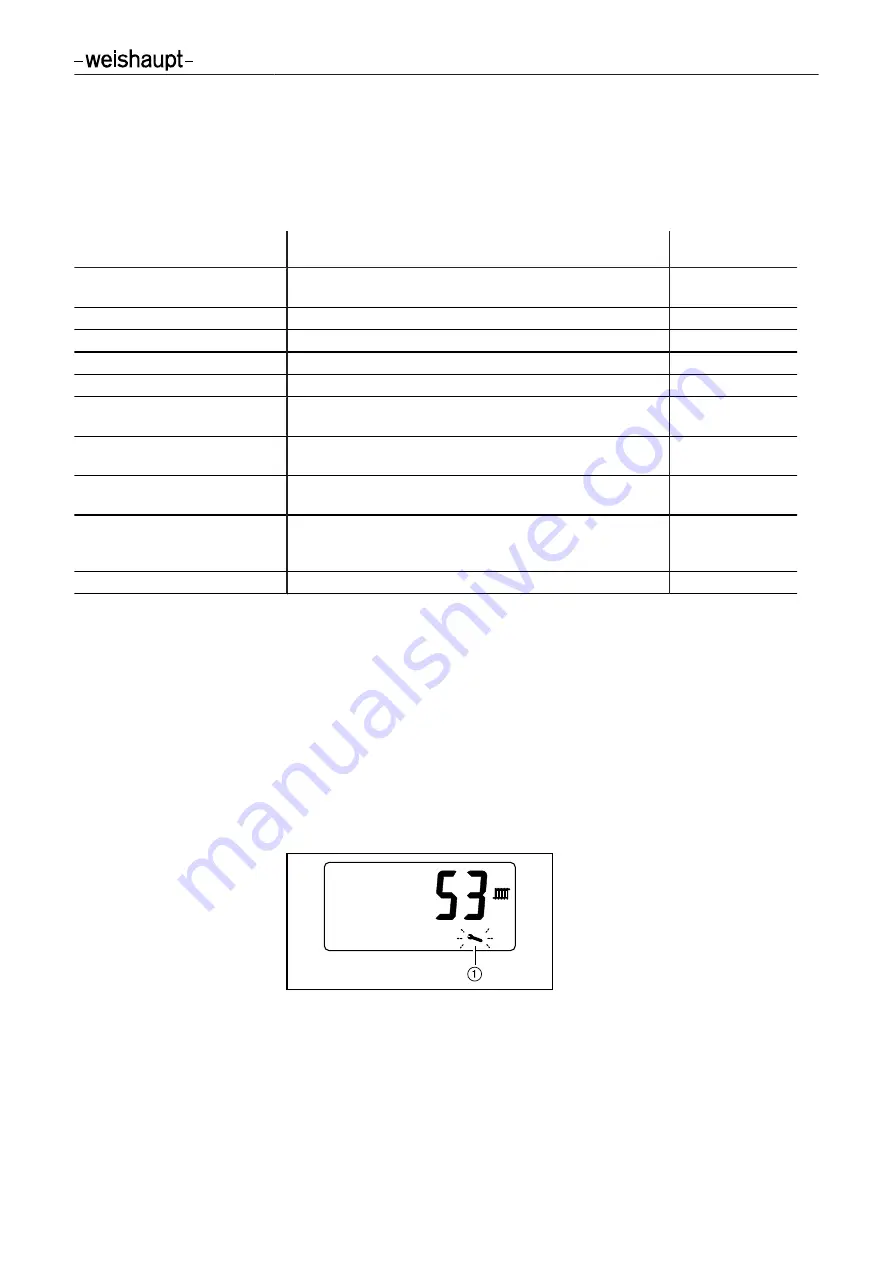
9.1 Safety components
Vital safety components must be replaced as soon as they reach their predefined
lifetime.
The predefined lifetime is not the warranty time specified in the terms and conditions
of delivery and payment.
Safety
component
Lifetime
according to construction
CEN-Standard
Printed circuit board (WCM-
CPU)
10 years or 250 000 operating cycles
EN 298-2003
Gas combi valve
10 years or 250 000 operating cycles
EN 126-1993
Gas pressure switch
10 years
EN 1854-1997
Air pressure switch
10 years
EN 1854-1997
Flue gas pressure switch
1 000 000 operating cycles
EN 1854-1997
Gasket
fan air outlet
10 years
EN 549 H3/B1
O ring 70 x 3
Gas valve/fan
10 years
EN 549 H3/B1
O ring 33 x 2
Gas valve/gas connection piece
10 years
EN 549 H3/B1
O ring 10.5 x 2.25
Pressure switch/gas connec-
tion piece
10 years
EN 549 H3/B1
Safety valve 3 bar
10 years
TRD 721-1997
9.2 Servicing display
The time interval to the next service can be set. A flashing spanner will appear in the
display when the set interval has expired.
Servicing
is displayed, if a remote control
station is used.
Setting the service interval
▶
Activate parameter level (see Ch. 6.3).
▶
Set service interval via parameter
70
.
Resetting the service display
The service display
1
must be reset after servicing.
▶
Activate info level (see Ch. 6.3).
▶
Select
46
in Info level i (see Ch. 6.3.1).
▶
Press enter button for 2 seconds.
✓
Service display and timer will be reset.
Installation and operating instruction
Gas condensing boiler WTC-GB 90-A
9 Servicing
83266502 • 1/2010-08 • La
63-95