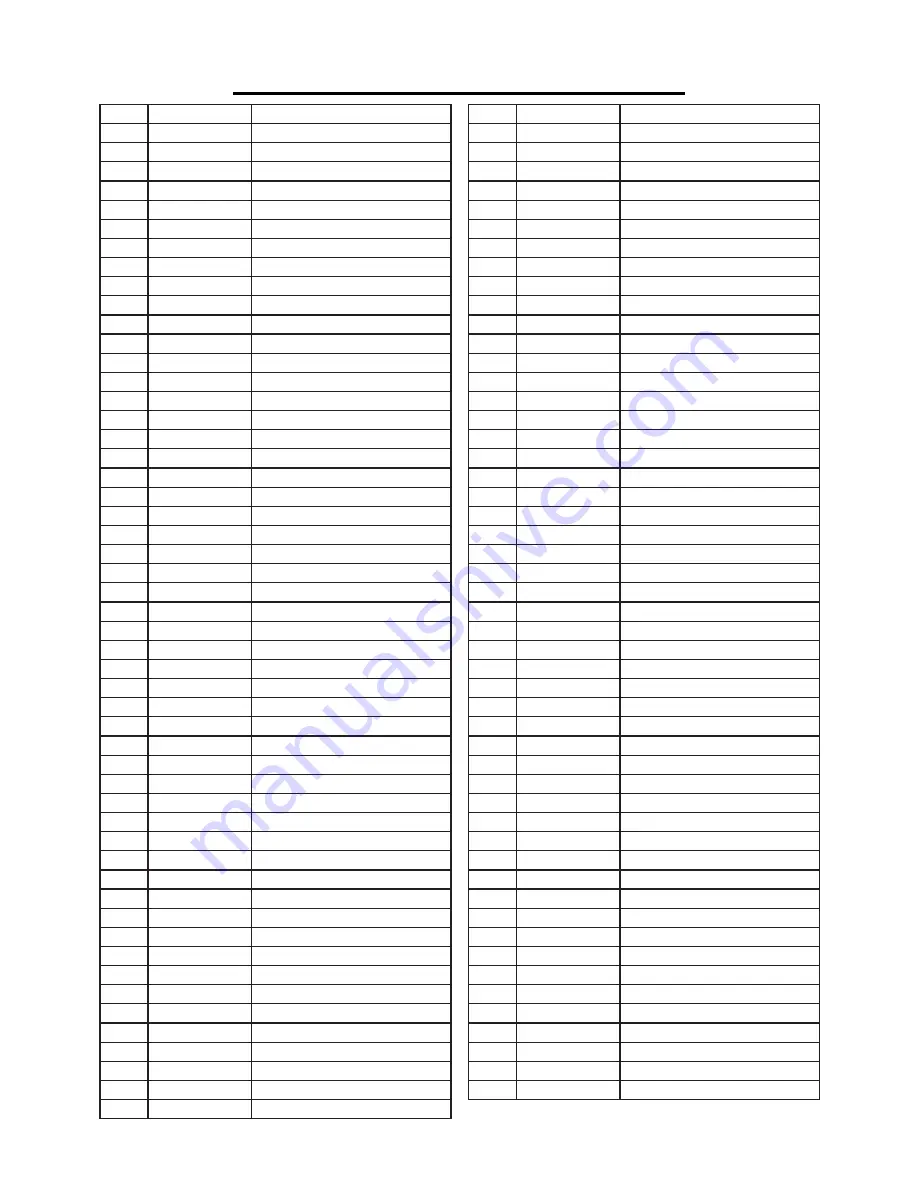
EXPLODED VIEW & PARTS LIST
No.
Part No.
Description
1
61731-001
Screw
2
61731-002
Washer
3
61731-003
Bushing
4
61731-004
Exhaust Cap
5
61731-005
Washer
6
61731-006
Screw
7
61731-007
Washer
8
61731-008
Cylinder Cap
9
61731-009
Cylinder Cap Seal
10
61731-010
Washer
11
61731-011
Valve Seat
12
61731-012
Valve Spring
13
61731-013
O-Ring
14
61731-014
O-Ring
15
61731-015
Valve
16
61731-016
Screw
17
61731-017
Cylinder Seal
18
61731-018
Collar
19
61731-019
O-Ring
20
61731-020
Piston Assembly
21
61731-021
Cylinder
22
61731-022
O-Ring
23
61731-023
O-Ring
24
61731-024
Restrictive Seal
25
61731-025
O-Ring
26
61731-026
Bumper A
27
61731-027
Bumper B
28
61731-028
Body
29
61731-029
O-Ring
30
61731-030
Nose
31
61731-031
Washer
32
61731-032
O-Ring
33
61731-033
Bar Guide
34
61731-034
Pin
35
61731-035
Angle Adjustment Pin
36
61731-036
Spring
37
61731-037
Screw
38
61731-038
Washer
39
61731-039
Safety Bracket A
40
61731-040
Coil Spring Base
41
61731-041
Screw
42
61731-042
Safety Bracket B
43
61731-043
No Mar Tip
43-1
61731-043-1
No Mar Tip Clasp
44
61731-044
Safety Guide
45
61731-045
Pin
46
61731-046
Washer
47
61731-047
Screw
48
61731-048
Spring
49
61731-049
Split Washer
50
61731-050
Rotating Knob Bushing
51
61731-051
Trigger
No.
Part No.
Description
52
61731-052
Ball
53
61731-053
Spring
54
61731-054
Firing Mode Selector Knob
55
61731-055
Bushing
56
61731-056
Turn Plate A
57
61731-057
Screw
58
61731-058
O-Ring
59
61731-059
Valve Seat
60
61731-060
O-Ring
61
61731-061
Trigger Valve Seat
62
61731-062
O-Ring
63
61731-063
O-Ring
64
61731-064
O-Ring
65
61731-065
Spring
66
61731-066
Trigger Valve Stem
67
61731-067
O-Ring
68
61731-068
O-Ring
69
61731-069
Trigger Valve Guide
70
61731-070
Nut
71
61731-071
Washer
72
61731-072
Screw
73
61731-073
Washer
74
61731-074
Bushing
75
61731-075
Turn Plate B
76
61731-076
Coil Spring
77
61731-077
Pin
78
61731-078
Screw
79
61731-079
Movable Feeder Shoe
80
61731-080
Screw
81
61731-081
Feeder Shoe
82
61731-082
Screw
83
61731-083
Joint Block
84
61731-084
Screw
85
61731-085
Magazine
86
61731-086
Screw
87
61731-087
Rail
88
61731-088
Support
89
61731-089
Nut
90
61731-090
Adjuster
91
61731-091
Joint Guide
92
61731-092
Joint Plate
93
61731-093
Nut
94
61731-094
Nut
95
61731-095
Bushing
96
61731-096
Torsion Spring
97
61731-097
Lock
98
61731-098
Soft Grip Sleeve
99
61731-099
O-Ring
100
61731-100
End Cap
101
61731-101
Air Plug
102
61731-102
Screw
19
Summary of Contents for 61731
Page 18: ...EXPLODED VIEW PARTS LIST 18...