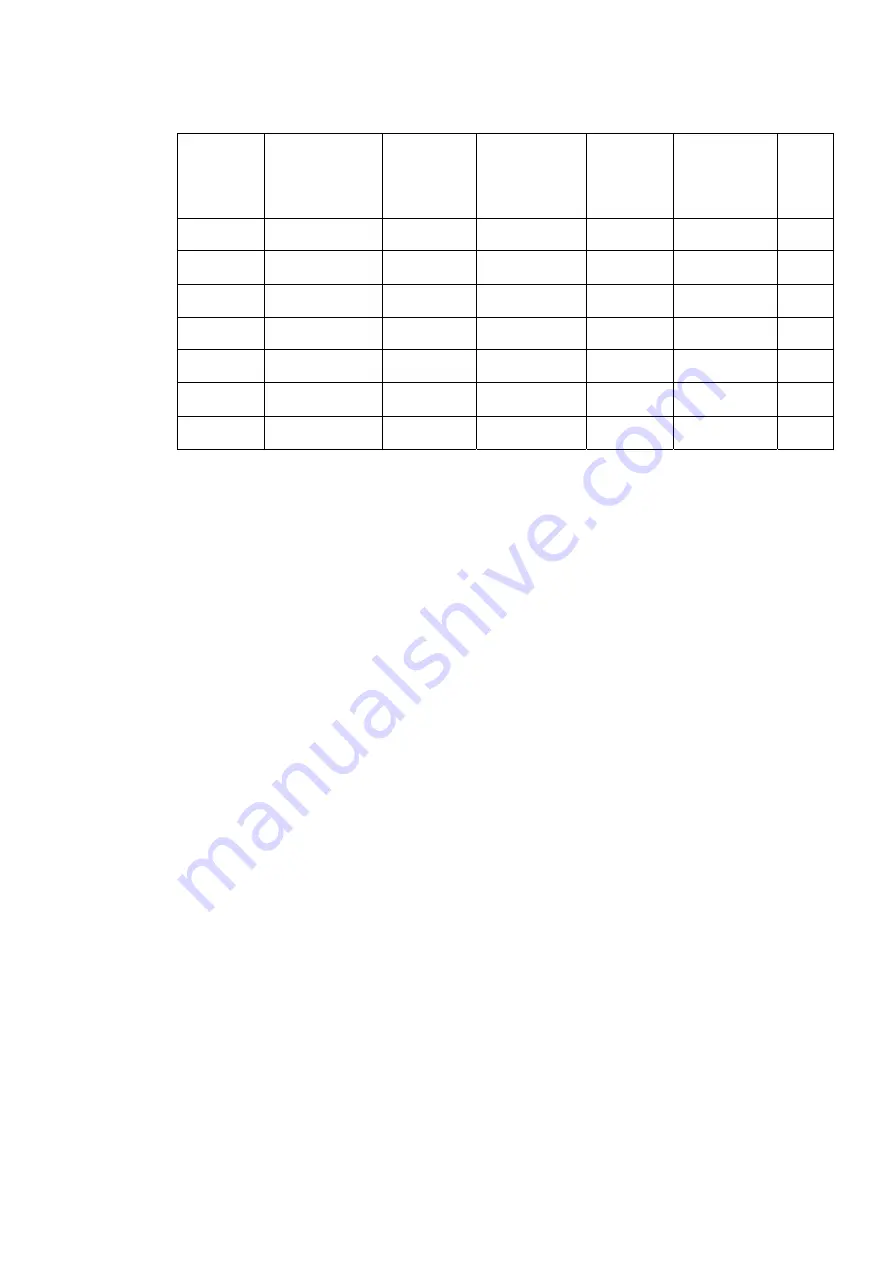
Page 15
Plate
thickness
(mm)
Tungsten
electrode
diameter
(mm)
Taper of
tungsten
electrode
(°)
Tungsten
electrode
end diameter
(mm)
Welding
current
(A)
Max argon
flow rate
(L/min)
Weld
layer
0.2 1.0~1.6 10 0.1
10-15
2
1
0.4 1.0~1.6 20 0.12 15-20
2.5 1
0.6 1.0~1.6 20 0.25 15-30
2.5 1
1.0 1.0~1.6 25 0.50 25-50
3
1
1.6 1.0~1.6 30 0.75 50-70
4
1
2.4 1.6~2.4 35 0.75 65-95
6
1
3.0 1.6~2.4 45 1.10 90-120
7
1-2
Table 3.2