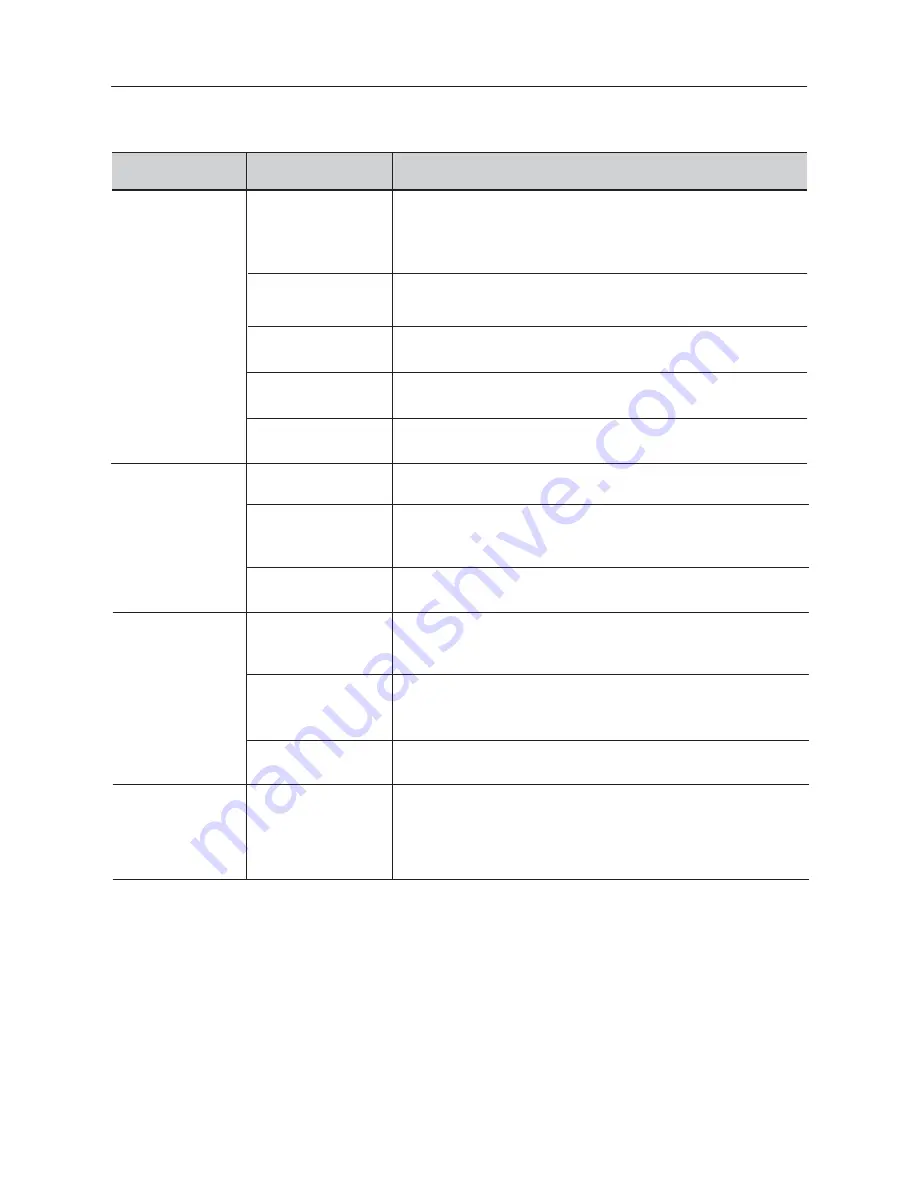
80
CHAPTER 7 -
DIAGNOSTICS AND TROUBLESHOOTING
7.2
TROUBLESHOOTING
PROBLEM
POINT TO BE
CORRECTIVE ACTION
CHECKED
Motor does not run
Incorrect wiring
1.Check the power and the control connections. For example,
the digital inputs DIx programmed for Start/Stop or General Enable
or No External Fault must be connected to GND (pin 5 of the
control connector XC1).
Analog reference
1.Check if the external signal is properly connected.
(if used)
2.Check the status of the speed potentiometer (if used).
Incorrect Programming 1.Check if the parameters are properly programmed for the
application.
Fault
1.Check if the inverter has not been disabled due to detected fault
condition (refer to Table above).
Motor Stall
1.Reduce the motor load.
2.Increase P169 or P136/P137.
Motor speed
Loose connections
1.Disable the inverter, switch OFF the power supply and tighten all
oscillates
connections.
Defective speed
1.Replace the defective speed potentiometer.
potentiometer
Variation of the external 1.Identify the cause of the variation.
analog reference
Motor speed
Programming error
1.Check if the contents of P133 (minimum frequency)
too high or
(reference limits)
and P134 (maximum frequency) are according to the motor
too low
and the application.
Signal of the
1.Check the control signal level of the reference.
Reference Control
2.Check the programming (gains and offset) at P234 to P236.
Motor nameplate
1.Check if the used motor meets the application requirements.
data
Display OFF
Power supply
1.The power supply must be within the following ranges:
200-240V models: - Min: 170V
- Max: 264V
110-127V models: - Min: 93V
- Max: 140V