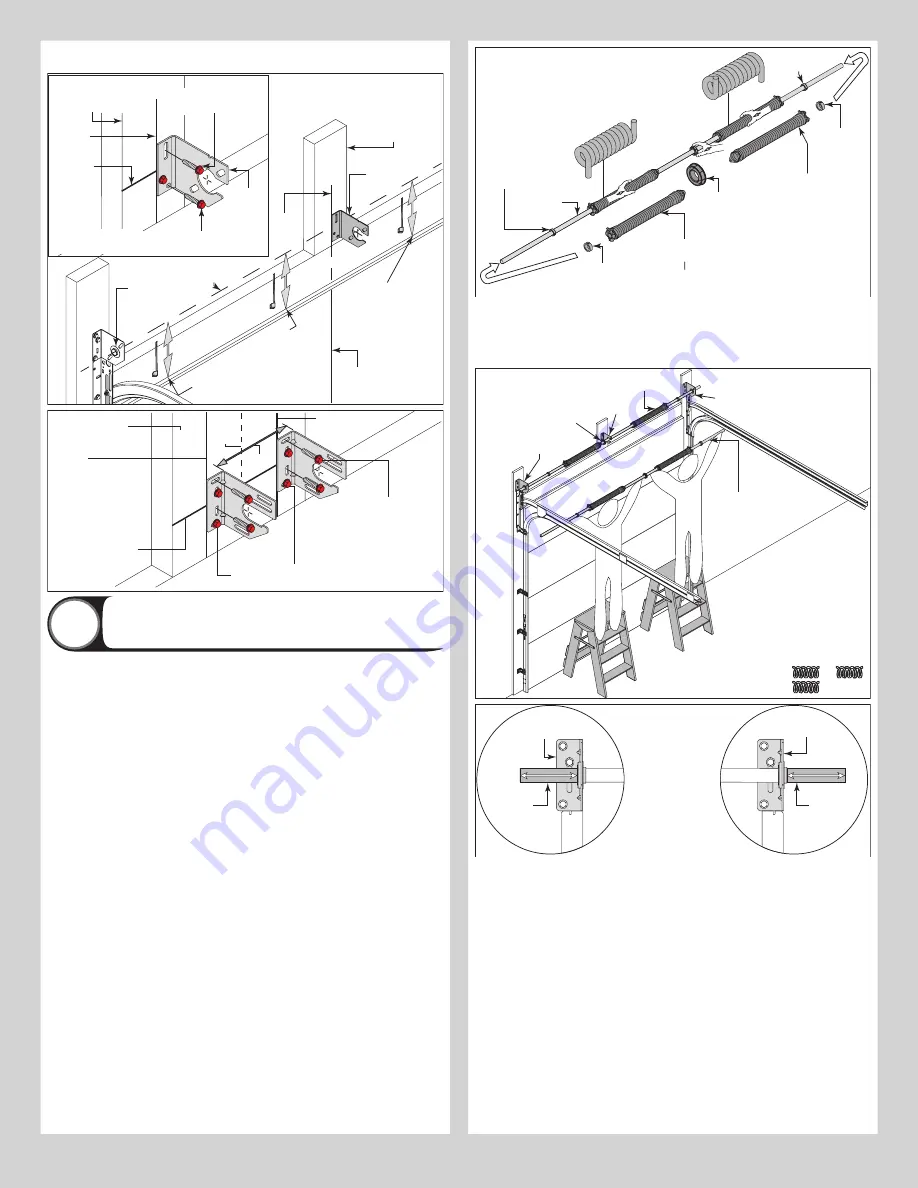
IF MOUNTING SURFACE IS A 2” X 6” BOARD INSTALLED ON TOP OF MASONRY, DRILL A
CLEARANCE HOLE IN MASONRY FOR THE 5/16” X 2-1/2” RED HEAD LAG SCREWS.
Spring mounting
pad (2” X 6”), White
Pine or denser.
