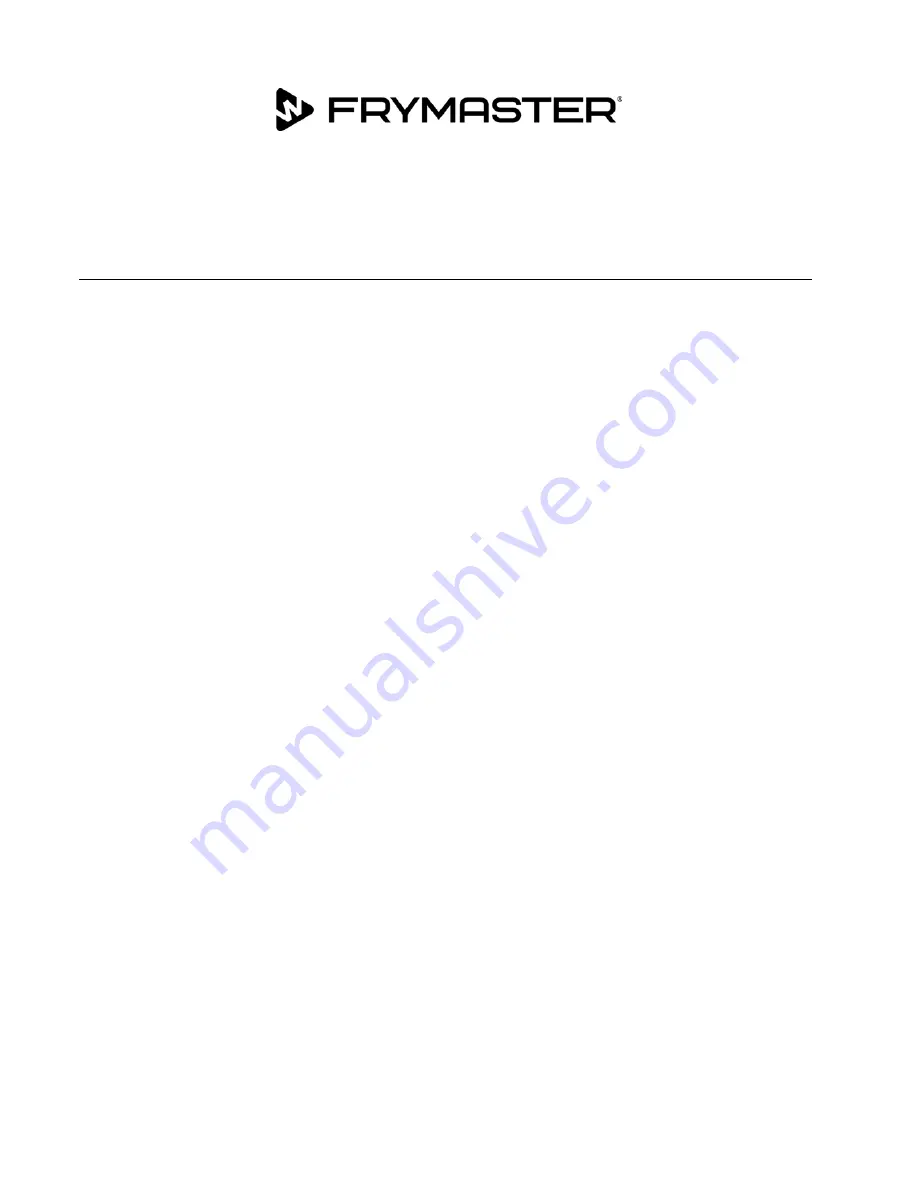
PF50 CE Series Portable Filtration System
Models PF50, PF50S, MFP50 and MFP50S
Operation, Service and Parts Manual
TABLE OF CONTENTS
CHAPTER 1: INTRODUCTION
.................................................................................................. 1-1
CHAPTER 2: IMPORTANT INFORMATION
............................................................................. 2-1
CHAPTER 3: FILTER PREPARATION
........................................................................................ 3-1
CHAPTER 4: OPERATING/FILTER INSTRUCTIONS
................................................................ 4-1
CHAPTER 5: CLEANING AND MAINTENANCE
....................................................................... 5-1
CHAPTER 6: TROUBLESHOOTING/SERVICE PROCEDURES
.................................................. 6-1
CHAPTER 7: PARTS LIST
........................................................................................................... 7-1