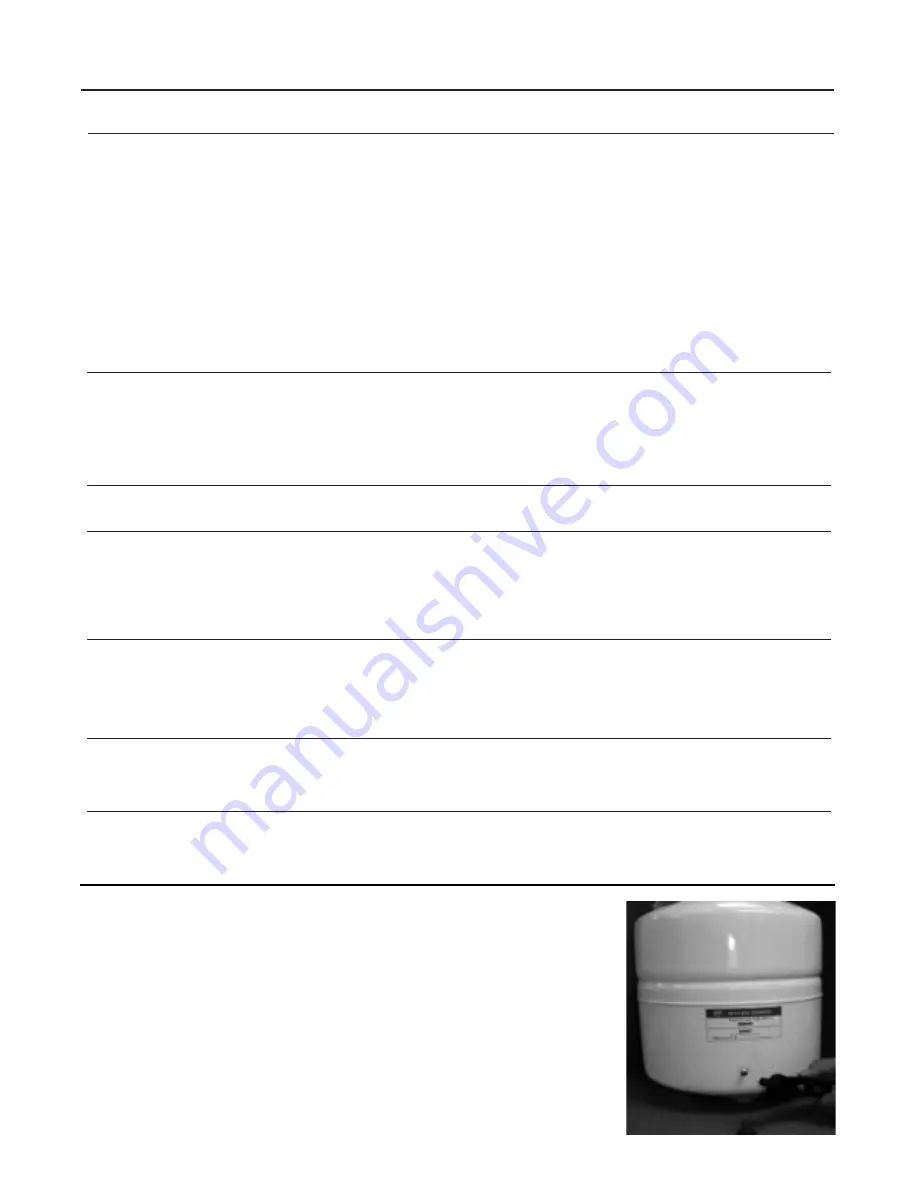
Troubleshooting
Problem
Cause
Solutions
Low/slow production
Excessive air pressure in tank
Relieve pressure at schrader valve on tank
(set to 7psi with the tank empty)
Pump not operating
Wiring connection broken (plug 110 AC wall
plug back in at wall and/or reconnect the 24
VAC wire harness connectors)
Replace pump if needed
Fouled membrane
Replace membrane
Plugged pre-filters
Replace filters
Crimped tubing
Check tubes to make sure they are
not kinked
Angle stop or water line valve
Ensure valves are opened by turning valve
not fully opened
handle counter clockwise until it stops
Milky colored water
Air in the system
Air in the system is a normal occurrence
with initial start up of the RO system. This
milky look will disappear during normal use
within 1-2 weeks. If condition reoccurs after
filter changes, drain tank 1 to 2 times.
Faucet Dripping
Needs adjustment
see page 12
Pump short cycles
Ball valve on tank closed
Open the ball valve on the top of the tank
Blue tube blocked between
Remove kinked/damaged section and
the tank and RO system
replace if necessary Call for
Faulty pressure switch
technical support
Bowl leaks at the top after
Damaged/Dry O-ring
Lubricate with water soluble lubricant
changing the filters
or replace O-ring as necessary
(Do not use Vaseline
®
or other
petroleum based lubricants)
Pump constantly running
Electrical fault
Call for technical support. Close faucet
Faucet left on
and let tank fill for 2 to 3 hours.
Plugged pre-filters
Replace filters
11
Checking air pressure in tank
Note:
Check air pressure when tank is empty.
Step 1
Open faucet and drain the tank.
Step 2
Using a digital air gauge check the air pressure in the tank. There should
always be between 5-7psi.
Step 3
If you have more than 7psi release air and recheck. If you have less than
5psi, add air. Air can be added with a bicycle pump.