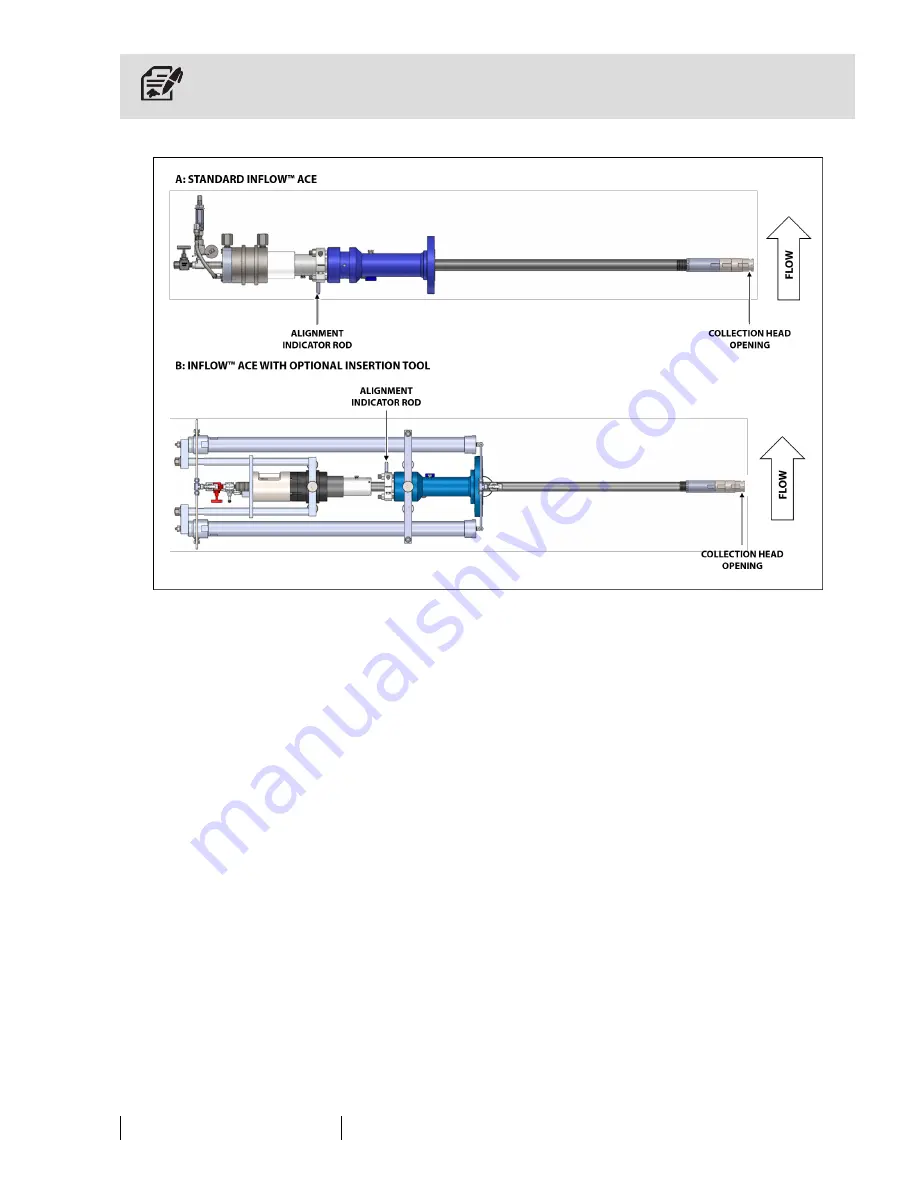
Once the unit is installed to the pipeline, the alignment indicator rod will be an external reference point to the collection head
opening.
Figure 10: Aligning the Collection Head
16
IOM-189
MODEL: INFLOW™ ACE MANUAL INSERTION
REV: G
13839 West Bellfort Street, Sugar Land, TX 77498
welker.com
Service Department 281.491.2331