Typical
center
bracket
Vertical
line
Equal distance (top of door
section to horizontal line)
Horizontal
line
Typical center
of left hand
end bearing
bracket
Jamb
Equal distance (top of door
section to horizontal line)
Center
of door
Center
bracket
5/16” x 1-5/8” Hex head
lag screws (RED HEAD)
Vertical
line
Horizontal
line
5/16” x 1-5/8” Hex head lag screw (RED HEAD) or
5/16” x 2-1/2” Hex head lag screw (RED HEAD)
Spring mounting
pad (2” X 6”), White
Pine or denser.
5/16” x 1-5/8” Hex head
lag screws (RED HEAD)
Vertical
line
Mounting surface
(17” Minimum)
Horizontal
line
Vertical line
† (2) Center bearing
brackets spaced 6” to
7” apart from the
center of the door.
Center
of
door
†12”
5/16” x 1-5/8” Hex head lag screw (RED HEAD) or
5/16” x 2-1/2” Hex head lag screw (RED HEAD)
Torsion Spring Assembly
18
NOTE:
Refer to the Package Contents and or Parts Breakdown to determine if your door
came with a coupler assembly.
IMPORTANT:
RIGHT AND LEFT HAND IS ALWAYS DETERMINED FROM INSIDE THE BUILDING
LOOKING OUT.
IMPORTANT:
IDENTIFY THE TORSION SPRINGS PROVIDED AS EITHER RIGHT WOUND (RED
WINDING CONE), WHICH GOES ON THE RIGHT HAND SIDE OR LEFT WOUND (BLACK WIND-
ING CONE), WHICH GOES ON THE LEFT HAND SIDE.
IMPORTANT:
ON SINGLE SPRING APPLICATIONS, ONLY A LEFT WOUND (BLACK WINDING
CONE), WHICH GOES ON THE LEFT HAND SIDE IS REQUIRED.
NOTE:
The set screws used on all torsion winding cones and cable drums are colored red.
DO NOT identify right and left hand by the set screw color.
IF YOU DON’T HAVE A COUPLER ASSEMBLY:
Facing the inside of the door, lay the torsion
shaft on the floor. Lay the torsion spring with the red winding cone at the right end of the
torsion shaft. Lay the torsion spring with the black winding cone at the left end of the torsion
shaft. Slide the center bracket bearing onto the torsion shaft followed by the torsion springs
and set collars (if applicable).
IMPORTANT:
THE CENTER BRACKET BEARING / TORSION SPRING(S) AND THE SET COL-
LARS (IF APPLICABLE) MUST BE POSITIONED, AS SHOWN.
Torsion
shaft
Left wound, black winding
cone (left hand side)
Right wound, red
winding cone
(right hand side)
IMPORTANT:
ON SINGLE SPRING APPLICATIONS, ONLY
A LEFT WOUND (BLACK WINDING CONE), IS REQUIRED.
NOTE:
Layout counterbalance
parts in proper orientation, then
install onto torsion shaft, as shown.
Set collar (if
applicable)
Set collar (if
applicable)
Set collar (if
applicable)
Set collar (if
applicable)
Center
bearing
bracket
With assistance, pick up the torsion spring assembly and slide one end of the torsion shaft
/ torsion keyed shaft through one end bearing bracket. Lay the middle of the torsion shaft /
torsion keyed shaft into the center bracket. Slide the other end of the torsion shaft / torsion
keyed shaft into the other end bearing bracket. Position the torsion shaft / torsion keyed shaft
so that equal amounts of the shaft extend from each end bearing bracket.
Left
hand
end
bearing
bracket
Center
bracket
Torsion spring
assembly
Right hand end
bearing bracket
Torsion spring
assembly
Center
bearing
bracket
Or
Torsion
shaft
Right hand end
bearing bracket
NOTE:
Position the
torsion shaft so that
equal amounts of the
shaft extend from each
end bearing bracket.
Torsion
shaft
Left hand end
bearing bracket
IF YOU HAVE A COUPLER ASSEMBLY:
Disassemble the coupler assembly by removing the
(3) 3/8” - 16 x 1-3/4” hex head screws and the (3) 3/8” - 16 nylon hex lock nuts from the
coupler halves. Loosen the set screws. Set the components aside.
9
Summary of Contents for 8700
Page 17: ......