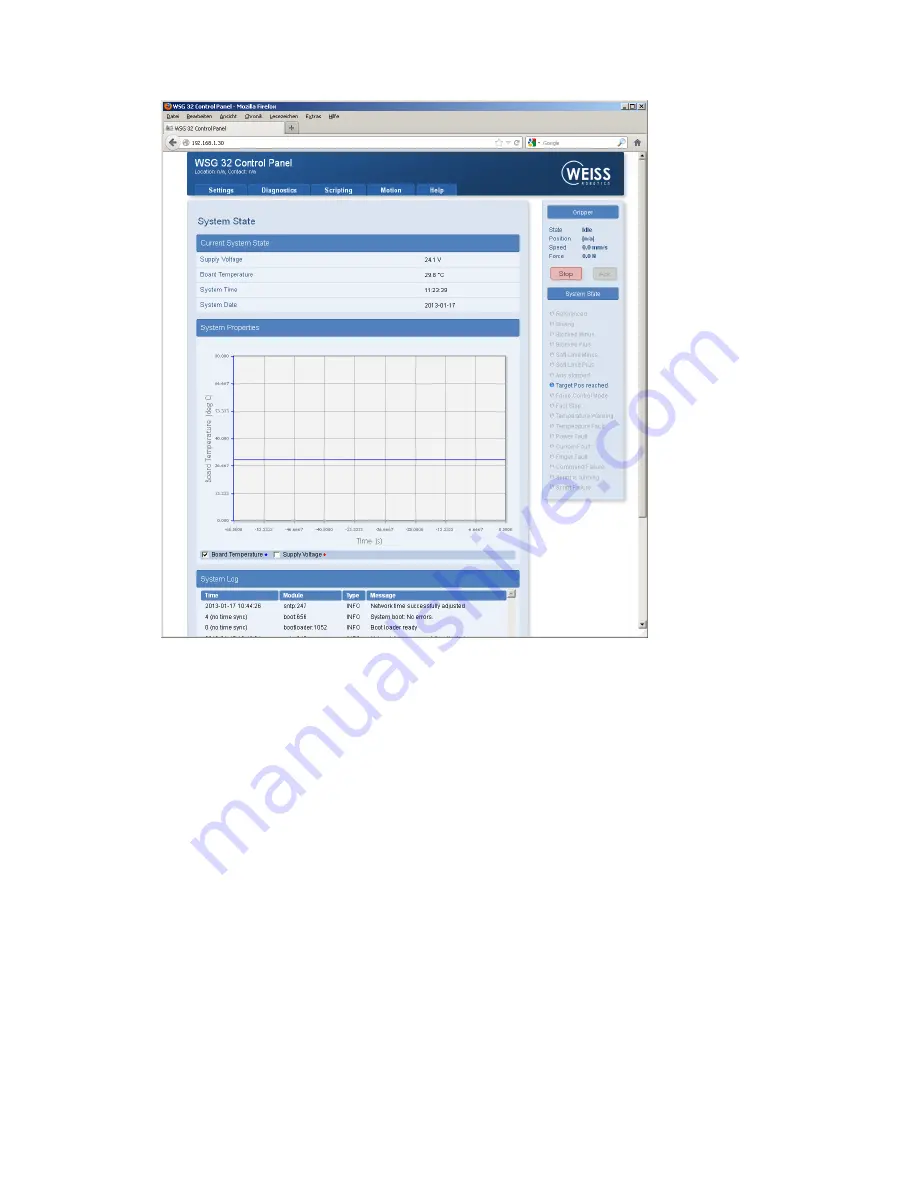
- 42 -
Via integrated help texts, the module’s web interface is intuitive to use. In the upper area you will find a
menu bar via which the individual pages can be called up.
9.15
Access restrictions for the web user interface
Depending on the network configuration, the module will be visible to everyone in the entire network and
the configuration can thus be altered unchecked.
To restrict access to the module's web interface, under "Settings” → “System Configuration" you can acti-
vate access restrictions for the interface and create users with differing access rights. If this is activated,
each user must be identified with a login name and personal password (Figure 28). Every user is assigned to
one of the following user groups:
User
Standard user. Cannot adjust settings, but can only access the pages under the menu options “Di-
agnostics“ and “Help“.
Figure 27: Web interface for configuration and diagnosis
Summary of Contents for WSG 32
Page 2: ......
Page 7: ... 5 Reference to further information ...
Page 14: ... 12 7 Technical Data 7 1 Outer dimensions Figure 2 Outer dimensions ...
Page 48: ... 46 ...