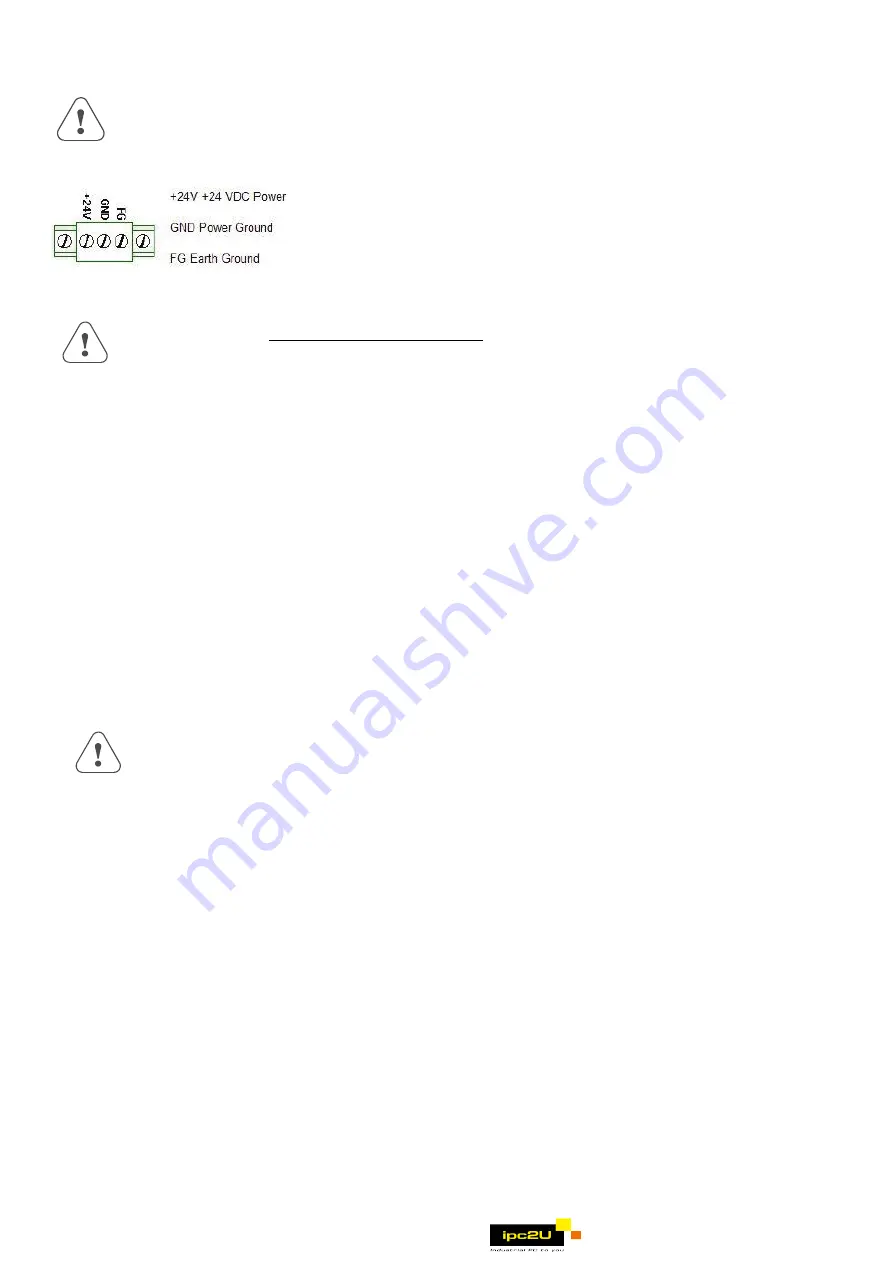
3
Equip ungrounded DC supplies with a resistor and capacitor in parallel to
earth ground. This provides a path for static and high frequency
dissipation. Typical values to use are 1MOhm and 4700pF.
Caution !
To prevent the HMI from becoming damaged or having sound output
issues, after turning the device off, please wait 10 seconds before turning
the device on again.
Connection
To make a connection, strip about 3/8” of insulation off the end of the
wire, turn the connector screw counterclockwise until the gap is wide
open, insert the wire all the way in, and turn the screw clockwise until it’s
tight.
Connect positive DC line to the ‘+24V’ terminal and the DC ground to the
‘0V‘ terminal.
2.2.2 Grounding Requirements
Chassis ground must be used. DC ground is not directly coupled to Earth
ground internally. It is preferable not to ground DC negative return to chassis
ground as poor site earths can introduce noise into a system, but if necessary
an earth connection should be made, from the power supply return point to
the central star earth point. Ground conductors should be as short and as large
in size as possible. The conductors must always be large enough to carry the
maximum short circuit current of the path being considered. Ground
conductors should be connected to a tree from a central star earth ground
point. This ensures that no ground conductor carries current from any other
branch.
2.2.3 CE Requirements
To make an MT-600/8000 comply with EMC directives, and to reduce susceptibility to electrical
interference, a separate #14 AWG ground wire should be taken to the chassis ground terminal of the
power connector. This ground connection should be run directly to the central star earth connection
point (as recommended in most Installation Instructions).
2.2.4 Safety Guidelines
This section presents recommended installation practices, and procedures. Since no two
applications are identical, these recommendations should be considered as guidelines.
Hardware
Considerations
WARNING!
The system designer should be aware that devices in Controller systems
could fail and thereby create an unsafe condition. Furthermore, electrical
interference in an operator interface, such as an MT-600/8000, can lead to
equipment start-up, which could result in property damage and/or physical
injury to the equipment operator.
If you, or your company, use any programmable control systems that require
an operator or attendant, you should be aware that this potential safety hazard
exists and take appropriate precautions. Although the specific design steps
depend on your particular application, the following precautions generally
apply to installation of solid-state programmable control devices. In addition,
these precautions conform to the guidelines for installation of Controllers as
recommended in the NEMA ICS 3-304 Control Standards.
Programming
Considerations
To conform with ICS Safety Recommendations, checks should be placed
in the controller to ensure that all writable registers that control critical
parts of plant or machinery have limit checks built into the program, with
an out-of-limit safe shut down procedure to ensure safety of personnel.
ICS 3-304.81 Safety Recommendations:
Consideration should be given to the use of an emergency stop function, which is independent of the programmable controller.
Where the operator is exposed to the machinery, such as in loading or unloading a machine tool, or where the machine
cycles automatically, consideration should be given to the use of an electromechanical override or other redundant means,
independent of the programmable controller, for starting and interrupting the cycle.
If provision is required for changing programs while the equipment is in operation, consideration should be given to the use
of locks or other means of assuring that only authorized personnel can make such changes.
These recommendations are intended as safeguards against the failure of critical components and the effects of such failures
or the inadvertent errors that might be introduced if programs are changed while the equipment is in operation. *
www.ipc2u.ru