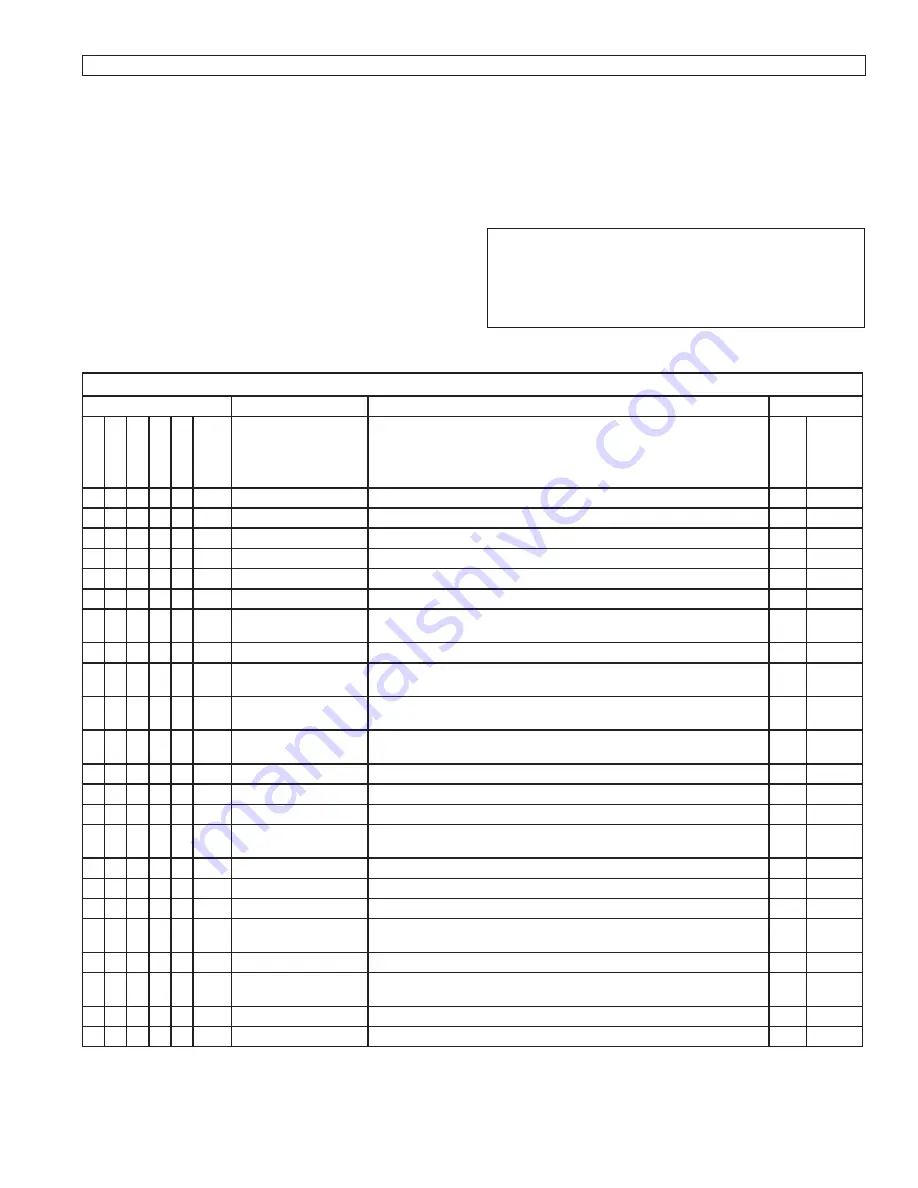
Page 19
General Maintenance and Care
SG Manual
H. GENERAL MAINTENANCE AND CARE (continued)
As a minimum, the following replacement parts should be
stocked to support uninterrupted burner operation.
Electrode
Blower Wheel
Ignition Transformer
Gas Solenoid Valve
Flame Scanner
Items with greater life expectancy and/or greater dollar
value, such as flame safety controls, main gas valves and
blower motors should be obtained from your local Webster
representative when a need arises.
8 - Inspection and Maintenance Schedule
Frequency
Performed By
Daily
W
eekly
Monthly
Seasonal
Annual
Annual
As
Required
Component / Item
Recommended Action or Test
Boiler
Operator
Trained Burner
Technician
X
Burner Flame
Visual inspection of burner flame.
X
X
Jackshaft and Linkage
Visual inspection for smooth and free travel.
X
X
Air Damper
Visual inspection for smooth and free travel.
X
X
Fuel Metering Valves
Visual inspection for smooth and free travel.
X
X
Draft Controls (Stack)
Visual inspection for smooth and free travel.
X
X
Gas Fuel Pressure
Record in log book, compare trends.
X
X
Flame SafeGuard - Main
Flame
Close manual fuel valve on pilot during cycle and check for safety shutdown,
recording time.
X
X
Flame SafeGuard
Check flame safeguard components, including scanner.
X
X
Flame SafeGuard
Replace flame safeguard components in accordance with manufacturers
instructions.
X
X
X
Hot Refractory Test
Conduct hot refractory hold in test. This test is required annually or after any
component change.
X
X
Interlock Controls
Check other interlocks that may be used on the burner for smooth operation
and correct action.
X
X
Firing Rate Control
Check firing rate control and verify settings.
X
X
Combustion Tuning
Conduct a combustion test, verify setting and NOx emission levels.
X
X
Main Fuel Valves
Make visual and manual check for proper sequencing of valves.
X
X
Main Fuel Valves
Check all coils, diaphragms, interlock switch & other parts of all safety shutoff
valves.
X
X
Main Fuel Valves
Perform leak tests on all safety shutdown control valves.
X
X
Low Pressure Air Switch
Test low air pressure switch for proper operation and adjustment.
X
X
Mod Damper Switch
Check damper low fire proving switch per manufacturers instructions.
X
X
Linkage and Fuel Cams
Check linkage and cams for wear and replace any items with wear indication
or stress cracks.
X
X
Combustion Air Fan
Clean combustion air fan and housing
X
X X
Burner Components
Visually check the burner components for signs of cracks, deformation, slip-
page or other unusual indication.
X
X
Burner Mounting
Check burner mounting clamps and brackets for tightness.
X
X
Refractory and Seals
Check burner refractory for cracks or signs of leakage.
X
NOTE
Always give Webster Engineering Serial
Number and/or UL Serial Number when
ordering parts.
An illustrated parts drawing is included within the Burner
Instructions Manual to aid in parts identification. The noun
name of the part needed should be established from the
drawing, then the part number can be obtained from the
burner material list contained in the Burner Instructions
and Service Manual.
Summary of Contents for Cyclonetic SG Series
Page 22: ...Page 22 SG Manual Notes NOTES ...
Page 23: ...Page 23 SG Manual Notes NOTES ...