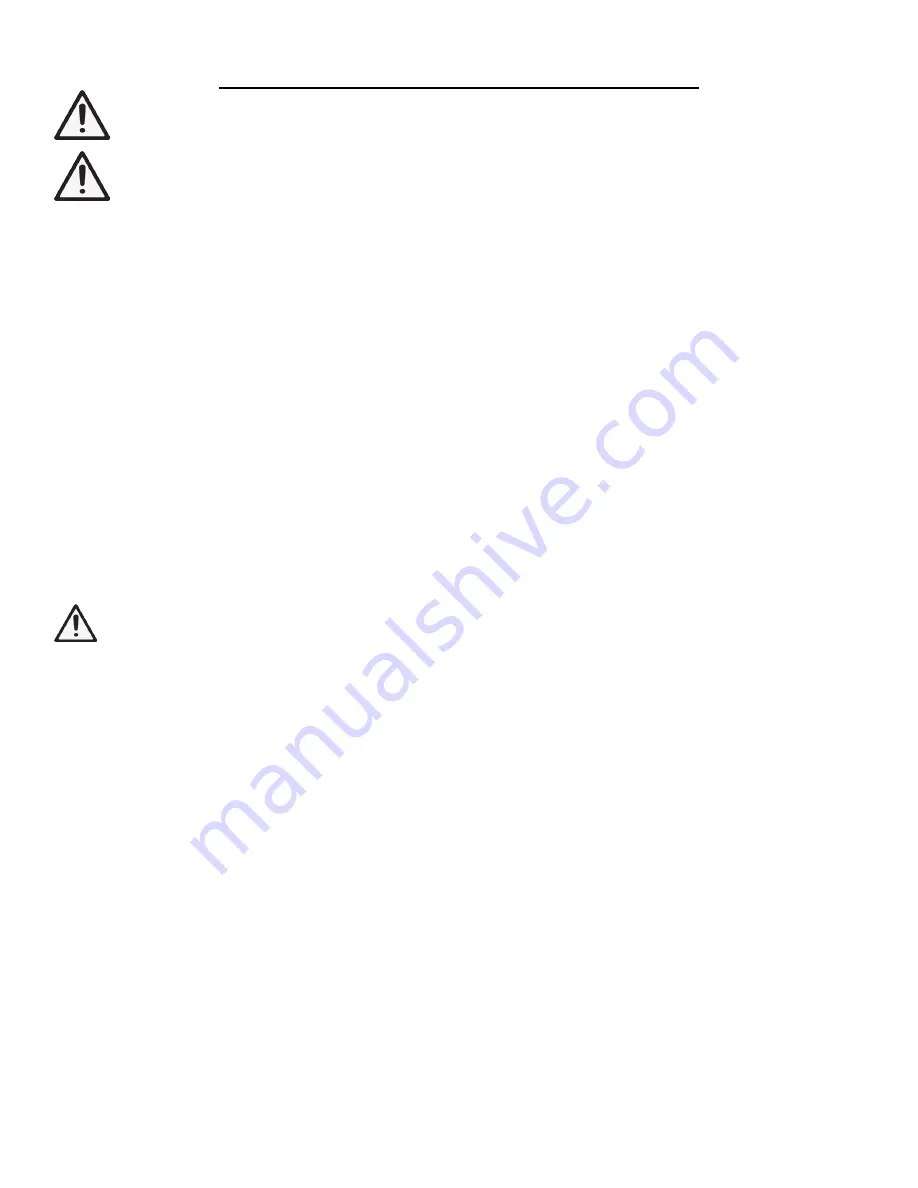
15
OPERATION
WARNING:
To prevent serious injury, make sure all the warnings and instructions have been read and
understood before operating this tool.
PRIOR TO OPERATION
Check that the following requirements are met before plugging in the machine:
• The anti-rust protection has been cleaned off from the machine.
• All obstacles have been cleaned and removed from the machine area and worktable.
• All adjustment tools (chuck key, rod, wrenches) have been removed from the machine.
• The cutter is properly installed and tightened in the holder.
• The workpiece is properly secured in a milling vise or quick vise (not included).
• The workpiece position has been adjusted on the X and Y axes to suit your task.
• The protective shield is in position.
• You are wearing ANSI Z87.1-approved eye protection and a face shield/dust mask.
DRILLING/MILLING OPERATIONS
1. Install the suitable holder/chuck and cutter bit. Tighten them securely.
2. Slowly rotate the speed adjustment knob to turn ON and set it to the appropriate speed. Wait a few seconds for
the machine to reach full speed.
WARNING:
Do not turn on the machine while the cutter is contacting the workpiece.
3A. DRILLING OPERATION. Pull the feed handle towards you to lower the cutter into the workpiece. If a
depth stop has been set, the headstock will automatically stop when it hits the depth stop block. You can also use
the depth gauge on the left of the column to calculate the cutting depth.
3B. MILLING OPERATION. Pull the feed handle towards you to lower the cutter to the desired depth and
tighten the feed lock lever. Rotate handwheels make the cut along the X or Y axis.
NOTE: Make your cut in several progressive passes, instead of trying to take off too much material in one pass.
4. When the cut is complete, clear the cutter from the workpiece.
5. Rotate the speed adjustment knob to the OFF position. Wait for the cutter to come to a complete stop and
raise the headstock all the way to the upper position.
OVERLOAD PROTECTION
The overload protection will shut off the machine automatically during an overload. When this happens, the yel-
low overload light on the left control box will illuminate.
The machine may overload if the feed rate is too fast or if the cutting depth is too deep. When this happens, ro-
tate the speed adjustment knob to the OFF position. Wait a few minutes to allow the motor to cool down and start
the machine again. This time, reduce the feeding rate and cutting depth to prevent overloading the motor again.
WARNING:
Always wear ANSI Z87.1-approved eye protection and a face shield/dust mask when using
this machine. Chips and dust fly at high speed during operation, and may cause injuries if they hit you.