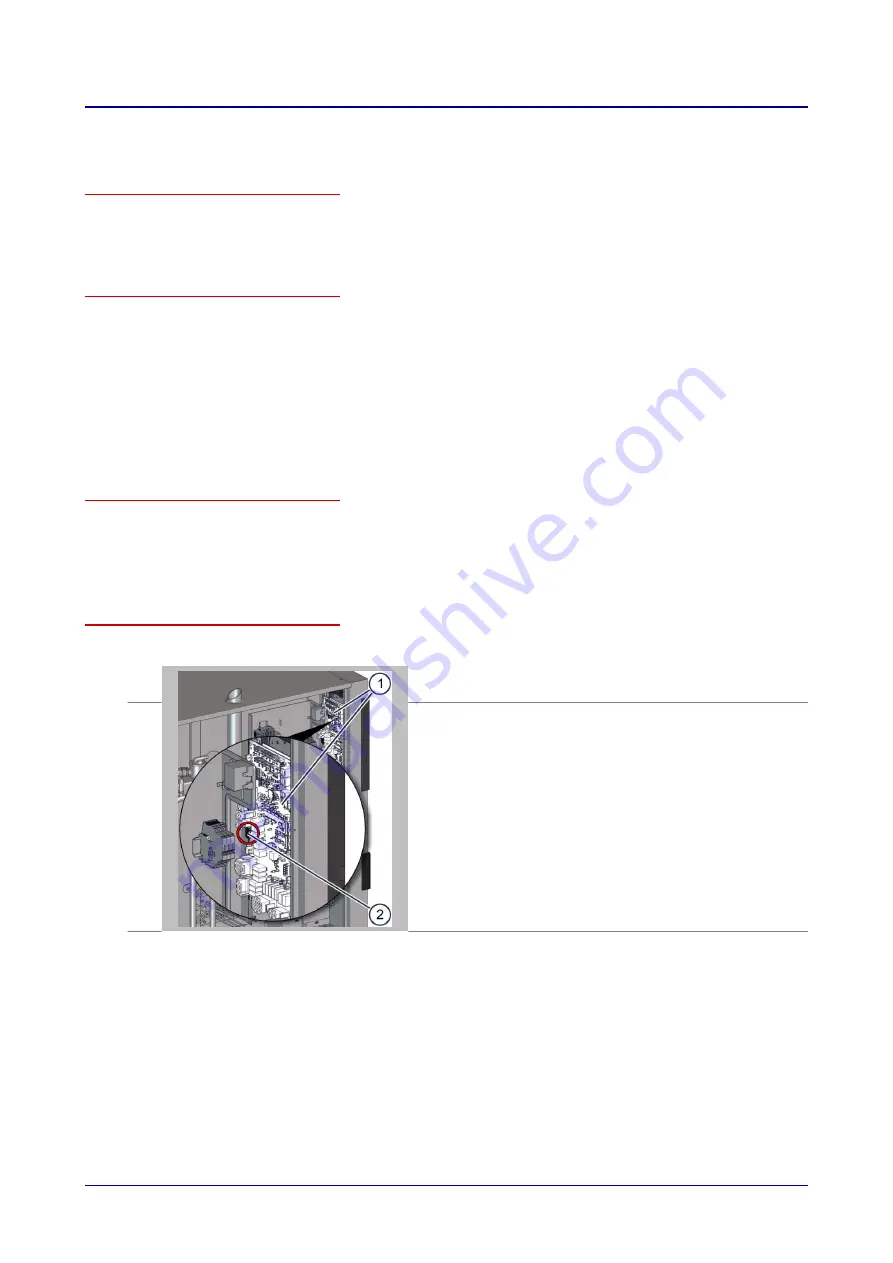
6.1.3 Connecting an energy optimization system
Purpose of an energy optimization system
You can connect the combi oven to an energy optimization system (e.g. SICOTRONIC). An energy optimization system
smooths out peaks in power consumption that occur during operation of your appliances, and can thereby help to reduce
your energy costs.
Configuring an energy optimization system
The energy optimization system must be configured as follows:
■
The connecting lines between the appliance and the energy optimization system should not be longer than 5 m. If this is
not possible, the connection must be carried out using an intermediate relay located at a maximum distance of 5 m from
the appliance.
■
The continuous switch-on time for the combi oven must be set to at least 8 minutes to be certain that the target cooking
temperature is reached.
■
The energy optimization system must not disconnect the power for longer than 30 seconds because the cooking result
cannot be guaranteed for a longer interruption in the power supply.
When connecting the system, refer to the circuit diagram and operating instructions of the energy optimization system.
Accessories required
You need the following parts to connect the energy optimization system:
■
Connecting cable for energy optimization system
■
Cable gland M20
■
Cable ties
Connecting an energy optimization system
The figure below shows a size 12.20 combi oven as an example for all appliance sizes:
1.
Disconnect the energy optimization system and the combi oven from
the power supply.
2.
Remove the side panel from the combi oven in order to access termi-
nal block -X37 (2) on the system interface board (SIB) (1) in the area
behind the operating panel.
6 Installation
Installation manual
43
Summary of Contents for C4 EB 12.20
Page 2: ......
Page 5: ...10 9 Convotherm 4 20 20 injection gas appliance 117 Table of Contents Installation manual 5 ...
Page 119: ......