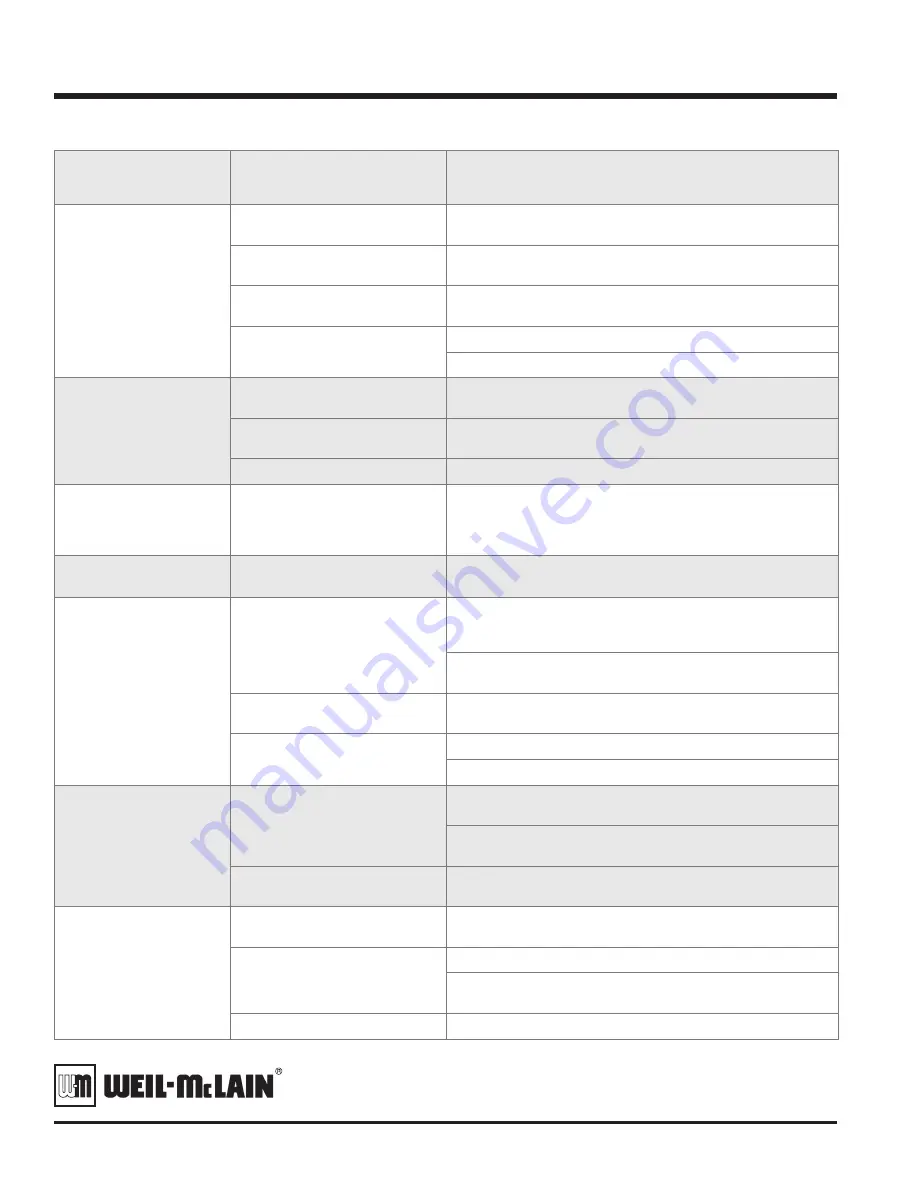
20
Part No. 550-142-801/1112
Weil-McLain
500 Blaine Street
Michigan City, IN 46360-2388
http://www.weil-mclain.com
Common problems and solutions
Symptom
Common Causes
Possible Corrections
Rapid cycling —
boiler turns on and
off frequently
Thermostat installed where drafts
or heat affect reading
Locate thermostat on inner wall away from heat sources or cool
drafts.
Heat anticipator in thermostat
adjusted incorrectly
Adjust thermostat per manufacturer's instructions.
Incorrect limit setting
Set limit according to system needs. Maximum setting is 220°F.
Increase limit setting to decrease cycling.
Insufficient water flow through
boiler
Check all valves to and from boiler. Return to proper setting.
Confirm circulator size.
Frequent release of
water through relief
valve
Expansion tank sized too small
Call qualified service technician to check expansion tank
operation and size.
Flooded expansion tank
Call qualified service technician to check expansion tank
operation.
Inoperative limit control
Call qualified service technician to replace limit control.
Need to frequently
add makeup water
Leaks in boiler or piping
Have qualified service technician repair leaks at once to avoid
constant use of makeup water. Makeup water can cause
mineral deposits which, in turn, can cause boiler section failure.
Do not use petroleum-base stop-leak compounds.
Black water
condition
Oxygen corrosion due to leaks in
boiler and piping
Have qualified service technician repair at once. Keep pH of
water between 7.0 to 8.5.
Popping or
percolating noise
heard in boiler
Mineral deposits in sections due
to constant use of makeup water
Call qualified service technician to de-lime boiler, if necessary.
In some cases, deposits will be too heavy to remove with de-
liming procedures.
Have qualified service technician repair leaks to eliminate need
for constant makeup water.
Incorrect pH of boiler water
Call qualified service technician to check pH level and correct.
pH should be maintained between 7.0 to 8.5.
Insufficient water flow through
boiler
Check all valves to and from boiler. Return to proper setting.
Confirm circulator size.
Metal flakes found in
vent outlet or vent —
flueway corrosion
Contaminated combustion air
supply — See page 3 in this
manual.
Remove any contaminating products. See page 3 in this
manual.
Provide outside air for combustion.
Condensation of combustion
gases in boiler sections
Have qualified service technician inspect system piping and
controls to verify proper regulation of return water temperature.
Some radiators or
baseboard units do
not heat or are noisy
Air in system
Bleed air from system through air vents in radiators or
baseboard units.
Low system pressure
Fill to correct pressure.
Check for leaks in boiler or piping. Have qualified service
technician repair at once.
High limit set too low
Adjust high limit to higher setting.