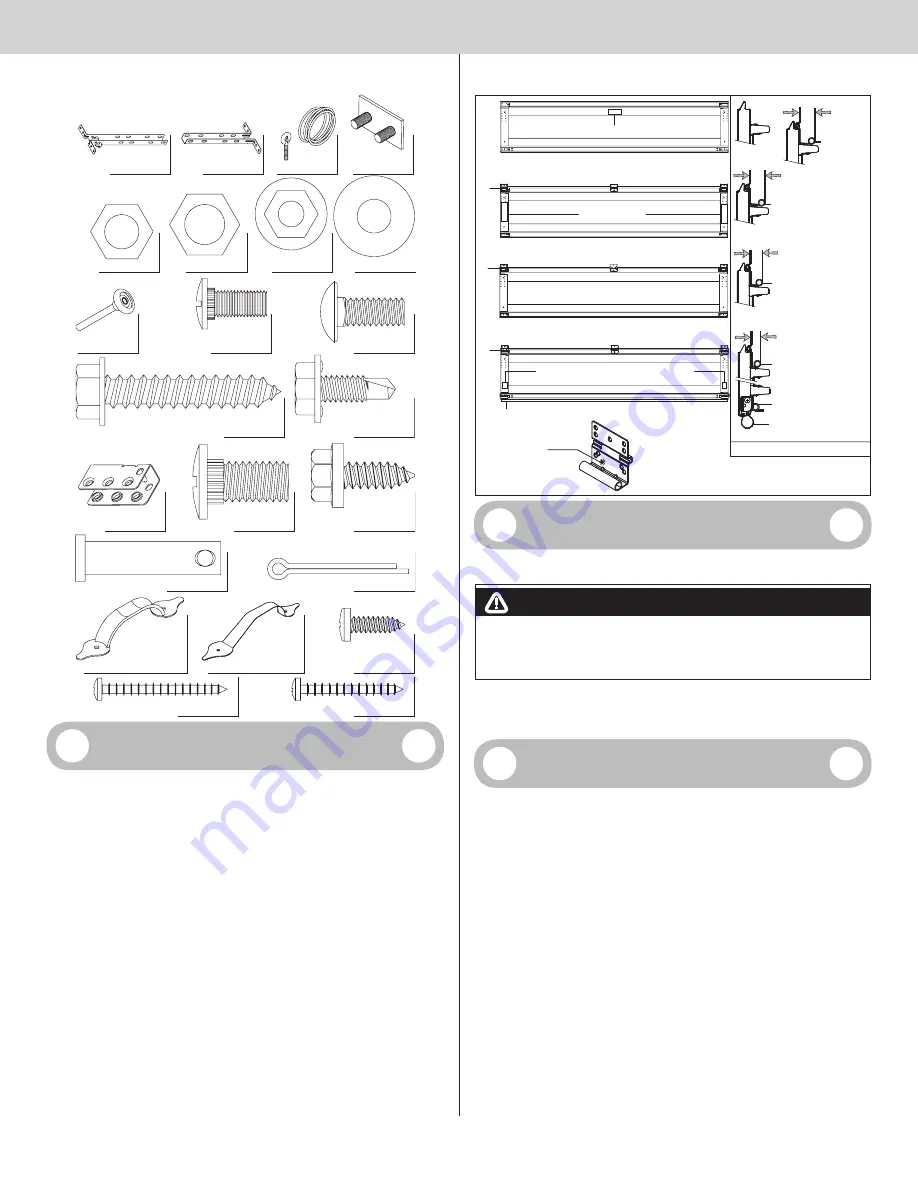
Pull down
rope (if included)
Stud Plate
(as required)
(2) 3/8”- 16 Hex nuts
1/4”- 20 Flanged
hex nuts (as required)
(2) 5/16” Washers
(2) 5/16”-18 Hex nuts
Top half drawbar
operator bracket
Bottom half drawbar
operator bracket
5/16” x 1 5/8” Hex head lag screws
(as required)
1/4”-20 x 11/16” Self
drilling screws (as required)
(2) 5/16”-18 x 3/4”
Carriage bolts
1/4”-20 x 9/16”
Track bolts (as required)
Track rollers
(as required)
1/4”-14 x 5/8” Self tapping
screws (as required)
(2) 3/8”-16 x 3/4”
Truss head bolts
Cotter pin
5/16” x 1-1/4” Clevis pin
Drawbar operator
bracket arm
#8 x 1-13/32” Quadrex pan head screws
#8 x 1-21/32” Quadrex pan head screws
#10 x 5/8”
Phillips pan head screws
(black painted heads)
Pull handles (as required)
Lift handles (as required)
Door Section Identification
Graduated end and center hinges are always pre-attached at the top of each section (except
top section) and the graduated end hinges are stamped for identification, #1, #2, #3, and #4
(#4 only on five section doors). The stamp identifies the stacking sequence of the section.
