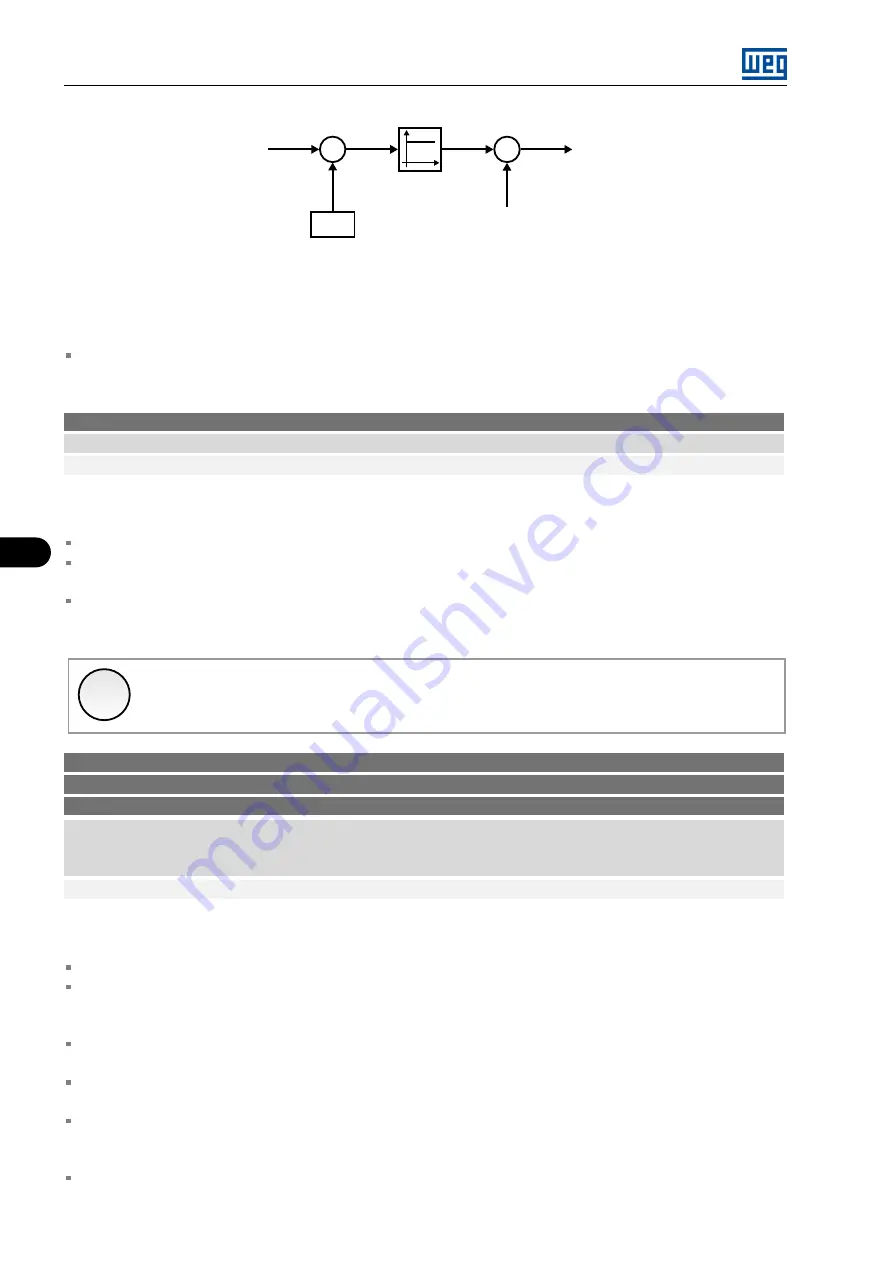
5
DETAILED PARAMETER DESCRIPTION
+
+
-
-
DC Link
voltage
(Ud)
Ramp
output
P0152
P0151
P0152 > 0
Speed
Figure 5.17:
Block diagram of the DC link voltage regulation
Vector Mode (P0202 = 3 or 4):
P0151 defines the DC link regulation level during braking. During the braking process, the deceleration ramp
time is automatically extended, thus avoiding an overvoltage fault.
P0152 - Proportional gain of the DC link voltage regulator
Adjustable range:
0.00 to 9.99
Factory setting:
0.00
Acesso:
Menu
→
Configurations
→
Control
Description:
Refer to P0151 (with V/F control) and
If P0152 = 0.00 and P0151 different from the maximum value, the ramp holding function is active. Refer to
P0151 for V/F.
P0152 multiplies the voltage error of the DC link, that is, error = present DC link-P0151. P0152 is typically
used to prevent overvoltage in applications with eccentric loads.
✓
NOTE!
This parameter is only visible on the HMI when: the control type is scalar, P0202 = 0, 1 or 2 (V/F
control).
P0156 - Overload current at 100 %
P0157 - Overload current at 50 %
P0158 - Overload current at 5 %
Adjustable range:
0.0 to 3420.0 A
Factory setting:
P0156 = 154.0 A
P0157 = 126.0 A
P0158 = 70.0 A
Acesso:
Menu
→
Configurations
→
Protections
Description:
It is for the motor and inverter overload protection.
The motor overload current is the value above which the inverter considers that the motor is operating under
overload. The higher the difference between the motor current and the overload level, the sooner the fault
occurs.
Parameter P0156 Motor Overload Current at Rated Speed) must be adjusted 10 % higher than the used motor
rated current (P0401).
The overload current is obtained as a function of the speed being applied to the motor, according to the
overload curve.
Parameters P0156, P0157 and P0158 are the three points used to form the motor overload curve, as shown
in
for the factory setting. Refer to
Item 6.3.2 Initial Power-up (Parameter Setting)
on page 6-13
of the user’s manual.
With the overload current curve adjustment it is possible to program an overload value that varies according
to the inverter operation speed (factory default), improving the protection for self-ventilated motors, or to use
a constant overload level for any speed applied to the motor (motor with separated ventilation).
MVW3000 | 5-24
Summary of Contents for MVW3000 Series
Page 2: ......
Page 58: ...1 QUICK REFERENCE OF PARAMETERS AND FAULTS MVW3000 1 52...
Page 62: ...2 SAFETY INSTRUCTIONS MVW3000 2 4...
Page 192: ...6 SPECIAL FUNCTIONS MVW3000 6 4...
Page 262: ...7 DIAGNOSTICS AND TROUBLESHOOTING MVW3000 7 70...
Page 263: ......