The sequence is always determined by #1 being the bottom section to #3 or #4 being the
highest intermediate section. If the stamp on the graduated end hinge is illegible, refer to
the section side view illustration. The section side view illustration shows the graduated end
hinge profile of all sections, and can also be used to identify each section.
The
BOTTOM SECTION
can be identified by #1 graduated end hinges, the factory attached
bottom astragal, the factory attached bottom corner brackets, and by the bottom corner
bracket warning labels on each end stile.
The
LOCK SECTION
can be identified by #2 graduated end hinges.
The
INTERMEDIATE SECTION
can be identified by #3 graduated end hinges. The section
will have a warning label attached to either the right or left hand end stile.
NOTE:
#4 graduated end hinges are used on the fourth section of five section doors.
The
TOP SECTION
can be identified with no pre-installed graduated end or center hinges.
Warning label
Warning label
Top section
Intermediate section
Lock section
Bottom corner bracket warning labels
Bottom section
Astragal
#3
#2
#1
#1 Graduated
end hinge
Bottom corner
bracket
Astragal
Section side view illustration
#2 Graduated
end hinge
1-1/8”
7/8”
#3 Graduated
end hinge
1-3/8”
1-9/16”
#4
Graduated
end hinge
Typical graduated end
hinge stamping
location
Removing an Existing Door
IMPORTANT:
COUNTERBALANCE SPRING TENSION MUST ALWAYS BE RELEASED BEFORE
ANY ATTEMPT IS MADE TO START REMOVING AN EXISTING DOOR.
WARNING
WARNING
A POWERFUL SPRING RELEASING ITS ENERGY SUDDENLY CAN CAUSE
SEVERE OR FATAL INJURY. TO AVOID INJURY, HAVE A TRAINED DOOR
SYSTEMS TECHNICIAN, USING PROPER TOOLS AND INSTRUCTIONS,
RELEASE THE SPRING TENSION.
For detailed information see supplemental instructions “Removing an Existing Door / Prepar-
ing the Opening”. These instructions are not supplied with the door, but are available at no
charge from Wayne Dalton, A Division Of Overhead Door Corporation, P.O. Box 67, Mt. Hope,
OH., 44660, or at
www.Wayne-Dalton.com
.
Preparing the Opening
IMPORTANT:
IF YOU JUST REMOVED YOUR EXISTING DOOR OR YOU ARE INSTALLING A
NEW DOOR, COMPLETE ALL STEPS IN PREPARING THE OPENING.
To ensure secure mounting of track brackets, side and center brackets, or steel angles to
new or retro-fit construction, it is recommended to follow the procedures outlined in DASMA
technical data sheets #156, #161 and #164 at
www.dasma.com
.
The inside perimeter of your garage door opening should be framed with wood jamb
and header material. The jambs and header must be securely fastened to sound framing
members. It is recommended that 2” x 6” lumber be used. The jambs must be plumb and
the header level. The jambs should extend a minimum of 12” (305 mm) above the top of
the opening for TorqueMaster
®
counterbalance systems. For low headroom applications, the
jambs should extend to the ceiling height. Minimum side clearance required, from the open-
ing to the wall, is 3-1/2” (89 mm).
IMPORTANT:
CLOSELY INSPECT JAMBS, HEADER AND MOUNTING SURFACE. ANY WOOD
FOUND NOT TO BE SOUND, MUST BE REPLACED.
For TorqueMaster
®
counterbalance systems, a suitable mounting surface (2” x 6”) must be
firmly attached to the wall, above the header at the center of the opening.
NOTE:
Drill a 3/16” pilot hole in the mounting surface to avoid splitting the lumber. Do not
attach the mounting surface with nails.
WEATHERSTRIPS (MAY NOT BE INCLUDED):
Depending on the size of your door, you may have to cut or trim the weatherstrips (if neces-
sary) to properly fit into the header and jambs.
NOTE:
If nailing product at 40°F or below, pre-drilling is required.
NOTE:
Do not permanently attach weatherstrips to the header and jambs at this time.
3
Summary of Contents for TorqueMaster Plus 6100
Page 21: ......